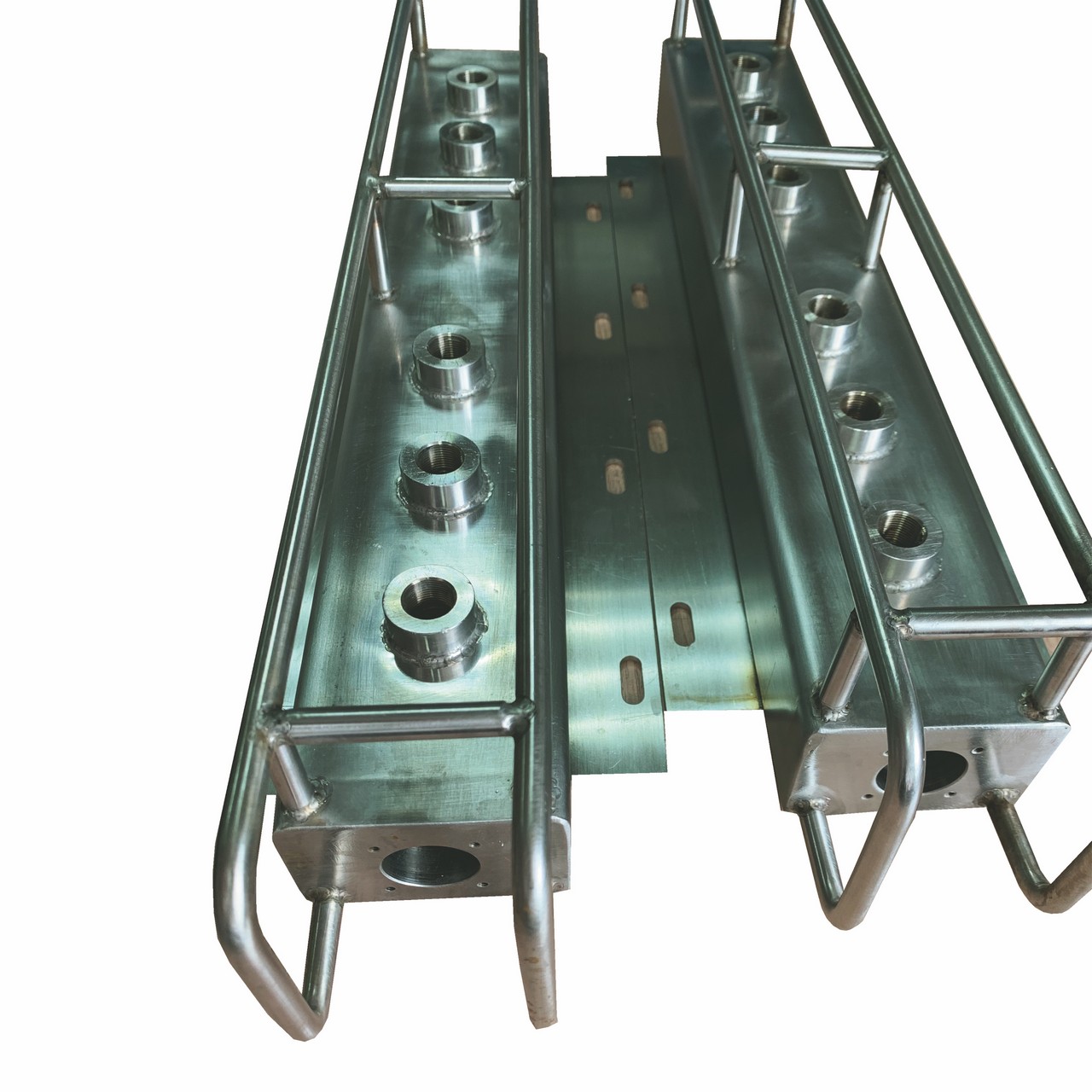
XIEJIN expertise: The Supply Chain.
XIEJIN thanks the Health Care workers who have valiantly carried us through Covid 19. Also thanks to the food and service workers for keeping us fed, the trades who keep it working, and drivers for keeping it moving!
XIEJIN is a provider of components necessary to support First Responders and Health Care Workers.
XIEJIN is an essential service.
We thank our staff, customers and vendors for their dedication to protocol, allowing efficient operation.
We can help manage your internationally sourced projects.
We can on shore components to reduce supply chain risk.
XIEJIN is proud of how our dedicated employees and expertise have met the challenges of 2020-21. We see a bright future and appreciate the valued relationships with our Customers and Vendors. All the best to your continued success.
Overview: How Injection molding works?
