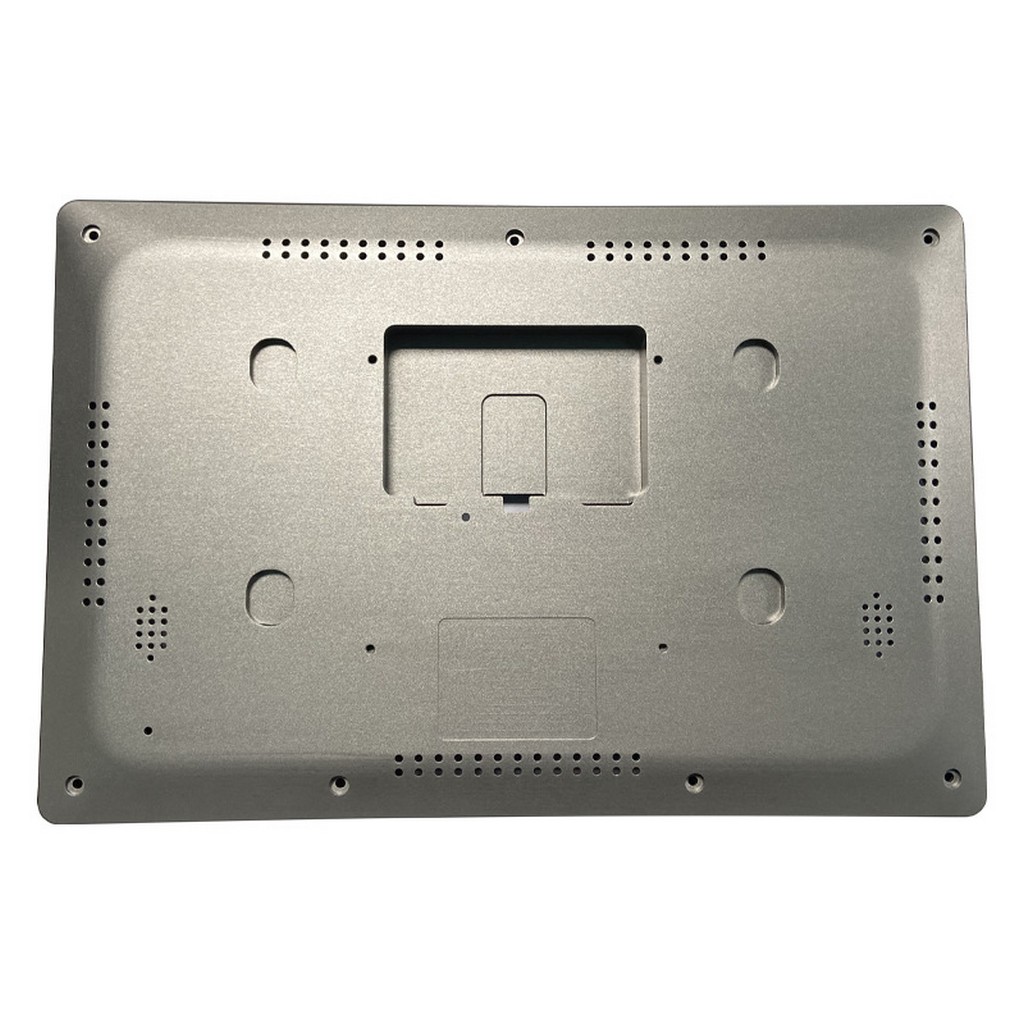
XIEJIN works together partners with the most recent die casting technology to supply top quality, on-- demand parts. Our typical threshold accuracy ranges from ±0. 0762 mm to ±0. 127 millimeter for aluminium and zinc, dedicated to customer specifications.
Hot holding chamber casting, likewise known as because gooseneck casting, has become the ubiquitous expire casting process. With this method, the injection mechanism 's chamber is immersed in molten metal as well as the "gooseneck" metal supply structure courses the molten metal in the expire cavity.
Cold chamber die spreading is often employed to lessen machine corrosion. The liquified metallic is loaded into the injection setup, removing the wish to submerge the injection system into the molten metal.
Great things about Die Casting with XIEJIN
SpeedyTurnaround
QuickTurnaround
We offer fast mould lead times: on when 12 organization days for rapid tooling or over to twenty days meant for production tooling.
DramónProduction
Dramón Production
Perfect for the creation beginning 100 parts.
EndlessOptions
UnlimitedChoices
Several diverse materials for a large number of mixtures of finishes, tolerances and marks. We also provide material qualifications, inspections and measurement reports.
Within- house quality control
Present in- house quality control
Rigid in- house QC to make sure your parts are perfect. Our processes are ISO 9001: 2015 certified.
PerishCasting Components
Aluminum
Aluminium lightweightA380| SOBRE AC- 46500| AlSi8Cu3
AluminumADC12| A383| AlSi11Cu3
Zinc
Zamak zinc metals
PerishCasting Finishing Options
Whilst- Solid
Parts made via zinc and zinc- aluminum have a reasonable resistance from corrode as- cast and is also remaining within this state. Alternatively , magnesium and aluminum need a coating to be corrode resistant.
Anodising( Type II or simply Type III)
Aluminium parts will often be anodised. Type II( sulphuric acid) anodising brings about a corrode- resistant oxide finish upon the business 's surface. Parts could be anodised in a number of colours, with black, gold, clear, and reddish.
Type III( hard) anodising outcomes within a thicker surface coating and constitutes a wear-- resistant layer combined with the corrosion resistance for sale in type II anodising. Anodised parts perform not conduct electricity.
Natural powderCovering
Each of the parts created from expire casting undergo powder coating. On this technique, a component is generally electrostatically sprayed with powdered color and subsequently baked in a fantastic oven.
Custom madeFinish
Additional digesting and finishes according to the requirements.