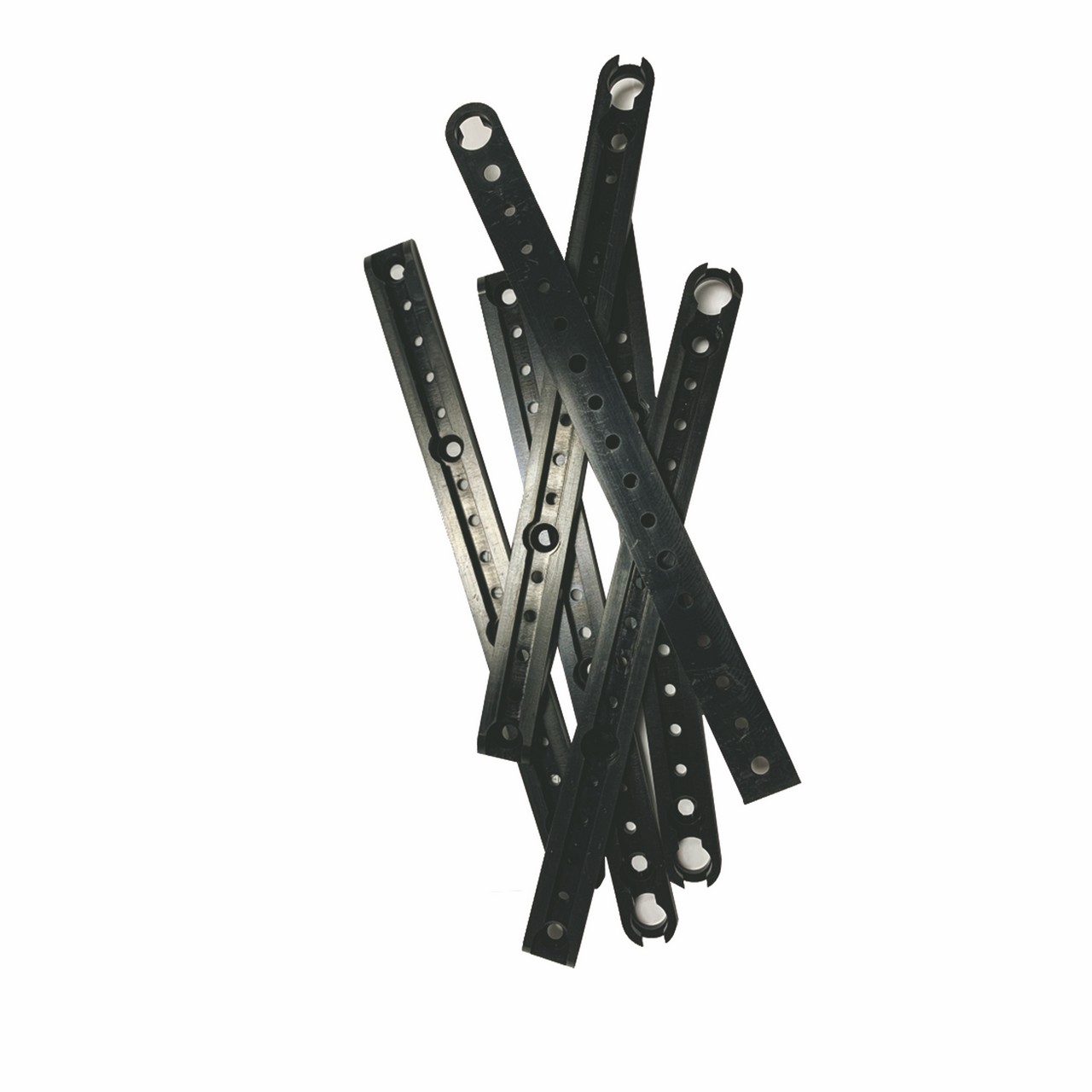
COMPUTER NUMERICAL CONTROL milling, or computer numerical control milling, is a engineering process which uses computerized controls and rotating multi-point slicing tools to steadily remove material from the workpiece and produce a custom-designed part or product. This method is suited to machining an array of materials, such as steel, plastic, glass, and wood, and producing a variety of custom-designed parts and products.
