Technical Anodizing
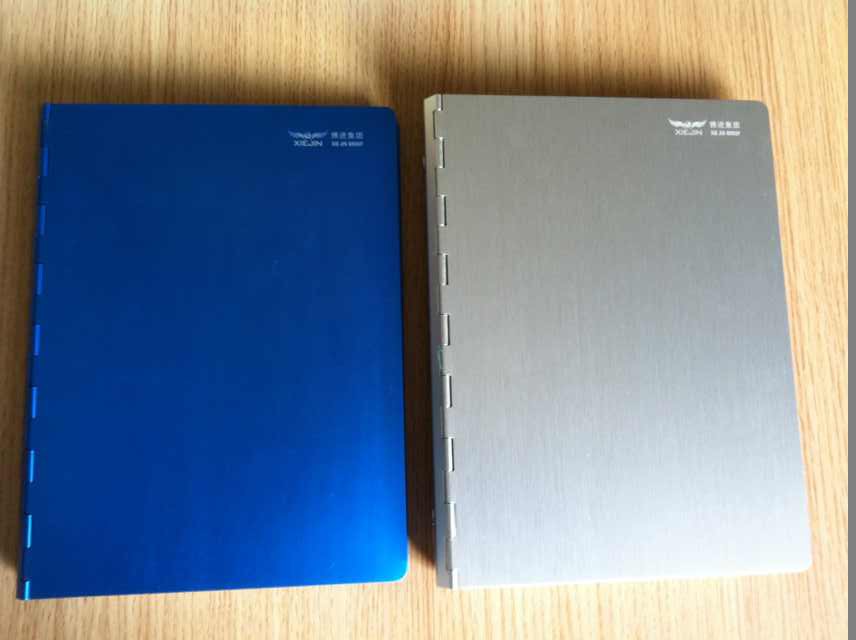
Sulphuric acid anodizing, better known as normal anodizing is a coating developed for the functional and decorative improvement of Aluminum parts. The coating is performed in an acid electrolyte at temperatures slightly below room temperature. The parts are connected with the anode and, in the course of the treatment, the parts surface is converted into an Aluminum oxide layer.
The layer thickness to be achieved depends on the application, the properties to be obtained by the layer and the subsequent resistance. For most applications, layer thickness values ranging from 5 to 20 μm can be obtained. The oxide layer builds up for 1/3 on the aluminum and for 2/3 in the aluminum. This property must be considered when making components when it comes to their fit. However, there is also the possibility to intervene to ensure dimensional accuracy and hence the fit. Nearly all wrought, cast and die-cast Aluminum alloys destined for industrial can be anodized. However, the alloy has great influence on the color of the anodized part. An alloy out of the 3.000 series has grey colour, a 7.000 alloy has more gold appearance.