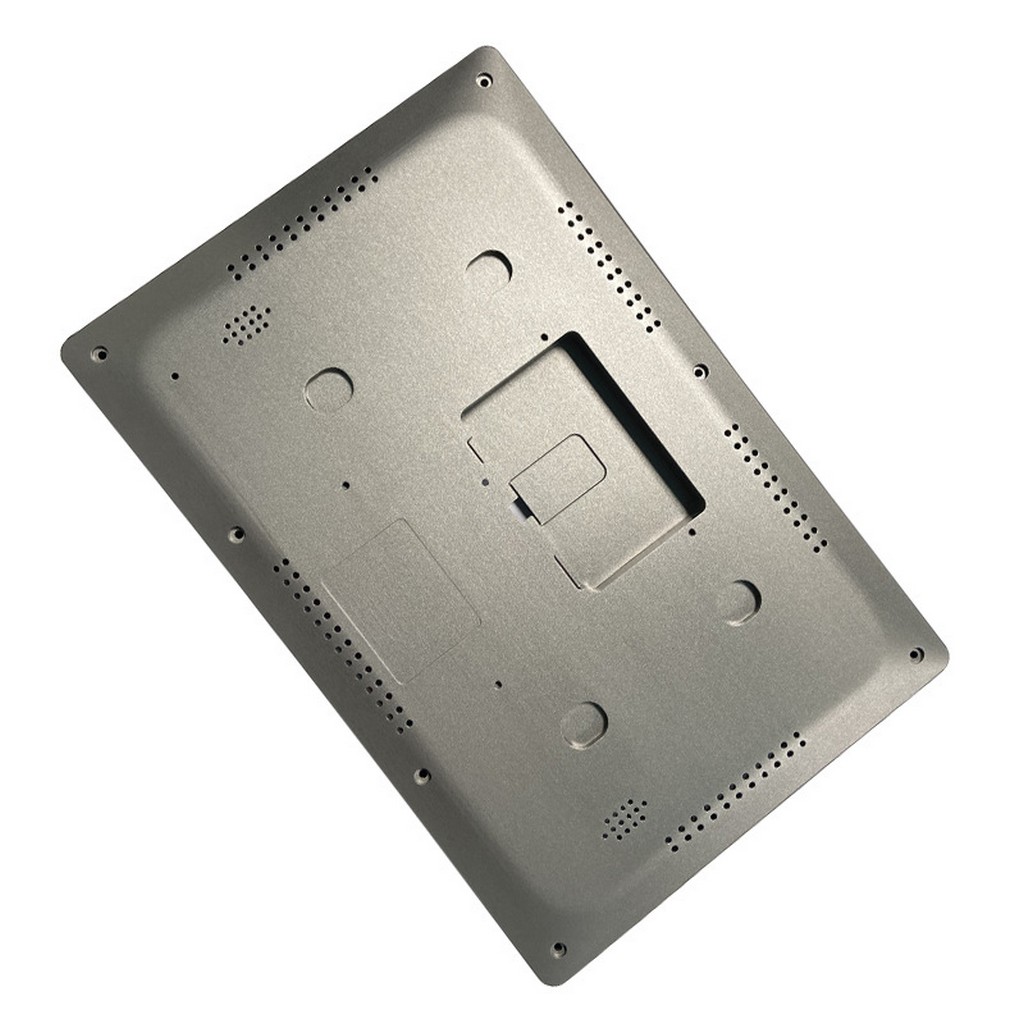
Cease to call home Casting for Fabrication of fabric Components and Structures
Findings
Expire casting is a vital technology for metal manufacturing in plenty of contemporary commercial fields. In these chapter, the essential, mechanism and characteristics of die casting plan of action and its own classification and app are symmetrically introduced. Designproductivity of die casting application may be presented, which include design of castings, dies, casting plan of action and the amount of casting metals, process parameters and casting tools. To cut backconduct a feasible and efficient die casting process creation, CAE simulation could be a great efficient method to lessen layout and development lead- time frame. A simulation- enabled circumstance study of die casting plan of action design can be fond of show its efficiency. Through these research study, using numerical ruse to disclose the associativity amid the actual casting process, building, simulation, and simulation output aspects is presented. An activity a substantial based simulation methodology for couples casting defects plus the ruse process, procedure and analysis from defect occurrence in casting plan of action are systematically presented and delineated.
Die casting process is essentially employed for nonferrous materials with good fluidity and low running temperature such as for instance zinc and its own alloys, copper, aluminum, brass, magnesium, and tin- based metals. Approximately 50% of gears produced from zinc- based alloys are actually created by the die audition process. 14 Die-cast armor and weapon upgrades are used in various industries and appliances such as for example automobile, jetstream, machine and saw, musical instruments, cameras, business machines, washing models, gear pumps, small speed reducers, lawn movers, and household appliances. 4 This method allows making of gears with higher level of accuracy and repeatability. Shape 14 depicts various kinds from miniature gears made from zinc and manufacture by die sending your line process.