Several features are offered under the umbrella of precision CNC engineering services, including mechanised, chemical, electrical, and thermal processes. COMPUTER NUMERICAL CONTROL milling is a mechanical machining process along with going, turning, and many different other machining techniques, meaning that substance is removed from the workpiece via mechanical means, like the actions of the milling machine’s slicing tools.
This informative article concentrates on the COMPUTER NUMERICAL CONTROL milling process, setting out the basics of the method, and the components and pedaling of the COMPUTER NUMERICAL CONTROL milling machine. In addition, this article is exploring the various milling functions and provides alternatives to the CNC milling process.
Milling Explanation
Just what is milling? Is actually is a type of machining that uses cutters to form a workpiece, often on the portable tabletop, even though some milling machines also include movable cutters. Milling started out as a manual activity performed by humans, several milling these days is performed by a CNC work, which utilizes your computer to oversee the milling process. COMPUTER NUMERICAL CONTROL milling offers higher precision, accuracy, and production rates, but there are still some situations when manual milling comes in useful. Guide milling, which needs a lot of specialized skill and experience, offers shorter transformation times. It also gets the added profit that manual generators are cheaper and an individual doesn’t need to worry about programming the machine.
Introduction to CNC Milling Procedure
Like most conventional mechanical COMPUTER NUMERICAL CONTROL machining processes, the CNC milling process utilizes computerized settings to operate and manipulate machine tools which cut and form stock substance. In addition, the process follows the same basic creation stages which all CNC machining techniques do, including:
Creating a CAD model
Converting the CAD model into a CNC program
Establishing up the COMPUTER NUMERICAL CONTROL milling machine
Carrying out the milling procedure
The CNC milling process starts with the creation of any 2D or 3 DIMENSIONAL CAD part design. Then the completed design is released to a CNC-compatible extendable and changed by CAM software into a COMPUTER NUMERICAL CONTROL machine program which dictates the steps of the device and the movements of the tooling across the workpiece. Ahead of the operator runs the CNC program, they prepare the COMPUTER NUMERICAL CONTROL milling machine by affixing the workpiece to the machine’s work surface (i. e., worktable) or workholding device (e. g., vise), and attaching the milling tools to the device spindle. The COMPUTER NUMERICAL CONTROL milling process uses horizontal or up and down CNC-enabled milling machines—depending on the requirements and requirements of the milling application—and rotating multi-point (i. e., multi-toothed) slicing tools, such as mills and exercises. When the machine is ready, the operator launches the program with the machine interface prompting the machine to carry out the milling procedure.
Once the COMPUTER NUMERICAL CONTROL milling process is initiated, the machine starts rotating the cutting tool at speeds reaching upwards to 1000s of RPM. Depending on the kind of milling machine utilized and the requirements of the milling application, as the tool cuts into the workpiece, the device will perform one of the next actions to produce the necessary reduces on the workpiece:
Slowly feed the workpiece into the stationary, rotating tool
Move the tool over the stationary workpiece
Move both the tool and workpiece in relation to the other person
As compared to manual milling processes, in COMPUTER NUMERICAL CONTROL milling, typically the machine feeds portable workpieces with the rotation of the cutting tool somewhat than against it. Milling functions which adhere to this tradition are known as climb milling techniques, while contrary functions are known as conventional milling techniques.
Generally, milling is best suited as a secondary or finishing process for an already precision machined workpiece, providing explanation to or producing the part’s features, such as slots, slots, and strings. However, the method is also used to form an investment piece of substance from learn to end. Both in cases, the milling process slowly removes material to form the required form and form of the part. Very first, the tool reduces small pieces—i. at the., chips—off the workpiece to form the approximate form and form. Then, the workpiece undergoes the milling process at higher accuracy and with greater accurate to finish the business with their exact features and specifications. Typically, a completed part requires several machining moves to achieve the desired precision and tolerances. For more geometrically complex elements, multiple machine setups may be asked to complete the fabrication process.
