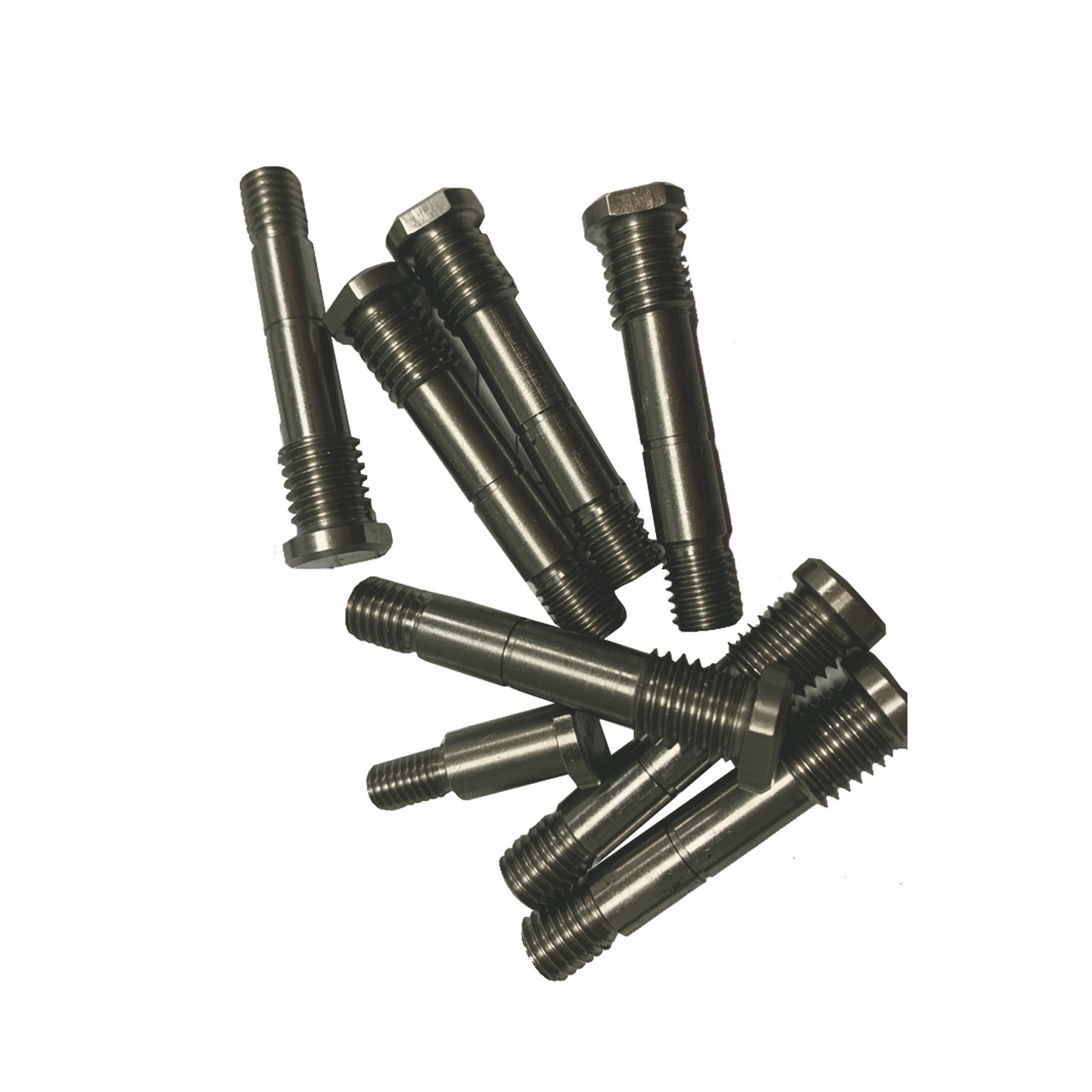
Making is the applying lathes to eradicate material from the outer layer diameter in the rotating workpiece. Single- point tools shear metal from your workpiece on( ideally) short, distinct, easily recyclable chips.
