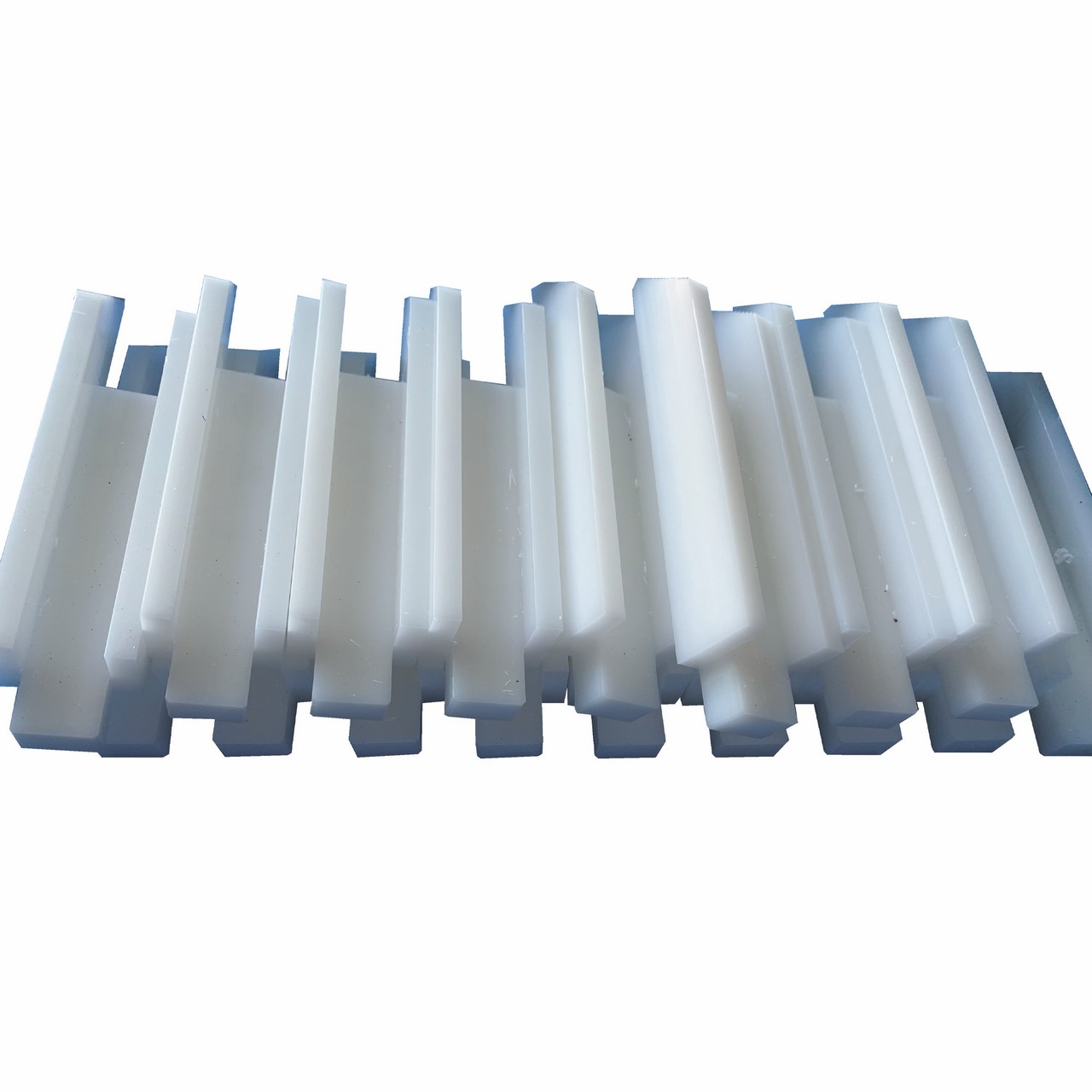
Pc Numerical Control (CNC) machining is a subtractive manufacturing process that permits manufacturers to accurately and cost-effectively create high-precision parts. CNC engineering removes excess natural material from components with cutting tools to produce a precise completed product from materials like plastic, metallic, and composites.
These types of days, product groups have lots of options in regards to multi-axis machining, from 3-axis to 5-axis to even 9-axis machining. What’s the difference between each kind? In this article, we’ll break up the key commonalities and distinctions between two popular types of CNC engineering (3-axis vs. 5-axis) — and describe in order to might make sense to utilize one over the other.
