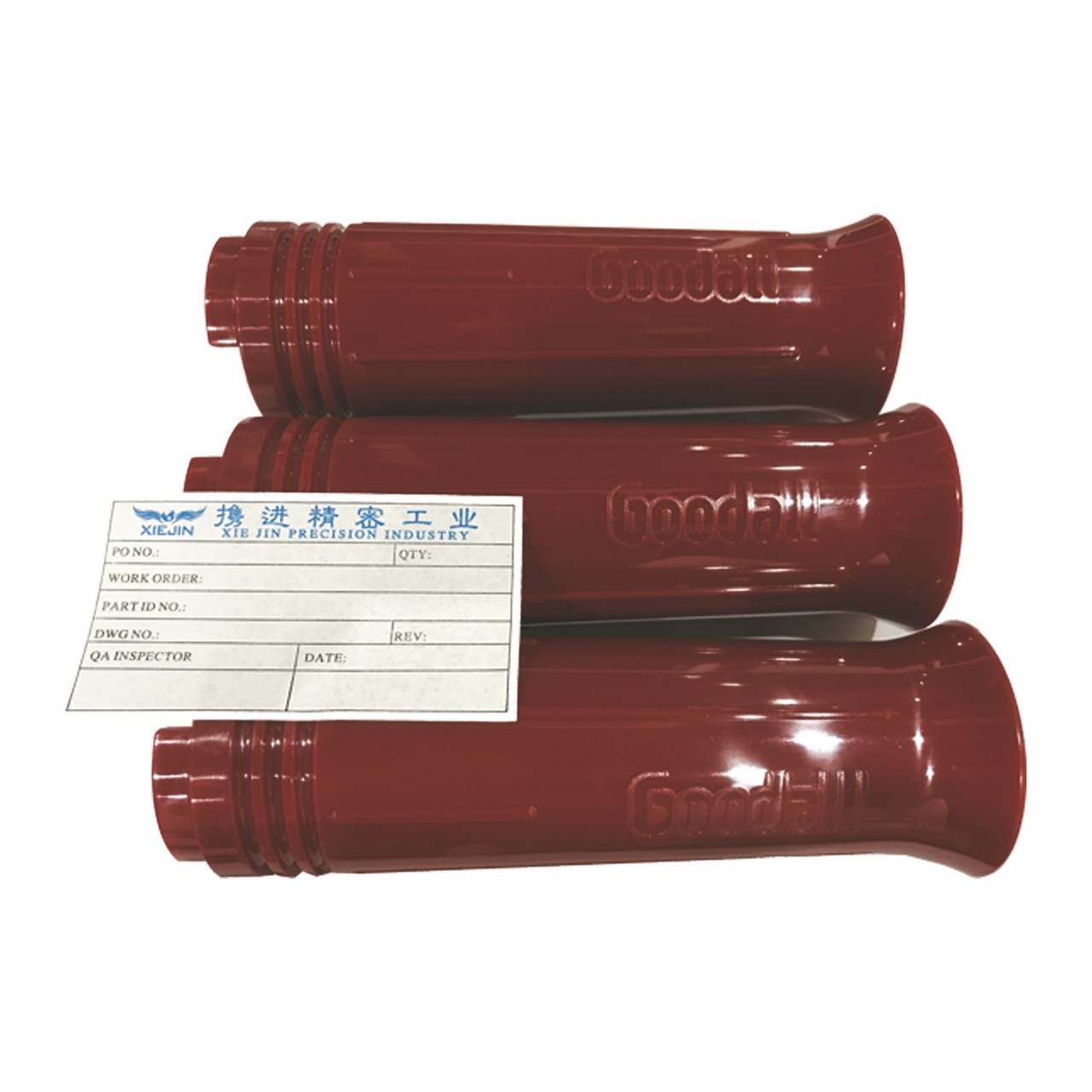
VThe basics
What is a injection creating? How does it work and what could it be used for?
With this section, we answer these questions and possess you common samples of injection shaped parts to help you familiarize yourself with the basic mechanics and programs of the technology.
What is shot molding?
Injection creating is a production technology for the mass-production of similar plastic parts with good tolerances. Within Injection Molding, plastic granules are first melted and then injected under pressure into a mildew, where the water plastic cools and solidifies. The materials used in Shot Molding are thermosoftening plastic polymers that can be colored or filled with other additives.
Almost every plastic part around you was produced using injection creating: from car components, to electronic enclosures, and also to kitchen home appliances.
Injection molding is so popular, due to the significantly low cost per unit when manufacturing high quantities. Injection molding offers high repeatability and good design versatility. The primary restrictions on Injection Molding usually come right down to economics, as high preliminary investment for the mold is needed. Furthermore, the turn-around time from design to production is sluggish (at least 4 weeks).
The shot molding process
I AM 101 - Shot molding process
Shot molding is broadly used today for both consumer companies engineering applications. Nearly every plastic item who are around you was produced using injection molding. For the reason that the technology will produce identical pieces at very high volumes (typically, a single, 000 to hundred, 000+ units) at a very inexpensive per part (typically, at $1-5 for each unit).
But in comparison to other technologies, the start-up costs of injection molding are relatively high, due to the fact custom tooling is required. A mold can cost between $3, 000 and hundred buck, 000+, depending on its complexity, materials (aluminum or steel) and accuracy (prototype, pilot-run or full-scale production mold).