CNC lathes with standard surface speed control encourage the master to select a surface velocity, then the device automatically modifies the rpm since the reducing tool transverses the number of diameters along the outer layer profile from your workpiece. Modern lathes even ship in single- turret gun and two- turret constructions, with single- turret models possessing a horizontal and head to feet axis and double- turret gun machines having one horizontal and vertical axis pair for pretty much every single turret.
ShowcasedCONTENT
The easiest method to Passivate Steel Parts
Engineering Questions? Ask Our Newest Writer
Open up your Own Machine Store? Here's Suggestions about Starting Modest
Early turning tools became solid, rectangular items of excessive- speed steel with rake and clearance angles on a particular end. If the tool dulled, machinists would sharpen it within a pedestal grinder to be used. High- speed steel equipment continue to be common on elderly turning machines, but carbide features become trusted, specially in brazed single- point form. Carbide sports better wear resistance and hardness, resulting in better production and tool life, however it can cost more and competence to resharpen.
Ratesand Passes
Turning is a mix from linear( tool) and rotational( workpiece) movement. Thus, cutting speed is unquestionably understood to be the rotational mileage( recorded as sfm— exterior feet each and every minute— in addition to smm— square meters every sixty seconds— traveled in a particular minute by a justification in the business surface). Feed charge( recorded in inches or millimeters per revolution) may be the step- wise distance the tool trips along or across a workpiece surface. Feed is regularily expressed since the linear long-distance the tool travels in just a little( in. /min or mm/ min).
Supply rate requirements vary relative to the operation 's purpose. In roughing, one of these is, excessive feeds are usually better related to maximizing metal removal rates, although require high part rigidity and machine power. Endturning, for the time being , might slow up the supply rate to make the outer lining complete specified on the business plan.
Fundamentalsof Tool Angles
Trimming tools 'effectiveness depends mainly around the tool 's angle based on the workpiece. The defined with it reference inserts to specify cutting and relief angles, and will also affect brazed single- point tools.
Premier rake angle( also known as backside rake angle) is the attitude formed between your angle from inclination from the insert along with line perpendicular towards the workpiece when viewing the tool via the medial side, front to rear. The surface of therake is positive the minute it slopes downward through the cutting point and in to the shank, neutral once the series through the the surface of the insert is parallel using the the surface of the shank, and negative mainly because it slopes way up from your cutting point and also a shank. Inserts and toolholders are often categorized as excellent or negative. Positive inserts include angled sides and mount in toolholders with positive top and side rake angles. Negative inserts have square sides in accordance with the very best encounter from the insert and mount into toolholders with negative top and aspect rake angles. Top rake viewpoint is specialize in that that is reliant on the angles in the insert— your positive ground or even a cast chipbreaker can affect the powerful top rake angle from bad to positive. Top rake coins also are usually better with softer and much more ductile workpiece materials, which require substantial positive shearing angles, while harder and tougher materials are finest cut with neutral or undesirable geometries.
Side rake angles are in reality formed between your encounter with the insert and the number perpendicular for your workpiece when observing the conclusion. These angles will stay positive if they slope independent of the leading edge, simple if they are perpendicular for the leading edge, and bad when they slope upward. The it could be thickness in the tool are likely to depend quietly rake angle, with smaller angles including thicker tools that increase toughness but require higher cutting pushes. Larger angles produce thinner poker chips and decrease cutting force desires, but past a maximum encouraged angle, the leading edge weakens and heat transfer diminishes.
End innovative angles form between the insert leading edge at the conclusion in the instrument and also a line perpendicular directly to the backside side from the tool shank. This angle can determine the clearance involving the reducing tool in addition to finished surface through the workpiece.
Located under the end leading edge, the end relief angle forms between your end encounter through the put along with a line perpendicular to the root of the toolholder. Tip overhang can associated with end clearance angle( which is often formed right at the end confront in the toolholder plus some line perpendicular on the beds base through the toolholder) bigger than the relief angle.