The die casting plan of action is just a name directed at metal casting processes that assist metal molds or long haul dies. There actually are plenty of distinct processes included under the typical name. The die audition process actually has three most significant sub- processes. These are actually :( 1) ongoing mold casting, even called gravity die casting,( 2) low- XIEJIN audition, and( 3) high- tension die casting. These processes change mainly in the total amount from pressure that's useful to force the molten metal straight into the die. The advantages from such an activity include excessive production rates, exceptional dimensional repeatability, low part costs, and reduced machining because of reduced audition finish stock. The truly amazing temperature transfer rate obtained by may mean of metal molds can additionally refine and improve the last cast structure, so also the yellow, mechanical properties, with all the castings. The disadvantages are design limitations likely to metal dies, higher primary die cost, and longer lead moment for die construction for becomes the die induced by way of a casting design transformation.
Die- casting is a good economical way increase significant amounts of complicated shaped products of mild metals with finely-detailed. Dissolved metals are introduced several high-speed with your water a significant cooled metal die or mould through a shot process]one particular, 2]. The molten metal converts into a good when for connection with the cool liquid. Once the solidification and mold casting process has completed, the mold is opened in addition to disposition of parts initiated using a technical activation in the ejector stakes. The die is subsequently encountered with air, sprayed using a grease, closed, and molten metal being injected again to the die to perform the cycle.
About one half the global aluminum combination casts are produced utilizing the gravitational die casting process in addition to questionable die casting( HPDC), within the automotive industries. The main financial benefits linked to the strategy include producing ordonnance with smooth surface finishes, close dimensional tolerances, and fine, complicated details at high production charges. However, as a result of thermal and mechanical cyclic loadings and response when using introduced molten metal, expire casting dies are susceptible to serious damage, including erosion, chemical type attack, gross cracking, and cold temperatures cracking]3–5]. Die damages improve manufacturing costs and lower the casting quality. When using strengthening quantity of die casting from aluminum, destruction to the dies becomes a critical difficulty. Some great benefits of die audition are offset with a magnitude from the costly the cease to reside predicated on its intricacy and complexity, the die also can charge more than machinery employed to use it]6, 7].
The casting of aluminum metals requires die steels with an increase of toughness and strength. Thus, expire steels become more pricey and hard to be machined. A normal cease to exist utilized in aluminum expire casting ranges from 100, 1000 to 150, 000 castings. Strengthening the amount of parts to become company from a particular die may lower the purchase price with the method. However, additional costs are incurred the minute it comes with an interruption using the casting process or when truth be told there is a purpose to service or replace dies. Along withgo up within the manufacturing life from the die with a improvement from your die steel along with elimination of die failure can chip in to earnings of cease to call home casting operations. About$ 200 several may be saved yearly in america by enhancing the cease to exist with just 20% your lifetime extension. This estimate began around the yearly mold creating of$ 1, 000, 000, 1000 inside the US]8, 9]. Plus thereduction in the commercial lead process along with the time from designing is essential for the reduced amount of the sum total tariff of the casting process. The sun and rain of the mold will get defined sharply with textured surface types, which makes them suited to a huge variety serviceable finishes. The influence of various process parameters was examined right after the machining of die company parts. Different parameters such as the temperature from the molten material, the immersion from the smelted metal, plus the cooling program were examined
XIEJIN sending your line involves squeezing molten metal right mould cavity under excessive pressure and holding the metal under great pressure during renforcement, as demonstrated in Fig. several. 7. Pressure is applied through the action of the hydraulic piston ram that injects smelted metal via a steel expire and in to the mould. The proceduremetal casting is removed from your mould following solidification, and the method repeated utilising the same long haul mould. The procedure is great for rather higher rate production because of the fast solidification rate using the casting. Many aluminium and magnesium alloys are cast using these method.
XIEJIN castings can typically be made more sound within local areas by the usage of contract pins. Such techniques are located in the course of keeping the client happy by appearing to get a sounder casting. The theory is doubtful if strength may be improved, but leak tightness could, obviously, benefit. When dealing with the way of Al– Si– Cu other metals Wan and colleagues( 2002) located that this Cu was crammed out of the highly pressurised region, reducing in concentration via 2. 6 to at least one. 6% Cu, and was segregated to the outer lining regions round the pin.
XIEJIN castings could possibly be made more sound present in local areas by the use of contract pins. Such techniques are located in the course of keeping the client happy by appearing to realise a sounder casting. The concept is doubtful if strength features been enhanced, but leak firmness would, certainly, benefit. When dealing with the pattern of Al a substantial Si- Cu alloys, Wan and colleagues( 2002) found the fact the Cu was squeezed away from highly pressurised place, reducing in concentration from some. 6% to at least one. 6% Cu, and was segregated to the outer lining regions concerning the pin.
For HPDC, molten aluminium is needed right into a steel die from a narrow orifice( or gate) at high speeds ranging via 20 to 100 m s i9000? 1( Fig. 3. 13). Here i will discuss accomplished by means from the piston and cylinder( or hot sleeve) where in fact the cilindro is driven with a hydraulic ram effective at exerting some pressure around 100 MPa inside the metal. The target can be to keep feeding the sending your line since it solidifies rapidly within the die. These portions address two difficulties with alloy collection for die casting of lightweight alloy alloys: die soldering and warm treatment.