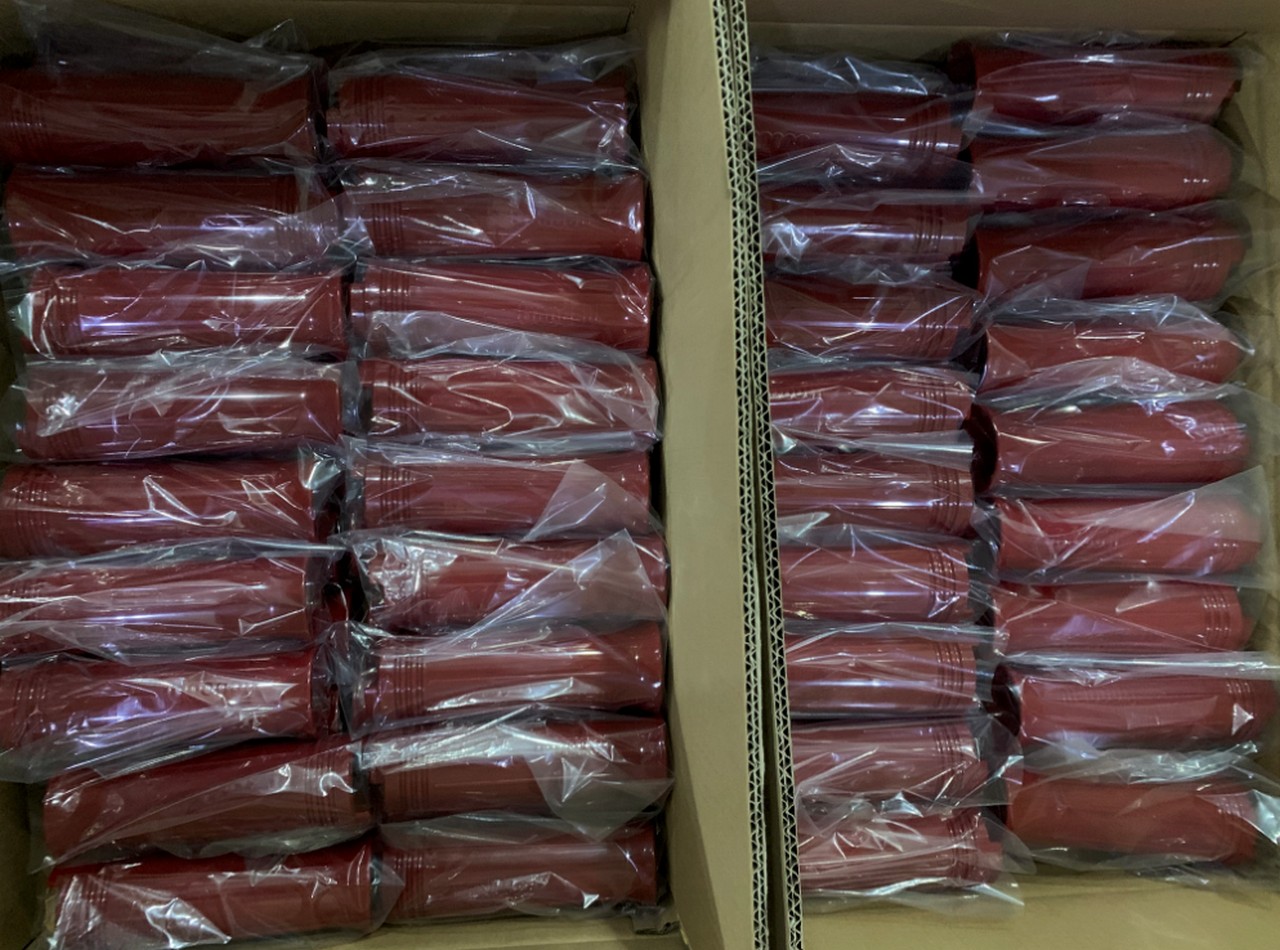
Regarding Injection Molding
Creating plastic parts is a complex job involving many factors that address program requirements. "How will the part be used? " "How does it fit with other areas in the assembly? inch "What loads does it experience in use? " In addition to functional and structural issues, running issues play a huge role in the style of an injection shaped plastic part. Exactly how the molten plastic-type enters, fills, and cools within the cavity to create the part mainly drives what form the features in that part must take. Adhering to some fundamental guidelines of injection shaped part design will bring about an important part that, in addition to being much easier to make and assemble, will typically be much better operating. Separating a part into basic groups will help you build your part in a reasonable manner while reducing molding problems. Since a part is developed, always keep in mind the way the part is shaped and what you can do to reduce stress.