Side relief perspective describes the angle under the side leading edge. It may be formed by along side it confront in the insert plus some line perpendicular to the essential from the toolholder. As with all the end relief angle, hint overhang can make the location clearance angle( formed by along side it deal with from the toolholder and also a line perpendicular on the root of the toolholder) increased compared to the relief angle.
Severalsecond of the lathe advancing a cutting tool having a workpiece undergoing turning
Charge perspective( also known as the side revolutionary angle and also the attack angle) forms between your insert area leading edge in addition to side through the tool shank. The attitude leads the tool with your workpiece, and enlarging it produces much wider, thinner chips. The datageometry through the workpiece and the data condition are primary considerations at any time selecting charge angle to acquire a cutting tool. For case, tools with emphasized lead coins permit respectable productivity rates at any time slicing through scale, interruptions or even hardened surfaces, without subjecting the cutting tool edge to severe shock. Operators must balance that benefit against increased part deviation and vibration, as larger business lead angles create higher radial makes. Zero- degree lead viewpoint turning tools produce chips even wide for the making operation 's cutting depth, while business lead angle cutting tools make effective cutting depth and matching chip width exceed the actual cutting depth around the workpiece. Most turning functions are efficiently performed in just a lead viewpoint selection of 10 to twenty nine degrees( metric systems invert the angle from 90 degrees, building the perfect lead angle collection 80 to 60 degrees).
Enough relief and clearance angles are already both necessary around the arrive at a finish and along side it for that tool to enter the reduced. Lacking the necessaryclearance, chip formation can't occur, but lacking the necessary alleviation, the cutter will rub and produce heat. Single- stage turning tools additionally require end and side clearance angles to the particular cut.
Turning topics workpieces to tangential, radial and axial cutting forces. Tangential pressure has the maximum effect on energy consumption, axial( feed) force applies pressure with the part in the longitudinal direction, and gigantic( depth of cut) force generally seems to push the workpiece and toolbar apart. "Cutting force" is generally the sum most three during these forces. Having a zero- degree lead angle, right now there is a ratio of 4 SYM 2 SYM 1( tangential: axial: radial). As charge angle raises, the axial force shrinks as well as the radial cutting force develops.
Toolholder style, nose radius and insert condition likewise have serious impacts on the actual optimum effective leading edge length in turning inserts. Certain insert radius and toolholder combinations might need dimensional compensation to create complete use of this cutting advantage.
Nasal areaRadius and Surface End
Surface finish within a changing is determined by the solidity in the tool, machine and workpiece. Once rigidity is guaranteed, the partnership between the gear feed( in. /rev or logistik. /rev) plus the nose contours in the insert or slicing tool to look for the workpiece 's surface finish. The nose contours is expressed like a radius— up to a certain point, a bigger radius converts to raised surface finish, nevertheless too big of any radius may easily introduce chatter. For machining capabilities where a compact- instead of - optimum radius is important, nourish rate might need to become reduced for the required end.
Output
After attaining the ideal amount of power, productivity raises alongside increases to depth from cut, feed rate and rate.
Depth of cut is the most basic of the to boost, nevertheless improvements are possible only then is sufficient material and power for this. Doubling interesting depth of cut doubles productivity in no increase to cutting heat, tensile strength (ts) or cutting pressure per cubic inch or centimeter removed( also referred to as this cutting force). It doubles the mandatory power, but so extended since the tool meets tangential cutting force requirements, there is normally no decrease in tool life.
Nourish rate is also easy to alter. Doubling the feed price makes chips doubly thicker, and increases( but does not necessarily double) tangential cutting force, trimming temperature and required power. This sort of change lowers tool life, yet wont halve it. Specific trimming force( the cutting force found in terms of the amount of material removed) also decreases with a rise of feed level. The excess force imposed concerning the leading edge with elevated feed rates may bring about the cratering of the best rake insert surface because of the increased temperature and scrubbing throughout the cut. Operators should monitor this variable carefully in order to avoid catastrophic failure the spot that the brand becomes a lot better than the spot that the.