Almost all thermoplastic materials can be injection shaped. Some types of silicone and other thermoset resins are also suitable for the injection molding process. The most popular materials in shot molding are:
Thermoplastic-polymer (PP): ~38% of worldwide production
ABDOMINAL MUSCLES: ~27% of global production
Polyethylene (PE): ~15% of worldwide production
Polystyrene (PS): ~8% of global manufacturing
Even if we take into consideration all other possible manufacturing technologies, shot molding with these four materials by yourself accounts for more than 40% of most plastic parts produced globally every 12 months!
The of Shot creating
Plastics replace off white
Within 1869, John Wesley Hyatt invented celluloid, the first useful artificial plastic meant to replace ivory for the production of... billiard balls! Earlier injection molding machines used a barrel or clip to warm up the plastic and a plunger to put in it to the mold.
A innovative creation
In the mid 1950s, the invention of the reciprocating screw by themselves revolutionized the materials industry. The reciprocating screw solved key issues with wrinkled heating of the plastic that past systems faced, and opened up new horizons for the mass production of plastic parts.
Treatment molding today
Right now, injection molding is a $300 billion dollars market. 5+ thousand metric tons of plastic parts are produced with treatment molding globally each year. Recently, the demand of environmentally friendly materials is increasing for environmental reasons.
Injection molding machines: how do they work?
An treatment molding machine involves 3 main pieces: the injection product, the mold - the heart of the whole process - and the clamping/ejector unit.
Throughout this section, we examine the goal of each of these systems and just how their basic functioning mechanics have an effect on the end-result of the Injection creating process.
Watch a sizable injection molding machine in action while producing 72 bottle of wine caps every 3 seconds in it here:
The treatment unit
IM101 - Injection molding schematic
The purpose of the injection product is to burn the raw plastic-type material and guide it into the mould. It involves the hopper, the clip or barrel, and the reciprocating screw.
Here is how the treatment molding process works:
The polymer lentigo are first dried up and located in the hopper, where they are merged with the colouring pigment or the other reinforcing chemicals.
The granules are fed in to the barrel or clip, where these are at the same time heated, mixed and moved for the form by a varying pitch screw. The particular geometry of the screw and the barrel are enhanced to help build-up the pressure to the right levels and melt the substance.
The ram then moves forwards and the melted plastic-type is injected into the mold through the runner system, where it floods the whole hole. Because the material lowers down, it re-solidifies and takes the form of the mold.
Finally, the mold opens and the now reliable part is pressed out by the ejector pins. The particular mold then shuts and the procedure repeats.
The whole process can be recurring very fast: the cycle takes around 30 to ninety days seconds based on the size of the business.
After the part is ejected, it is dispensed on a conveyor seatbelt or in a holding container. Generally, injection molded components decide to use instantly and require little to no post-processing.
Manufacturing the shape
The mold is a lot like the negative of an photograph: its angles and surface surface is directly shifted onto the treatment molded part.
That usually makes way up the most significant part of the start up costs in injections molding: the expense of a typical mold begins at approximately $2, 000-5, 000 for a simple angles and relatively small production runs (1, 000 to 12, 000 units) and go upwards to $100, 000 for molds optimized for full-scale production (100, 000 units or more).
This is due to the high level associated with required to design and manufacture a high-quality mold that can produce precisely thousands (or lots of thousands) of parts.
Molds are usually Cnc-machined out there of aluminum or tool steel and then finished to the required standard. Apart from the negative of the part, they also have other features, like the athlete system that helps the flow of the material into the mold, and internal water soothing channels that support and quicken the cooling of the part.
Learn more about CNC engineering in the making and design guide →
Recent innovations in 3D making materials have empowered the manufacturing of molds well suited for low-run injection molding (100 parts or less) at a small percentage of the cost. Such small amounts were economically unviable in past times, due to the very high cost of traditional mold making.
The business mold design for producing a hundreds and hundreds of parts quantity of plastic components
An commercial mildew design for creating a tens of countless numbers of parts quantity of plastic parts. The particular cavity is show on the remaining and the primary on the right.
The anatomy of the mildew
I AM 101 - Schematic of a mildew for Injection creating
The simplest mildew is the straight-pull mold. It comprise of 2 halves: the cavity (the front side) and the core (the back side).
Inside most cases, straight-pull molds are preferred, because they are simple to design and manufacture, to get total cost relatively low. Generally there are some design restrictions though: the business must have a 2 . not G geometry to each area and no overhangs (i. e. areas that are not supported from below).
If more advanced geometries are required, then retractable side-action induration or other inserts are required.
Side-action cores are moving elements that enter into the mold from the top or perhaps the bottom and are employed to manufacture elements with overhangs (for example, a tooth cavity or a hole). Side-actions should be applied sparingly though, since the cost increases quickly.
Interesting fact: Regarding 50% of the normal injection molding period is dedicated to cooling and renforcement. Minimizing the width of the design is key to velocity up this step and cuts costs.
The two edges of the mildew: A side & B part
Shot molded parts have two sides: the A side, which faces the hole (front half the mold) and the B side, which faces the primary (back half of the mold). These types of two sides usually serve different purposes:
The A part usually has better visual appearance and it is often called the cosmetic side. The particular faces on the A side will be smooth or will have a textured according to your design specs.
The B part usually provides the hidden (but very important) structural aspects of the part (the bosses, ribs, snap-fits and thus on). Intended for this reason it is called the functional side. Typically the B side will often have a rougher finish and obvious marks from the ejector buy-ins.
Injecting material to the mold: The jogger system
The jogger system is the channel that guidelines the melted plastic-type material to the cavity of the mold. That controls the circulation and pressure with which the water plastic is shot into the hole and it is removed after disposition (it snaps off). The runner system usually includes 3 main sections:
The particular sprue is the primary channel by which all the melted plastic material primarily flows through as it goes in the mold.