Shot Molding Part
Shot Molding Applications
Plastic-type injection molding is the most preferred process for manufacturing plastic components. Injection molding can be used to generate many things such as digital housings, containers, jar caps, automotive decorations, combs, and a lot other plastic products available today. It is well suited for producing high volumes of plastic-type parts due to the fact that several parts can be manufactured in each cycle by using multi-cavity shot molds. Some highlights of injection molding are high tolerance accuracy, repeatability, large substance selection, low labour cost, minimal discard losses, and little need to end parts after creating. Some disadvantages of this process are an expensive in advance tooling investment and process limitations.
Programs Include:
Packaging
Customer goods
Medical devices
Electronics & telecommunications
Mechanical parts (including gears)
Most other common plastic products currently available
What When You Could:
Decrease mold and tool design times by 75%
Reduce form and tool design times by 74%
Reduce mold creation lead times by 80%
Reduce form production lead times by 80%
Considerably streamline injection form design and creation
Significantly streamline shot mold design and production
Measurably lower production costs with direct metal stamping
Measurably lower creation costs with immediate metal printing
Conquering Injection Molding Style Challenges
Watch the recorded webinar to know how Bastech offers benchmarking results that prove the features of conformal air conditioning with considerable enhancements in cost, efficiency and quality.
Enjoy the Webinar
THREE DIMENSIONAL Techniques
Customer Reports
The basic principles of Shot Creating
Injection Creating Glossary > >
Employer
Refers to the round protrusions on plastic components and molds (#2 in Figure just one below)
Cavity
Appertains to the top half of the injection mold usually the show surface of the completed product but is mainly curvy
Key
Refers to the side of the tool where the plastic part is injected from; also known as the bottom half the tool
Core Outs
Refers to the portion of an important part that is gutted out in order to achieve consistent wall thickness. This particular portion of the business has no conclusion use perform other than fast the part and reducing warp
Set up
Describes portion of injection molding part that has the own taper to make it much easier to remove from the mold. Generally all plastic components should be designed with draft where possible
Door
Refers to where the plastic-type enters into the cavity of the mold. The two types of entrance are the subsequent:
1. Automatically Cut Gates: Gates that incorporate features in the tool in order to or shear the gate as the molding tool is opened to remove the business
2. Manually Trimmed Entrance: Gates that need an operator to split up components from runners during a secondary procedure
Gibbs
Area of the custom shot mold maintain glide down therefore the camera can actuate it
Hand Fill
Light weight aluminum or steel feature in an effect used to create undercuts in shaped parts. They are manually taken off the mold throughout the part ejection process.