In comparison to depth of slice and feed rate changes, raising cutting speed is ill-- advised. Speed increases cause significant increases in cutting temperature and lower both tangential and particular cutting forces. Doubling the trimming speed requires additional power whilst reducing tool life by over fifty percent . The particular load upon the most notable rake face may lower, but the bigger trimming temperatures could cause cratering.
Fine-tuningTurning
Insert wear can be quite a common indicator of accomplishment or failure for almost any making operation. Other common indicators contain unacceptable chips and workpiece or simply machine problems. Generally, operators need to index their inserts at zero. 030 "( 0. 77 mm) flank wear. For finishing operations, providers should perform indexing at zero. 015 "( 0. 38 mm) or maybe sooner.
Another of an excellent lathe functioning on a workpiece
Toolholder Identification
Mechanically clamping indexable insert holders follow nine requirements inside the ISO and AMERICAN NATIONAL STANDARDS INSTITUTE identification system.
The very first notice in the machine indicates the insert clamping method. Four prevalent types dominate, nevertheless they every encompass several variants.
C inserts start using a best clamp for inserts that perform not want a middle opening. This method relies totally about friction and is most beneficial with positive rake inserts in moderate to light turning, as effective as boring operations.
M inserts force the insert contrary to the pocket wall using a cam lockpin that secures the protective place pocket shim. The top clamp keeps the trunk of the area and keeps it from raising each time a cutting load affects the insert 's nose. M inserts are very helpful for negative rake inserts having a middle hole on medium to heavy turning businesses.
S inserts use an inconvenience- free torx or allen head bolt, but require counterbores or countersinks. The screws can seize with heat, so this technique is top for light to medium resorting functions and boring operations.
S inserts would be the ISO normal for turning tools, and power the insert from the pocket or purse walls with a pivoted lever the truth that tilts or if you adjustment screw could be seated. These inserts are top for negative rake inserts with holes in medium to hefty turning operations, nevertheless they simply do not restrict the insert from lifting through the cut.
The 2nd section ideal for the letter to make reference to the insert shape. Another section runs on the letter to connect with the blend from straight or offset shank and lead angle.
Fourth is some letter to point the display rack rake angle or insert measurement angle. For rake angles, L is a confident rake wherever the sum the conclusion clearance angle and wedge viewpoint is no more than 90 certifications, N is made for a poor rake where sum of each one of these angles is over 90 deg, and O will work for neutral rakes where in fact the sum is exclusively 90 degrees. Exact clearance aspects are indicated with among the numerous correspondence.
Fifth is just a letter the fact indicates the hand in the tool. R implies that the tool serves as a right- side tool that cuts from ideal to left, while L fits to left- hand equipment that cut from left to right. N tools are easy, and can reduce from sometimes direction.
The sixth and 7th sections differ between imperial and metric measurement systems. Inside the imperial system, these sections concur to some two- number number indicating the holder get across- section. For square shanks the amount shows the final amount of sixteenths of breadth and height( 5/8 "being the spot that the changeover happens from" 0x "to" xx "), while rectangular holders utilize first digit to symbolize the eighths of width and the next digit for quarters from height. There are numerous exceptions to these system, such as for example toolholders 1 "?× 1? ", built to utilize the designation 91. The metric system uses two a substantial digit numbers to symbolize the millimeters for both height and width( because order). And thus, an oblong insert 15 milimetre tall and 5 milimetre wide might have some quantity of 1505.
The 8th and ninth sections also change between imperial and metric programs. For imperial systems, section almost 8 describes insert size, when section 9 covers surface and tool length. The insert specifications is dependent upon the specifications of your inscribed circle within increments of eighths of the great inch. The outer lining and instrument length are letter- based mostly, having a- G related to the sizes of qualified backside and end tools and L- U( without Um or Q) for qualified entrance and end tools. Inside the metric system, section 8 concerns the tool length, and section 9 refers to set up size. Tool length representation is unquestionably letter- based, while to obtain insert size, rectangular and parallelogram shapes use lots to point the entire longest leading edge in millimeters, disregarding decimals and preceding an individual- digit numbers along with your zero. Other shapes use aspect length( diameter for round inserts) in millimeters, also disregarding decimals and preceding one- number numbers utilizing a zero.