Typically the runner spreads the melted plastic alongside the face where two halves of the mold meet and connects the spur to the gates. There may be more than one sportsmen, guiding the textile towards one or multiple parts. Typically the runner system is cut off from the part after ejection. This is the only stuff waste in treatment molding, 15-30% of that can be recycled and reused.
The gateway (is the gain access to point of the material in the tooth cavity of the mould. Its geometry and location is important, as it can determine the flow of the plastic.
Distinct gates types are well suited for different software. You will discover 4 types of gates used in injection creating:
Edge gates utilize material at the parting distinctive line of the two halves of the mold and are the most typical door type. The athlete system needs to be removed manually later, departing a little imperfection at the injection point.
Canal gates inject substance below the separating line. The athlete system snaps off because the part is ejected from the mold, eliminating the need for guide removal. This makes this sort of door well suited for very large volumes.
Post entrance inject the cloth from the rear of the hole, hiding the small imperfection left from smashing the other door types. These entrance are employed for elements that need excellent aesthetic appearance.
Hot tips are directly linked to the encourage and inject plastic-type from the top side of the part. No substance is wasted this way on the runner system which makes them well suited for large size production, but a dimple will be noticeable at the injection point.
The particular vestige
At the point the location where the athlete system linked with the part, a little imperfection is usually visible, called the vestige.
If the existence of the vestige is not desirable for cosmetic purposes, then in can be "hidden" in the functional B-side of the business.
The clamping and ejection system
Within the far side of your injection molding machine is the clamping system. The clamping system has a dual purpose: it keeps the 2 parts of the mold tightly close during injection and it also pushes the part from the mold after it opens.
Right after the part is ejected, it comes onto a conveyor belt or a bucket for safe-keeping and the routine starts once again.
Position of the several moving parts of the mold is never perfect though. This specific causes the design of two common imperfections that are noticeable on almost every injection shaped part:
Parting outlines which are noticeable quietly of a part the location where the 2 halves of the mold meet. They will are caused by tiny misalignments and the slightly curved edges of the mold.
- Ejector (or witness) signifies which can be noticeable on the hidden B-side of the part. They are created because the ejector pins are a bit protruding above or indented below the surface of the mold.
The image below shows the mold used to manufacture both both equally sides of the casing for a remote controller. Fast quiz: attempt to identify the core (A-side), the cavity (B-side), the runner system, the ejector buy-ins, the side-action key and air ports on this form.
IM 101 - Example mold with noticeable parting range, ejector pins, athlete system, cavity, key and side-action key
Benefits and constraints of injection creating
Injection molding is definitely an established manufacturing technology with a long history, but is actually constantly being sophisticated and improved with new technological breakthroughs.
Below is an easy rundown of the main element advantages and down sides of injection creating to help you understand whether is actually the right solution for your program.
Benefits of injections molding
High-volume producing of plastics
Broad variety of materials
Very high output
Great repeatability and tolerances
Superb visual appearance
Constraints of injection creating
High start-up costs for tooling
Style changes are costly
Longer lead times than any other technologies
Examples of products made with injection creating
When you look around you right now, you will see at least a few products that have been made with injections molding. You're probably looking at one right now actually: the casing of the product you are using to learn this guide.
To understand them, look out there for these 3 things: a separating line, witness signifies on the concealed side and a comparatively uniform wall density throughout the part.
We've collected some examples of goods commonly manufacturing with injection molding to help get an improved understanding of what can be executed with this producing process.
Toys
Presentation
Miniatures
Automotive
Power
Healthcare
Lego rocks
Lego bricks are among the most recognizable types of injections molded parts. Could possibly be made using conforms, like the one in the picture, which produced a hundred and twenty million lego stones (that's 15 , 000, 000 cycles) before it was removed from commission.
The substance used for Seglar bricks is AB MUSCLES due to the high impact resistance and excellent moldabillity. Each packet has been designed to perfection, reaching tolerances down to 10 micro metres (or a 10th of any human hair).
This is certainly partly achieved by using the best design procedures, which we'll look at in the next section (uniform walls thickness, draft perspectives, ribs, embossed textual content and so on ).
A upon the market Lego brick mildew
Part 2
The particular design of shot molding
There are many factors that may impact the quality of the last product and the repeatability of the procedure. To produce the entire advantages of the process, founder must follow certain design guidelines.
In this section, we summarize common defects of injection molding and basic and sophisticated guidelines to follow when designing components, including suggestions to help keep the costs to a minimum.
Typical injection molding problems
Most defects in injection molding are related to either the flow of the melted materials or its non-uniform cooling rate during solidification.
Here is a listing of problems to keep in mind while developing a part for injection molding. Within the next section, we'll notice how you can avoid each of them by subsequent good design methods.
Bending
When certain sections cool (and consequently shrink) faster than others, then the part can permanently bend because of to internal tensions.
Parts with non-constant wall thickness are most vulnerable to bending.
Sink scars
Whenever the interior of the part solidifies before its surface, a little recess in an otherwise flat surface may appear, known as sink tag.
Parts with solid walls or badly designed ribs are most prone to sinking.
Drag scars
As the plastic material shrinks, it is applicable pressure on the mold. During disposition, the walls of the business will slide and clean against the mildew, which can outcome to drag scars.
Parts with straight walls (and no draft angle) are most prone to drag marks.
Made lines
When 2 flows meet, small hair-like discolorations may develop. These made lines impact the parts aesthetics, but additionally they generally reduce the strength of the part.
Components with abrupt angles changes or openings are more susceptible to knit ranges.