Once the milling procedure is completed, and the part is produced to the custom-designed requirements, the milled part passes to the finishing and post-processing stages of creation.
CNC Milling Device Operations
Types of pedaling for milling machine operations, including blades, drills, and broaching bits.
Types of pedaling for milling machine operations, including blades, drills, and broaching bits.
Image Credit score: Sugrit Jiranarak/Shutterstock. possuindo
CNC milling is a machining process suited to producing high accuracy, high threshold parts in modele, one-off, and small to medium creation runs. While elements are typically produced with tolerances varying between +/- zero. 001 in. to +/- 0. 005 in., some milling machines can achieve tolerances as high as and greater than +/- 0. 0005 in. The versatility of the milling process allows it for use in an array of industrial sectors and for a variety of part features and designs, including slots, chamfered edges, threads, and wallets. The most typical CNC milling functions include:
Deal with milling
Plain milling
Angular milling
Contact form milling
Face Milling
Face milling pertains to milling functions in which the cutting tool’s axis of rotation is perpendicular to the surface of the workpiece. The process employs face milling cutters that have the teeth both on the periphery and tool face, with the peripheral teeth mostly being used for cutting and the face teeth becoming utilized for concluding applications. Generally, face milling can be used to create flat areas and contours on the finished item and is in a position of producing higher quality finishes than any other milling processes. Both up and down and horizontal milling machines support this process.
Types of face milling include conclusion milling and side milling, which use conclusion milling cutters and aspect milling cutters, correspondingly.
Plain Milling
Basic milling, also referred to as surface or slab milling, refers to milling functions in which the cutting tool’s axis of rotator is parallel to the surface of the workpiece. The particular process employs basic milling cutters that have teeth on the periphery that perform the cutting procedure. Depending on the specifications of the milling application, like the depth of the cut and the size of the workpiece, both filter and wide blades are employed. Narrow blades permit deeper reduces, while wider blades are employed for slicing larger surface areas. If the plain milling application requires the removal of a huge amount of substance from the workpiece, the operator first employs a coarse-toothed cutter, slow slicing speeds, and fast feed rates to produce the custom-designed part’s approximate angles. Then, the user introduces a better toothed cutter, faster cutting speeds, and slower feed rates to produce the important points of the completed part.
Angular Milling
Angular milling, also referred to as angle milling, describes milling functions where the cutting tool’s axis of rotation are at an angle in accordance with the surface of the workpiece. The method uses single-angle milling cutters—angled based on the particular design being machined—to produce slanted features, such as chamfers, serrations, and grooves. One common using angular milling is the creation of dovetails, which employs 45°, 50°, 55°, or 60° dovetail cutters in line with the design of the dovetail.
Form Milling
Form milling pertains to milling functions involving irregular areas, contours, and information, such as elements with curved and flat surfaces, or completely curved areas. The process uses formed milling blades or fly blades specialized for the particular application, such as convex, curvy, and corner rotating cutters. A few of the common applications of form milling include producing hemispherical and semi-circular cavities, beads, and contours, as well as intricate designs and complex elements with a individual machine setup.
Additional Milling Machine Functions
Apart from the aforementioned functions, milling machines can be used to accomplish other specialised milling and engineering operations. Examples of the other types of milling machine functions available include:
Straddle milling: Straddle milling refers to milling functions in which the machine tool machines several parallel workpiece areas with a individual cut. This process employs two blades on the same machine arbor, set up in a way that the blades are in either aspect of the workpiece and can work both equally attributes at the same time.
Gang milling: What is team milling? Gang milling describes milling functions which employ two or more cutters—typically of varying size, shape, or width—on the same machine arbor. Each cutter machine can perform the same cutting procedure, or a different one, simultaneously, which produces more elaborate designs and intricate parts in reduced production times.
User profile milling: Profile milling refers to milling functions in which the machine tool creates a slice path along a vertical or viewpoint