The metric system works on the tenth and last section to include a provision to have qualified holders which might have tolerances of ±0. 08 logistik for and also end( Q), front and end( F), and back, front and end measurements( B).
Brazed Single- Level Tools
Single- point equipment can be found in many models and sizes, using a number in materials. Solid single- level tools can be created by high- speed steel, skin tightening and steel, cobalt alloy or carbide. However, the trouble of such tools made them mainly irrelevant as a offers looked to brazed- likely turning tools.
Brazed- suggestion tools work with a body in inexpensive material and a touch or blank of higher priced cutting material brazed towards trimming point. Tip materials include large- speed steel, carbides and cubic boron nitride. They are in fact for sale in sizes A although G, with offset point designs A, B, E, F and G all available as possibly right- or left-- hand cutting tools. For rectangular shanks, the quantity following the letter designation indicates the elevation or width of the unit in sixteenths of the inches. For rectangular shanked tools, the initial number is the sum total eighths from the inch of shank width, along with the second number is normally the sum total of fourths in a inch of shank level.
The nose radius of brazed- tip tools pertains to the shank size, and workers should take the time to match with tool size in order to complete desires.
SpecialisedTools for Boring
Monotonous is mainly used for finish large, cored holes in diffusion or pierced holes in forgings. Most tools resemble those in traditional, external making, but cutting angles are specifically critical because of chip movement concerns.
A newof any lathe boring a workpiece
Rigidity is likewise paramount to productivity in monotonous. The utmostdiameter from the gap plus the need for more computer chip removal clearance directly influence the most scale the monotonous bar. Practical overhang for stainlesss steel boring bars is four instances their shank diameter. Exceeding that limit compromises the metal removals rate because of loss from rigidity and increased vibration likelihood.
Diameter, material modulus of suppleness, length and cargo around the beam influence rigidity and deviation, with diameter providing the effect and length the 2nd supports largest. Increasing the line dimension or shortening length will remarkably increase rigidity.
Modulus of suppleness is specific to the info used and alter with heat treating. Steel is the smallest amount of stable at 30, 1000, 000 psi, with rock for 45, 000, 000 psi and carbide at 90, 000, 1000 psi.
The same , such are high numbers for stableness, and steel shank boring discos offer satisfactory performance for a lot of functions up to length/ diameter ratio of 4 SYM 1. Tungsten carbide shank boring bars succeed up to length/ diameter proportion of 6 SYM 1.
TrimmingApplication Geometry in Boring
Radial and axial cutting forces in drab are influenced by the company lead angle. The increased axial push of a little lead perspective may be especially useful during reducing vibration. As the company lead angle increases, radial forces enhance and increase the forces perpendicular for the direction within the cut, surrounding to vibration.
Recommended lead coins to manage vibrations in monotonous are between 0 degrees and 15 degrees( in the actual system. Within the metric program, this can be 90 degrees to seventy- five degrees). In a lead viewpoint of 15 degrees, radial lowering forces are almost twice because high than in a zero- degree lead angle.
Great rake angle cutting tools will undoubtedly be preferable for most boring functions on order to cut back cutting causes. However, small clearance sides of positive rake angle equipment require operators to plan regarding the of contact between your tool in addition to workpiece. That is certainly particularly significant to ensure an excellent enough clearance angle whenever a bummer small diameter holes.
Radial and tangential forces in boring characteristics increase because the nose radius increases, require forces are in fact also at the mercy of the company lead angle. Thesedepth of lower of boring functions may change these relationship: when the depth from cut is more than along with add because of the nose radius, business lead angle determines the radial pushes. If the depth of cut could be lower than the nose radius, the cutting depth itself improves the radial forces. This challenge creates it particularly significant operators utilize a nose radius smaller weighed against how a cutting depth.