Short photos
Caught air in the mold can prevent the flow of the material during injection, resulting in an incomplete part. Good design can enhance the flowability of the melted plastic material.
Parts with very thin walls or poorly designed steak tend to be more prone to short shots.
Working with undercuts
The easiest mold (the straight-pull mold) consist of 2 halves. Functions with undercuts (such since the teeth of a thread or the hook of the snap-fit joint) might not be manufacturable with a straight-pull mildew though. This is either because the mold cannot be CNC machined or because the materials with the way of ejecting the part.
Undercuts in injection molding are part features that cannot be produced with a simple two-part mold, because material with the way while the mold opens or during ejection.
The particular teeth of the line or the connect of a snap-fit joint are good examples of undercuts.
Right here some ideas to help you offer with undercuts:
Prevent undercuts using shutoffs
Avoiding undercuts completely might be the smartest choice. Undercuts always add cost, difficulty, repairs and maintanance requirements to the mold. A smart redesign can often eliminate undercuts.
Shut-offs are a good technique to deal with undercuts on inner parts of the part (for snap-fits) or on the perimetres of the part (for holes or handles).
Below are some examples displaying how injection shaped parts can be redesigned to avoid undercuts: essentially, materials is removed in the area under the undercut, removing the issue completely.
Samples of design modification that will help you eliminate undercuts Examples of design alteration that can help you eliminate undercuts
Proceed the parting collection
The best way to offer with an undercut is to move the parting collection of the mildew to intersect from it.
This solution is ideal for many designs with undercuts on an external surface. Don't forget to change the write angles accordingly.
Make use of a stripping undercut (bumpoffs)
Stripping undercuts (also known as bumpoffs) can be used when the feature is versatile enough to deform over the mildew during ejection. Burning undercuts are utilized to manufacture the strings in bottlecaps.
Undercuts can simply be used under these conditions:
- The burning undercut must be located far from stiffening features, such as corners and steak.
- The undercut must have a lead angle of 30o to 45o degrees.
- The particular injection molded part must have area and must be flexible enough to expand and deform.
It is suggested to avoid stripping undercuts in parts produced from dietary fiber reinforced plastics. Usually, flexible plastics such as PP, HDPE or Nylon (PA) can tolerate undercuts of up to 5% of their diameter.
Samples of design alteration that will help you eliminate undercuts
Instance part with burning undercuts. The part is deformed as it is forced out of the mold.
Sliding side-actions and callosité
Slipping side-actions and callosité are utilized launched not possible to upgrade the injection shaped part to avoid undercuts.
Side-action callosité are inserts that slide in since the mold closes and slide out before it opens. Remember that these mechanisms add cost and difficulty to the mildew.
Follow these recommendations when designing a side actions:
- There needs to be space for the core to move in and out. Which means that the feature must be on the other side of the part.
- The particular side-actions must move perpendicularly. Moving into the angle other than 90° much more complicated, increasing cost and lead times.
- Don't neglect to add write angles to your design as always, taking in concern the movement of the medial part action core.
Popular design features
Discover ways to design the most typical features encountered in injection molded pieces with these sensible guidelines. Use them to improve the operation of your designs, while still making sure that you comply with the standard design rules.
Threaded nails (bosses and inserts)
There are 3 ways to add fasteners to an injection molded part: by designing a thread upon the part, by adding a boss where the screw can be attached, or by together with a threaded put.
Modelling a carefully thread upon the part is possible, but is not recommended, as the teeth of the thread are fundamentally undercuts, increasing substantially the complexity and expense of the mould (we will more about undercuts in a later section). An example of a shot cast part with a thread are bottle of wine caps.
Bosses
Companies are incredibly common in Injection Cast parts and are widely-used as points for attachment or assemblage. They consist of cylindrical projections with holes created to acquire screws, inserts with threads, or other types of attachment and assembly hardware. A good way to think of your boss is as a rib that closes on itself in a round.
Bosses are widely-used as parts of accessory or fastening (in conjuction with self-tapping screws or threaded inserts).
Recommended design of a supervisor
When bosses are widely-used as points of fastening, the exterior diameter of the boss should be 2x the moderate diameter of the screw or put and its interior diameter equal to the diameter of the core of the screw. Typically the hole of the boss should prolong to the base-wall level, set way up full depth is not needed for assembly, to maintain a uniform wall membrane thickness throughout the feature. Include a chamfer for easy insert of the attach or insert.
Intended for optimum results:
Steer clear of designing bosses that merge into main wall surfaces
Support companies with ribs or attach them to a main wall membrane
For bosses with inserts, use an outer diameter similar to 2× the insert's nominal size
Threads
Metal threaded inserts can be added to plastic-type material Injection Molded pieces to realise a durable threaded hole for nails such as machine screws. The good thing about using inserts is that they allow many cycles of assemblage and disassembly.
Inserts are installed in Injection Molded pieces through thermal, ultrasonic or in-mold insert. To create a supervisor that will acquire a threaded put, use similar rules as above, using the diameter of the insert as the guiding aspect.
A threaded put located in a boss
For best results:
Avoid adding threads directly on your injection cast part
Design companies with an exterior diameter equal two times the nominal size of the attach or put
Put a 0. 6 mm relief at the edges of the thread
Make use of a thread with a pitch greater than 0. 8 millimeter (32 threads for each inch)
Use a a trapezoidal or buttress line
Greatest way to offer with the created undercuts:
Make use of a line with a message greater than zero. 8 mm (32 threads per inch)
For external strings, place them together the parting collection
Ribs
When even the maximum suggested wall thickness is not enough to satisfy the functional requirements of the part, steak may be used to improve the stiffness.