3-axis machining
Following the operator enters milling instructions into a pc, the 3-axis COMPUTER NUMERICAL CONTROL machine will automatically complete the job by by using a tool to slice along 3 axes — By, Y, and Z ., or left-to-right, front-to-back, and up-and-down. Each CNC milling and CNC turning drop under the coverage of 3-axis engineering. However, they functionality slightly differently.
Whenever by using a 3-axis CNC milling machine, the materials block remains set in a bassesse or on the machine bed. Rotating exercises or cutting tools are attached with a spindle and move along the By, Y, and Z . axes, removing bits to accurately make up the final component. 3-axis CNC milling machines are excellent for producing most geometries and parts.
Simply by contrast, in the CNC turning process, the workpiece is attached to a rotating spindle, and a lathe designs the component. Since the spindle holding the workpiece rotates, a middle drill or cutting tool remnants the component’s external and inner perimetres or creates openings across the center axis. In comparison to CNC milling machines, CNC lathe turning machines produce parts faster and offer cheaper per-unit costs, which is advantageous for high-volume production runs.
Given that a 3-axis COMPUTER NUMERICAL CONTROL machine can simply reduce along three responsable, it may have trouble with non-conventional shapes or designs with heavy, narrow cavities that are difficult to reach. When digesting parts with complicated geometries, operators could have to by hand reposition the workpiece, which can sluggish down the digesting speed, raise work and machining costs, and bring about a less-than-perfect finished product.
5-axis machining
5-axis machines rely on a tool that moves in 5 different directions — X, Y, and Z, in addition to a and B, around which the tool revolves. Using a 5-axis CNC machine allows operators approach a part every which way in a single operation, removing the need to manually reposition the workpiece between procedures. 5-axis CNC engineering saves some is well suited for creating complicated and precise components like those found in the medical, oil and gasoline, and aerospace sectors. There are a few different sorts of 5-axis machines that product groups should be aware of, including listed 5-axis CNC machines, continuous 5-axis COMPUTER NUMERICAL CONTROL machines, and mill-turning CNC centers.
Such as 3-axis CNC milling, the cutting tool only moves together three axes and doesn’t maintain constant contact with the workpiece in listed 5-axis CNC engineering. However, the engineering table and tool head can automatically swivel in two directions between procedures. Indexed 5-axis engineering is great for manufacturing housings, lures, and fixtures. This falls approximately 3-axis CNC milling and continuous 5-axis COMPUTER NUMERICAL CONTROL machining in phrases of speed, accuracy, and the opportunity to manage complex geometries.
Within continuous 5-axis COMPUTER NUMERICAL CONTROL machining, the trimming tool and the workpiece can turn and move concurrently during operation, preserving time and allowing operators to produce intricate geometries with organic and natural surfaces. Continuous 5-axis CNC machining offers improved surface complete, speed, and dimensional stability, but it has the greatest cost-per-part.
5 axis CNC machining
Switching mill CNC facilities are practically similar to CNC switching machines, with one exception — they are equipped with COMPUTER NUMERICAL CONTROL milling equipment. The particular workpiece is connected to a spindle that can turn or remain fixed while cutting tools remove material from it. By merging the elements of CNC lathe machines with milling tools, mill-turning CNC facilities offer high levels of accuracy and geometric versatility, making them great for creating parts with loose rotational symmetries, such as camshafts or centrifugal air compressors.
Nearly these kind of 5-axis COMPUTER NUMERICAL CONTROL milling machines offer greater accuracy when machining deeper components and hardened materials, nevertheless they also offer higher yields and faster machining rates of speed. Nevertheless , 5-axis engineering much more expensive because of to the specific equipment necessary and the need for expert workers.
3-axis machining versus 5-axis machining
The between 3-axis and 5-axis milling machines is that the workpiece can be worked well on from 3 axes with the former and 5 axes with these. Both are highly versatile, automated, and replicable production procedures that will enable you to quickly and cost-effectively create accurate components. Nevertheless , you may choose to use one over the other for a variety of reasons.
Ought to you be on a budget or only have to cut a smooth surface, 3-axis machines might be the way to go. Not only is it more affordable than those with five axes, 3-axis machines are better to program, so you won’t have to incur the expense of working with expensive expert programmers and operators. Plus, preparation time is smaller with 3-axis engineering.
If you need to produce a deeper part or one with complicated geometry, you’ll probably might use 5-axis machining. Using 5-axis machines enables you to machine the workpiece from all sides — no manual rotator required. With 5-axis machining, you’ll have higher yields, higher accuracy, and increased freedom of motion, as well as the ability to manufacture larger components faster.
Visit our resource center to find out more about CNC engineering, including techniques for decreasing costs and design best practices.