The Basics Of Injection Molding Service
Injection molding is one of the most often-used manufacturing processes for creating plastic parts. Thanks to its high-precision, repeatability, and cost efficiency at scale, injection molding is used to make a variety of products and parts from the smallest medical insert up to large automotive & aerospace and defense parts. The injection molding process requires an injection molding machine, raw plastic material, and a machined mold. The raw plastic material is first melted in the injection unit and is then injected into the mold — most often machined from steel or aluminum — where it cools and solidifies into the final plastic part. The key steps in the injection molding process are clamping, injection, cooling, and ejection.
How Injection molding Works
The sequence of events during the injection mould of a plastic part is called the injection molding cycle. The key steps in the injection molding cycle are:
Clamping: The two sides of the mold are closed and clamped shut.
Injection: The material is fed into the machine and pushed towards the mold. While this is happening, the material is melted by heat and pressure. The plastic is then injected into the mold — this is called the “shot.”
Cooling: The plastic in the mold cools and solidifies into the shape of the part.
Ejection: After the part cools, it is ejected from the mold.
Features of Injection Molding Service
Advantages
100+ materials
We offer many available injection molding material, also customizable
Accuracy & Efficiency
All sheet metal parts are built on-demand and with lower setup costs compared to CNC Machining. Depending on your needs, order as little as a single prototype up to 10,000 production parts.
Scalability
Molding can be the ideal process for custom production runs of 1-500,000+ parts.
Stable & Durable
Injeciont mold produces real end products that has awesome durability.
Rapid Turnaround
With rapid molding, molds ready in 15 days, parts shipped in 1 to 15 days
Surface Quality
Injection molds are precisely CNC milled and polished, which gives the parts terrific surface, customizable treatments are also available.
Drawbacks
Structure Limits
Interlocking and hollowed structure is difficult to be produces in one pieces with Injection Molding.
Startup Cost
For small batch production, the starting cost is not as affordable as CNC milling or 3D Printing.
Injection Molding Processes
Custom Molded Prototypes and Production Parts with Fast Lead Times
Plastic Injection Molding
Plastic Injection Molding
is a manufacturing process where resin in a barrel is heated to a molten state, then shot into a mold to form a final production-grade thermoplastic part
Liquid Silicone Rubber Molding
Liquid Silicone Rubber Molding
is a thermoset process that mixes a two-component compound together, which is then heat cured in the mold with a platinum catalyst to produce a final part.
Overmolding and insert molding
Overmolding and insert molding
are two-part injection molding processes where one material is overlaid onto a second substrate part or metal insert to create a single component.
Get an Injection Molding quote
Injection Molding Materials
Rigid And Flexible Plastic Varieties,Rubber-Like Varieties
Hard Plastics
ABS | Acrylonitrile Butadiene Styrene
ASA | Acrylonitrile Styrene Acrylate
CA | Cellulose Acetate
COPO | Copolyester
PCT | Polycyclohexylenedimethylene Terephthalate
PPA | Polyphthalamide
HDPE | High-Density Polyethylene
PEEK
Polypropylene (PP)
Polycarbonate (PC)
PMMA | Polymethyl Methacrylate, Acrylic
Nylon 12(PA12)
Nylon 6/66(PA6/66)
Derlin (POM)
Teflon (PTFE)
PBT
PLA | Polylactic Acid
High-Density Polyethylene (HDPE)
PVC
PPS | Polyphenylene Sulfide, Ryton
Vespel (PI)
Torlon 4203 (PAI)
UPE/UHMW
PVDF
ULTEM (PEI)
Flexible Plastics
Polyethylene (PE)
Polystyrene (PS)
PET
EVA Foam
EPS Foam
PU Foam
Rubber-Like Varieties
TPE | Thermoplastic Elastomer, Santoprene
TPU | Thermoplastic Polyurethane (Shore A)
LSR | Liquid Silicone Rubber
LSR | Liquid Silicone Rubber
PVC | Polyvinyl Chloride (Shore A)
POE | Polyolefin Elastomer
MPR | Melt Processable Rubber
EPDM | Ethylene Propylene Diene Monomer Rubber, Viton
Mixed plastic
PC-ABS | Polycarbonate-Acrylonitrile Butadiene Styrene
PC-PBT | Polycarbonate-Polybutylene Terephthalate
PC-PET | Polycarbonate-Polyethylene Terephthalate
PS-PPE | Polystyrene-Polyphenyl Ethers
PE-PS | Polyethylene-Polystyrene
PE-PP | Polyethylene-Polypropylene
PBT-PET | Polybutylene Terephthalate-Polyethylene Terephthalate
PBT-PET | Polybutylene Terephthalate-Polyethylene Terephthalate