When developing ribs:
● Make use of a thickness corresponding to 0. 5 × main wall width
● Define a height smaller than 3 × ribs width
● Make use of a base fillet with radius higher then? × ribs thickness
● Include a draft position of at minimum 0. 25° - 0. 5°
● Add a min. distance between steak and walls of 4 × ribs width
Snap-fit important joints
Snap-fit joints are a simple, economical and rapid way of joining two components without fasteners or tools. A broad range of design possibilities exists for snap-fit joints.
Because a rule of thumb, the deviation of a snap-fit joint mainly will depend on its length and the permissible pressure which can be applied on it on the width (since the thickness much more or less defined by the wall width of the part). Also, snap-fit important joints are another example of undercuts.
Type of an set up with snap-fit important joints
Within the example above, the most regular snap-fit joint design (known since the cantilever snap-fit joint) is shown. Just like steak, add a write angle to your snap-fit joints and use a minimal thickness of zero. 5x the walls thickness.
Specific recommendations on designing snap-fit joints is a huge subject that will go beyond the range of this article. To get more detailed information, please refer to this article from MIT.
For best results:
Add a draft angle to the vertical wall space of your snap-fit joints
Design snap-fits with thickness higher than 0. 5x the wall width
Adjust their size and length to manage their deflection and permissible force
Residing hinges
Living handles are thin components of plastic that connect 2 sections of the part and allow it to flex and flex. Typically these handles are incorporated in mass-produced containers, such as plastic storage containers. A well-designed residing hinge can final for approximately a mil cycles without failing.
The material used to injection mildew a living joint must be versatile. Polypropylene (PP) and Polyethylene (PE) are good options for consumer application and Synthetic (PA) for architectural uses.
A practical hinge is shown below. The suggested minimum thickness of the hinge varies between 0. 20 and 0. thirty-five mm, with higher thicknesses leading to more durable, but firmer, parts.
Example of an living joint (left) and suggested design dimensions for PP or RAPID EJACULATIONATURE CLIMAX, (right)
Before heading to full-scale manufacturing, prototype your residing hinges using COMPUTER NUMERICAL CONTROL machining or THREE DIMENSIONAL printing to look for the angles and stiffness that best fits the application. Add nice fillets and design shoulders with a uniform wall width since the key body of the business to increase the material flow in the mold and minimize the tensions. Divide hinges lengthier than 150 millimeter in two (or more) to improve lifetime.
For comprehensive guidelines, please recommend to this DURCH guide.
For best results:
Design handles with a width between 0. 20 and 0. thirty-five millimeter
Select a flexible material (PP, PE or PA) for parts with living handles
Make use of shoulders with a thickness equal the thickness of the key wall
Include fillets as large as possible
Smash steak
Crush Steak are small sticking out features that deform to produce friction when different components are pushed together, acquiring their possition.
Smash ribs can be an economical option for manufacturing high tolerance holes for tight fits. They may be commonly used to house bearings or shafts and other press fit programs.
An example of a component with smash ribs is shown below. Using 3 crush ribs is recommended to ensure good alignment. The particular recommended height/radius for every single rib is 2 mm. Put in a minimal interference of zero. 25 mm between the crush ribs and the installed part. Because of the small surface contact with the mold, crush steak can be designed without a write angle.
Example of an crush ribs (left) and suggested design dimensions (right)
For best results:
Add a minimal interference of zero. 25 mm between crush rib and the component
Perform not put in a write angle on the vertical walls of a crush steak
Lettering and icons
Text is a very common feature that can be helpful for logos, labeling, warnings, diagrams and instructions, saving the expense of stick on or painted labeling.
When adding textual content, choose embossed textual content over engraved textual content, as it's much easier to CNC machine on the mold and so more affordable.
Also raising the text 0. 5 mm over a part surface will make sure that the letters are easy to read. We recommend selecting a bold, curved font style with uniform line width, with a size of 20 factors or larger. A few font examples include: Century Gothic Strong, Arial and Verdana.
For optimum results:
Use embossed textual content (0. 5 millimeter height) instead of imprinted texted
Make use of a typeface with uniform width and at least typeface size of 20 points
Align the written text verticle with respect to the separating line
Make use of a elevation (or depth) higher than 0. 5 mm
Tolerances
Shot molding typically produces parts with tolerances of ± zero. 250 mm (0. 010").
Tighter tolerances are feasible in some circumstances (down to ± 0. a hundred and twenty-five mm - and even ± zero. 025 mm), nevertheless they raise the cost significantly.
For small manufacturing runs ( < 10, 000 units), consider by using a secondary working (such as drilling) to improve precision. This ensures the right interference of the business with other components or inserts (for example, when using press fits).
Design rules for injection molding
One of the greatest great things about injection creating is how easily complex geometries can be formed, allowing a single part to serve multiple functions.
Once the mold is produced, these complex components can be produced at an extremely low cost. But becomes the mold design at later phases of development can be quite expensive, so reaching the best results on the first time is important. Adhere to the guidelines below to avoid the most popular defects in injection molding.
Make use of a regular walls thickness
Make use of a standard wall thickness all through the part (if possible) and avoid thick sections. This particular is significant as non-uniform walls can result in warping or the part as the melted material lowers down.
If areas of different width are required, make the transition as smooth as you possibly can by using a chamfer or fillet. This particular way the material will flow more evenly inside the cavity, ensuring that the entire mold will be fully packed.