High heel
Refers to the percentage of an programmed custom injection form that will bring the slide in the forward position when the creating machine is shut down on the form
Horn Pin
Pin number used to forward the slide with an programmed injection form
Line of Pull
The direction in which the two custom injection form halves will independent from the plastic-type part allowing it to be thrown without the interferences from metal creating undercuts
Ribs
Relates to thin bladed features on the part that are employed for strengthening wall parts and bosses. Likewise, used to reduce warp (#3 in Figure 1 below)
Runner
A station cut into custom injection molds, by which plastic travels from the injection creating machine, through the sprue, through the runner and then through the gateway finally filling the business
Shear
Pertains to when plastic-type material enters to the mould and the burn is maintained by friction manufactured by acceleration and pressure. Also much shear can cause the plastic-type material material to lose, inadequate can cause the fabric to freeze off triggering short picture
Quick Shot
A result of a plastic part not filling completely, including some or all of the details
Shrink Rate
Pertains to how much the plastic stuff will shrink after cooled. This percentage of shrink is added to the part ahead of the mould is designed. Every single plastic material has its own reduce in size rate ranging from. 001 per inches up to. 060 per inch. Despite the fact that most along with between. 004" and. 021"
Side Motion
Term used for slides and/or palm pulls used in the injection mould build process
Drain Marks
Identifies areas of the cast part where it is apparently sunk in, due to un-uniformed wall portions, thick wall portions and rib/boss to thickness ratios being off
Slide
Element of the custom plastic injection conforms that is employed for creating undercuts. Needed for computerized injections conforms
Sprue
Funnel that links the injection molding machine nozzle to the jogger
Steel Risk-free
Appertains to the amount of steel left on the mold in order to tweak in a dimension. Intended for example, if you have an inside diameter that is supposed to be. 500 you may leave the mould at. 505 in case you get excessive shrink
Skinny Wall Molding
Typically the molding of plastic-type material parts with wall structure thicknesses. 005" to. 060" thick
Undercuts
Appertains to the portion of the designed component where a slide or hand pull is required to create holes, windows or clips that are not in the queue of bring (#1 in Number 1 below)
Vestige
Material protruding from the gate area after gate jogger has been removed from the injections molded part. This specific vestige is usually trimmed by the molding machine user
Wall Fullness
Pertains to how heavy the cross part of the plastic part is
Warp
Pertains to portion of a injection molded part that distorts during cooling or creating, triggering undesired results in the done product. Usually brought on by un-uniform wall structure sections
?
Polymers Perfect for Injection Developing
Injection Molding Tools
Injection Molding Method
Injection Molding Pattern
Different Types of Injection Molding Operations
Stress
Entrances
Popular Gates
Gate Spot
Wall Fullness
Drain Marks
Smoothness
Separating Lines
Common Creating Defects
Polymers Ideal Suited for Injections Molding
There are thousands of different materials designed for injection creating. Most polymers may be used, including all thermoplastics (such as nylon, polyethylene, and polystyrene) and a few elastomers. Materials are chosen based on the strength and function required for a final part, but each material also has different variables for molding that must be considered. Mixing the available materials with metals or blends of previously developed materials permits product creative designers to choose from a huge selection of materials to obtain the one with specifically the right properties.
Injection Molding Tools
Injection Molding Equipment:
Injection molding machines, often known as presses, are made up of a stuff hopper, a picture ram or screw-type plunger, and a heating unit. Conforms are clamped to the platen of the molding machine, where plastic is injected into the mold through the sprue orifice. Pushes are rated by tonnage, which is the calculation of the amount of clamping force that the appliance can put in. This force will keep the mold sealed through the injection creating process. Tonnage can vary from less than 5 loads to 6, 1000 tons, although higher tonnage presses are rarely used. Typically the total clamp power needed is established by the expected area of the custom part being molded. This expected area is increased by way of a clamp power of two to 8 tons for each and every square inch of the projected areas. As a concept of thumb, 4 or 5 tons/inch can be used for most products. If the plastic-type material material is very stiff, it will need more injection pressure to fill the mould, thus more grip tonnage is necessary to maintain the mold sealed. The required power can even be determined by the material used and the size of the business, with larger plastic-type material parts requiring higher clamping force.
Mould:
The mold or die refers to the tooling used to produce plastic-type material parts in creating. Traditionally injection conforms have been expensive to manufacture and were only found in high-volume production apps where thousands of parts were produced. Molds are typically constructed from hard steel, pre-hardened metallic, aluminum, and/or beryllium-copper alloy. Selecting a material for mould building is generally something of economics. Steel molds generally will cost more to build but give a more time lifespan that will offset the bigger primary cost over the higher number of elements made before showing signs of damage. Pre-hardened steel conforms are less wear-resistant and are generally used for lower volume requirements or larger components. Typically the hardness of the pre-hardened steel procedures typically 38 and 45 on the Rockwell-C scale. Hard steel molds are heat treated after machining, making them superior in words of wear weight and lifespan. Normal hardness ranges between 50 and 70 Rockwell-C (HRC).
Lightweight aluminum m