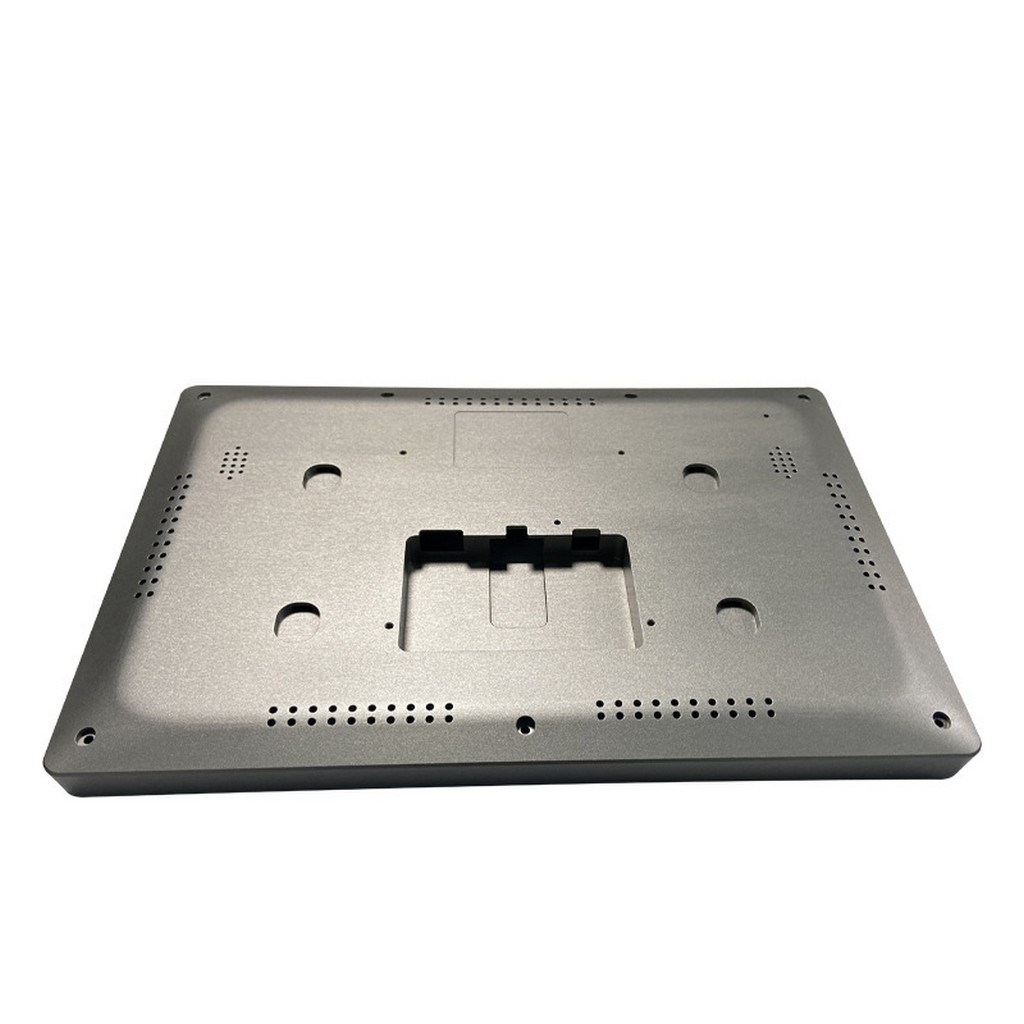
Financial state and efficiency are simply two great make use of the expire casting process.
XJ EmployeesIf you are looking for the most cost- effective, efficient technology to create your element in a durable and strict metal form, the high- pressure die casting process is the solution. It offers the broadest array of shapes when compared with other manufacturing techniques. Likewise, the ruthless die casting process offers a high amount of dimensional accuracy while offering:
Developmentof complex shapes with limited tolerances
Slimwall metal libéralité
Higherproduction rates
Lengthylifespan
Cheapestper part piece price
Great things about Die Casting
Perish casting is an effectual , cost- effective process able of manufacturing a broader array of shapes and components than any other metal throwing or forming techniques. Die solid parts routinely have an extended lifespan and usually are created to complement the encircling part 's overall look. Designers can gain several advantages through the use of die-cast parts, such as for example:
High- speed production: Perish castings may be produced into complex shapes with closer tolerances than most mass production procedures. Usually, minimal engineering is necessary, meaning numerous similar parts may be produced before additional tooling is necessary.
Dimensional accuracy and stability: Die throwing produces durable and dimensionally steady parts while keeping close tolerances.
EMI and RFI shielding: Expire cast parts may also be warmth and UV resistant and supply EMI and RFI shielding.
Power and weight: Generally, die solid parts are superior to plastic-type material injection moldings and tend to be better and lighter than parts produced from other casting methods.
Pass awayCasting Process Summary
The die casting process contains many steps, but it could be separated simply. There are two styles of die throwing methods, hot chamber and chilly chamber die casting. Hot holding chamber die casting can be sent applications for parts created from zinc or magnesium. During this method, the alloys are melted on the die casting machine itself, plus the molten metal enters the "gooseneck" automatically. The hydraulic- powered vertical piston then causes the metal from the gooseneck and to the die.
Chilly chamber die casting enables you to cast aluminum parts. During this method, large quantities of aluminum are melted in a different furnace and used in the die sending your line machine, where it's preserved the "holding furnace". If the cycle starts, a certain amount of molten metal is "ladled" into an unheated injection cyndrical tube, and also a horizontally mounted hydraulic piston pushes it in to the die.
The full total cycle an opportunity to go from liquid metal to a good die-cast part can differ from project- to- project– some cycles may last one second or less, some may previous for just two- to- three full minutes. Following renforcement from the metal in the die cavity, the equipment 's hydraulic clamping system releases the moving die half, allowing the disposition system to advertise the casting out side in the mold. Castings are then utilized in the next stage along the way ( such as for instance die trim) to eliminate excess material– like gateways, runners, overflows, and flash– from the business.
Typically the XJ Difference
XIEJIN offers design help from your personnel of exceedingly qualified engineers. XIEJIN now offers in- house COMPUTER NUMERICAL CONTROL facilities, and use experienced toolmakers to greatly help ensure a good product. The following hands- on approach even goes in terms of to help develop different finishes for your product by handling outside finishing companies to assist you to get the most cost- effective, socially responsible solution.
Request a quote today on the custom die casting solution for the application, or contact Chicago Light Metal to find out more .