Associated with transition as smooth as possible at portion of non-uniform wall width
Create the transition as smooth as possible at section of non-uniform wall width
A wall width between one 2 mm and 3 mm is a safe value for many materials. The next table summarises specific recommended wall thicknesses for a few of the most frequent shot molding materials:
Material Recommended wall thickness [mm]Recommended wall membrane thickness [inches]
Polypropylene (PP) 0. 6 - 3. 6 mm 0. 03'' - 0. 15''
ABS 1. 2 - 3. 5 mm 0. 045'' - 0. 14''
Polyethylene (PE) 0. 6 - 3. zero mm 0. 03'' - 0. 12''
Polystyrene (PS) 1. 0 - 4. 0 mm 0. 04'' - zero. 155''
Polyurethane (PUR) 2. 0 - 20. 0 mm 0. 08'' - 0. 785''
Nylon (PA 6) 0. 8 - 3. 0 mm 0. 03'' - 0. 12''
Polycarbonate (PC) 1. zero - 4. zero mm 0. 04'' - 0. 16''
PC/ABS 1. 2 - 3. 5 mm 0. 045'' - 0. 14''
POM (Delrin) 0. 6 - 3. zero mm 0. 03'' - 0. 12''
PEEK 1. 0 - 3. 0 mm 0. 04'' - 0. 12''
Silicone 1. 0 - 10. 0 mm 0. 04'' - zero. 40''
For best results:
Use a uniform wall fullness within the advised values
When different thickness will be required, smoothen the move by using a chamfer or fillet with length that is 3x the difference in fullness
Hollow out heavy portions
Thick portions can cause various disorders, including warping and sinking. Limiting the maximum thickness of any area of your design to the recommended values by making them empty is essential.
To be able to increase the strength of hollow section, use ribs to design structures of similar strength and rigidity but reduced wall membrane thickness. A stylish part with empty sections is shown below:
Hollow heavy sections and add ribs to improve stiffness
Ribs can even be used to increase the stiffness of lateral sections without increasing their thickness. Bear in mind though that the wall thickness limits still apply. Exceeding beyond the recommended ribs thickness (see below) can cause drain marks.
The wall membrane thickness limitations still apply for steak
For optimum results:
Hollow out heavy sections and use ribs to increase the strength and rigidity of the business
Design ribs with max. thickness comparable to 0. 5x the wall thickness
Design and style ribs with utmost. height equal to 3x the wall membrane fullness
Add soft changes
Recommended: 3 × wall fullness big difference
Sometimes portions based on a wall thicknesses may not be avoided. Throughout these cases, use a chamfer or fillet to make the transition as smooth as is possible.
In the same way, the base of vertical features (such ribs, bosses, snap-fits) must also always be rounded.
Rounded all corners
Typically the uniform wall fullness limitation also does apply to edges and corners: the move must be as smooth as possible to ensure good material flow.
Intended for interior edges, use a radius of at least zero. 5 x the wall thickness. Intended for exterior edges, add a radius similar to the indoor radius plus the wall thickness. This kind of way you ensure that the fullness of the wall surfaces is frequent all over the place (even at the corners).
Adding to this, sharp 4 corners cause stress levels which can cause weaker parts.
Put wide radii to all edges to take care of uniform wall fullness and avoid disorders
Add wide radii to all or any edges to maintain uniform wall membrane thickness and steer clear of disorders
For best results:
Add a fillet comparable to 0. 5x the wall fullness to internal 4 corners
Include a fillet similar to 1 ) 5x the wall fullness to external 4 corners
Add draft aspects
To make the ejection of the part from the mold easier, a draft angle must be added to all vertical wall surfaces. Walls with out a pen angle will have drag marks on their surface, as a result of high friction with the mold during ejection.
A bare minimum draft angle of 2° is advised. Larger draft aspects (up to 5o °) should be used on a more elevated features.
Learn more about the value of draft angles in this article →
A fantastic rule of thumb is to improve the draft perspective by one education for each and every 25 logistik. For example, add a draft perspective of 3o deg to an credit that is seventy five mm tall. Much larger draft angle should be used if the business has a textured surface finish. Generally speaking of thumb, add 1o to 2o extra degrees to the results of the aforementioned calculations.
Remember that draft angles are also necessary for ribs. Remember though that adding an angle will reduce the thickness of the top of the rib, so make certain that your design complies with the recommended minimum wall membrane thickness.
Add a draft angle (minimum 2o)to all top to bottom walls
Include a pen angle (minimum 2o)to all vertical wall surfaces
For best results:
Add a bare minimum draft angle of 2o degrees to all vertical wall surfaces
For features a more elevated than 50 logistik, improve the draft perspective by one education every 25 logistik
For parts with textured surface surface finish, improve the the pen angle by 1-2o extra deg
Element 3
Injection creating materials
Injection creating is compatible with a variety of plastics. In this particular section, you'll find out about the key characteristics of the extremely popular materials. We'll also discuss the normal surface completes that could be applied to injection molded pieces.
Materials used for injection creating
Most thermoplastics can be injection molded. Many thermosets and the liquid silicones are also compatible with the injection molding process.
They can be also reinforced with fibers, rubber debris, minerals or fire retardant agents to change their physical properties. For example fiberglass can be mixed with the pellets at percentages of 10%, 15% or 30% causing parts with higher stiffness.
Polypropylene (PP)
The most common Injection molding plastic-type material. Excellent chemical weight. Food-safe grades available. Not well suited for physical applications.
STOMACH MUSCLES
Popular thermoplastic with good impact resistance, cheap & low thickness. Vulnerable to solvents.
Polyethylene (PE)
Light and portable thermoplastic with good impact strength & weather resistance. Suited for outdoor software.
Polystyrene (PS)
Typically the Injection molding plastic-type material with the minimum cost. Food-safe grades available. Not well suited for physical applications.
Polyurethane (PU)
Thermoplastic with good impact strength and good mechanical properties & hardness. Well suited for molding parts with thick walls.
Synthetic (PA 6)
Anatomist thermoplastic with excellent mechanical properties and high chemical & abrasion resistance. At risk of moisture.
Polycarbonate (PC)
The plastic with the very best impact durability. High thermal weight, weather resistance & toughness. Can be colored or translucent.
PC/ABS
Mixture of two thermoplastics causing high impact durability, excellent thermal steadiness, and high rigidity. Prone to solvents.
POM (Acetal/Delrin)
Engineering thermosoftening plastic with good durability, stiffness & wetness resistance and self-lubricating properties. Relatively likely to warping.
GLANCE
High-performance engineering thermosoftening plastic with excellent durability and thermal & chemical resistance. Accustomed to replace metal pieces.
Silicone rubber
Thermoset with excellent high temperature & chemical weight and customizable banks hardness. Food-safe and medical grade available.
An additive that is commonly used to increase the rigidity of the treatment molded parts is fiberglass. The goblet fibers can be combined with the pellets at percentages of 10%, 15% or 30%, causing in several mechanical properties.
Colorant can be added to the mixture (at a ratio of about 3%) to create a great variety of colored pieces. Standard colors include red, green, discolored, blue, black and white and so they can be mixed to create different colours.
Surface finishes and SPI standards
Area finishes can be used to give an injection cast part a certain look or feel. Besides cosmetic purposes surface finishes can also serve technological needs. For example, the average surface roughness (Ra) can drastically influence the lifetime of moving parts such as plain bearings.
Treatment molded parts are not usually post-processed, but the mould itself can be finished to various degrees.
Keep in mind that hard surfaces improve the scrubbing between your part and the mold during ejection, therefore a larger draft perspective is required.
Typically the Society of Materials Industry (SPI) points out several standard polishing off procedures that end result in several part surface finishes.
Finish Description SPI standards* Applications
Glossy finish The mould is first smoothed and then finished with a precious stone buff, resulting in a mirror-like surface finish. A-1
A-2
A-3 Suitable for parts that want the smoothest surface finish for plastic or functional purposes (Ra less than 0. 10 μm). The A-1 surface finish is well suited for pieces with mirror-like surface finish and lenses.
Semi-gloss finish The mold is smoothed with fine grit sandpaper, causing in a fine surface finish. B-1
B-2
B-3 Suitable for parts that require a good image appearance, but not a high smooth look.
Matte finish The mold is smoothed using fine natural stone powder, removing all machining marks. C-1
C-2
C-3 Suitable for parts with low visual appearance requirements, but machining represents are not satisfactory.
Textured finish The mould will be smoothed with fine natural stone powder and then sandblasted, creating a bumpy surface. D-1
D-2
D-3 Suitable for pieces that require a satin or lifeless textured surface surface finish.
As-machined finish The mould is finished to the machinist's acumen. Tool marks will be visible. - Suitable for non-cosmetic pieces, such professional or hidden components.
If deciding on a glossy surface finish, remember these useful tips:
Some sort of high glossy mould finish is not equivalent to an increased glossy finished product. It is significantly be subject to other factors such as plastic-type material resin used, creating condition and mould design. For illustration, ABS will produce parts with a better glossy surface surface finish than PP. To obtain the recommended material and surface finish combo visit the appendix.
Finer surface completes demand a higher class material for the mold. To achieve a very fine polish, tool terme conseillé with the top hardness will be required. This kind of has an impact on the overall cost (material cost, machining as well as post-processing time).
Part 4
Cost reduction tips
Learn more about the key cost individuals in injection creating and actionable design tips that will help you reduce the costs of your project.
Expense drivers in treatment molding
The biggest costs in treatment molding are:
Pedaling costs determined by the total expense of designing and engineering the mold
Stuff costs determined by the quantity of the material used and its price for every kilogram
Production costs determined by the total time the Injection molding machine is used
Pedaling costs are frequent (starting at $3, 000 and way up to $5, 000). This cost is independent of the amount of created parts, while the material and generation costs are centered on the generation volume.
For smaller productions (1, 1000 to 10, 1000 units), the price tag on pedaling provides the greatest impact on the complete cost (approximately 50-70%). And so, it's worthwhile transforming your design consequently to simplify the manufacturing of the mold (and it is cost).
For much larger volumes to full-scale production (10, 1000 to 100, 000+ units), the side of the bargain of the pedaling costs to the complete cost is outweighed by the stuff and production costs. So, most of your design efforts should give attention to minimizing the two amount part and the time of the molding cycle.
Below we collected some recommendations to help you minimize the price tag on your Injection cast project.
Tip #1: Check out the straight-pull mould
IM 101 - Check out the straight move mould
Side-action induration and the other in-mold mechanisms can improve the expense of pedaling by 15% to 30%. This explicates to a bare minimum additional cost for tooling of about $1, 000 to $1, 500.
Throughout a previous part, we examined ways to deal with undercuts. To take care of generation on-budget, avoid side-action cores and other mechanisms unless absolutely necessary.
Tip #2: Redesign the treatment molded part to avoid undercuts
Undercuts always add cost and complexity, as well as maintenance to the mould. A clever renovate can frequently eliminate undercuts.
Tip #3: Help make the injection cast part smaller
Small parts can be molded faster causing in a higher production output, making the cost for every part lower. Small parts also cause lower material costs and reduce the buying price of the mold.
Hint #4: Fit multiple parts in one mould
IM information - Tip #2: Fit multiple pieces in the same mould
As we saw in a previous section, appropriate multiple parts in the same mould is common practice. Usually, 6 to 8 small the same parts can easily fit into the same mould, essentially reducing the overall production time can be 80%.
Pieces based on a geometries can also fit in the same mould (remember, the model airplane example). This kind of is a great solution for lowering the complete cost of assembly.
Here's an advanced technique:
Occasionally, the key body of 2 parts of an assembly is the same. Using some creative design, you can create interlocks points or hinges at shaped locations, essentially reflecting the business. This kind of way the same mold can be used to production both halves, reducing the tooling costs in half.
Hint #5: Avoid small details
To production a mold with small details require longer machining and finishing times. Text message is an example of this and might even require specialized machining techniques such as electric powered discharge machining (EDM) resulting in higher costs.
Tip #6: Use lower class completes
Finishes are usually applied to the mold by hand, that can be a high priced process, especially for high-grade finishes. In the event that your part is not for plastic use, don’t apply a costly high-grade finish.
Tip #7: Minimize the part volume by lowering wall fullness
IM OR HER 101 - Hint #3: Minimize the part volume by reducing the wall membrane thickness
Reducing the wall thickness of your part is the best way to minimize the part volume. Certainly not only does it mean less stuff is employed, but also the injection creating cycle is greatly accelerated.
For illustration, reducing the wall membrane thickness from 3 mm to 2 mm can reduce the cycle time by 50% to 75%.
Thinner wall surfaces signify the mould can be loaded quicker. More notably, parts thinner pieces cool and harden much faster. Do not forget that about half the injection molding pattern is spent on the solidification of the part even though the machine is stored idle.
Care must be taken through to not extremely reduce the rigidity of the part which will downgrade it is mechanical performance. Steak in key locations enables you to increase rigidity.
Tip #8: Look at secondary operations
Intended for lower volume production (less than multitude of parts), it can be more cost effective to utilize a second functioning to perform your injection molded pieces. For example, you may drill a pit after molding quite than using an expensive mold with side-action cores.
Element 5
Start Treatment creating
Once your design ready and optimized for treatment molding, what’s next? In this particular section most of us take you through things needed to get started on manufacturing with treatment molding.
Step a single: Start small and prototype fast
IM OR HER 101 - Get started small & original fast
Before you commit to any expensive injection creating tooling, first create and test a practical prototype of your design.
This kind of step is crucial for launching a prosperous product. This way design errors can be discovered early, while the price tag on change remains to be low.
There are 3 solutions for prototyping:
3D producing (with SLS, SLA or Material Jetting)
CNC machining in plastic-type material
Low-run treatment molding with 3D IMAGES printed molds
These kinds of processes can create realistic prototypes for form and performance that closely appear like the appearance of the final treatment molding product.
Utilize information below as a quick comparability instructions on decide which solution is suitable for your application.
Prototyping with 3D producing
Min. quantity: a single part
Typical cost: $20 - $465.21 per part
Prospect time: 2 - 5 days
Study more about this procedure →
Designs maximized for injection creating can be easily 3D printed
Typically the prototyping solution with the minimum cost and most effective turnaround
Certainly not every injection creating material is offered for 3D producing
3D IMAGES printed parts are 30-50% weaker than injection molded pieces
Prototyping with COMPUTER NUMERICAL CONTROL machining
Min. variety: 1 part
Normal cost: $100 - $500 per part
Lead time: 5 - week
Study more about this process →
Stuff properties identical to the injection cast parts
Excellent accuracy and reliability and polishing off
Design and style modifications may be need, as different design restrictions apply
More expensive than 3D printing with longer lead time
Prototyping with low-run injection molding
Minutes. quantity: 10 - 100 parts
Normal cost: $1000 - $4000 total
Prospect time: 5 - week
Learn more about this process →
The most realistic prototypes with accurate material properties
The actual process and mold design is simulated
Typically the prototyping solution with the highest cost
Smaller availability than CNC or 3D IMAGES producing
Step 2: Make a "pilot run" (500 - 10, 000 parts)
Make a preliminary run (1000 - 10. 000 parts)
Together with the design finished, it time to get started with Injection molding with a tiny pilot run.
The minimum order volume for treatment molding is five-hundred units. For these quantities, the conforms are usually COMPUTER NUMERICAL CONTROL machined from lightweight aluminum. Aluminum molds are relatively easy to manufacture and low in cost (starting at about $3, 000 to $5, 000) but can withstand up to five, 000 - 10, 000 treatment cycles.
At this stage, the typical cost per part varies between $1 and $5, with respect to the geometry of your design and the selected material. Typically the typical lead moment for such orders is 6-8 weeks.
Rarely get confused by the term “pilot run”. If you only require a few thousand pieces, then this would be your ultimate production step.
Typically the parts created with "pilot" aluminum conforms have physical properties and accuracy the same to parts created with “full-scale production” tool steel conforms.
Step 3: Range up production (100, 000+ parts)
IM OR HER 101 - Your own up production (100. 000+ parts)
If producing parts enormous quantities of the same parts (from twelve, 000 to hundred, 000+ units) then special Injection creating tooling is required.
For these volumes of prints, the molds are CNC machined from tool steel and can withstand large numbers of Injection creating cycles. Fortunately they are prepared with advanced features to maximize generation speeds, such as hot-tip gates and intricate cooling programs.
The typical product cost at this stage varies between a few mere cents to $1 and the typical prospect time is 4 to 6 several weeks, due to the complexity of building and manufacturing the mold.
Part 6th
Useful resources
Throughout this guide we reviewed everything you need to get started with treatment molding - but there's plenty more to learn.