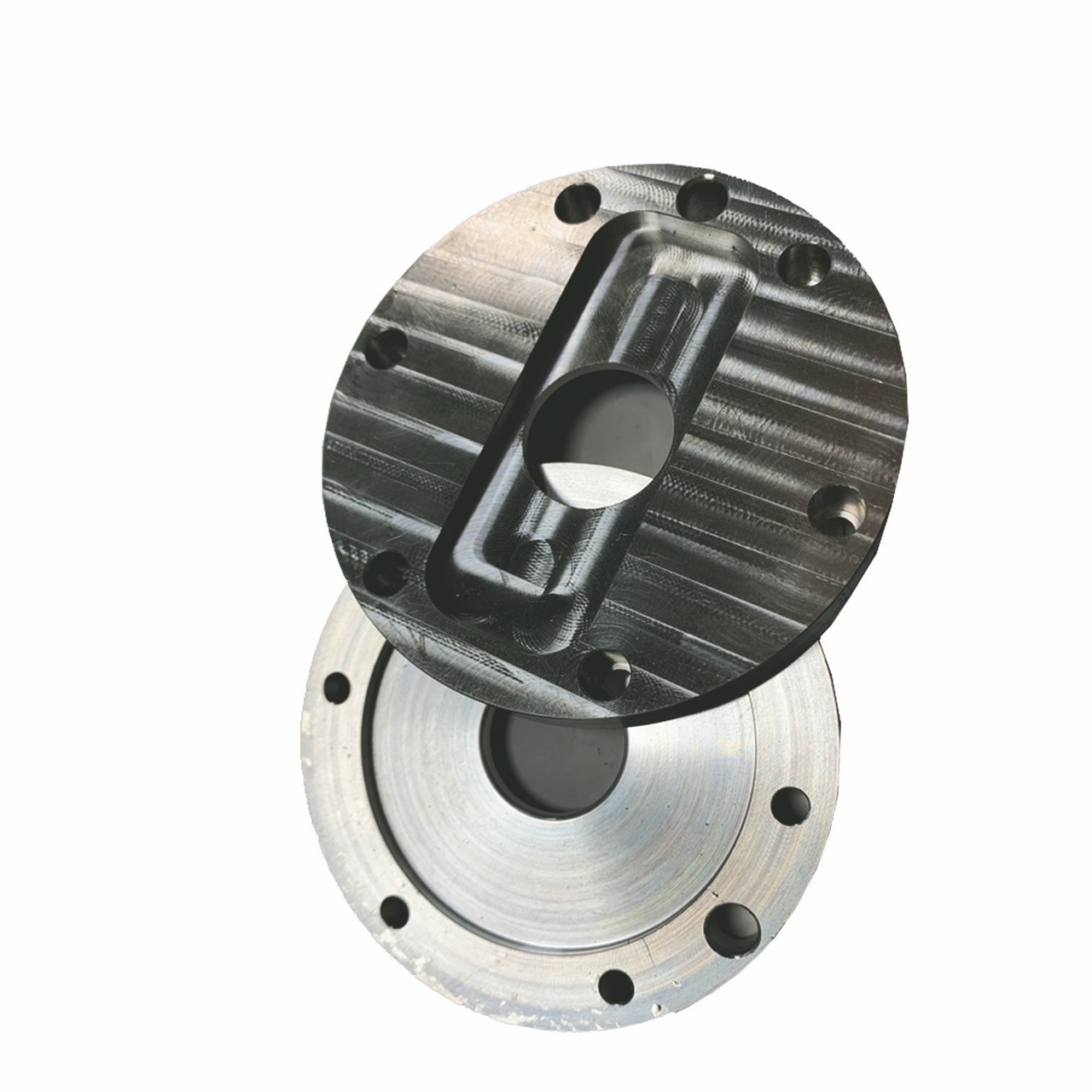
Just what CNC Milling Device and how really does it work? Just how do CNC milling machines compare to COMPUTER NUMERICAL CONTROL Lathes? When do you need such a CNC machine tool?
Focused on milling – the process of engineering using rotating tools to slowly remove material from a workpiece – COMPUTER NUMERICAL CONTROL milling machines are a mainstay for factories around the world. These machine tools utilize a variety of slicing tools along one or more responsable to remove substance from your workpiece through mechanical means.
COMPUTER NUMERICAL CONTROL milling machines are often employed in a variety of producing industries: from industrial sectors like aerospace, delivery, automobiles, and olive oil drilling / growing and refining, to medical, FMC producing, and precision executive sectors.
Also called CNC Machining Facilities, the more superior CNC milling machines can operate together multiple-axis. These may be fitted with programmed tool corrigers, advanced machine coolant systems, pallet corrigers, and advanced software to increase the efficiency and reliability of machining techniques.
In this article, we are looking at the next facets of a COMPUTER NUMERICAL CONTROL Milling Machine/ Engineering Center:
What is a CNC Milling Machine?
How really does a CNC Milling Machine work?
COMPUTER NUMERICAL CONTROL Milling Machine compared to CNC Lathe
Just what are the key components of a CNC Milling Device?
Do you know the cutting tools utilized by a CNC Milling Device?
What are the several types of COMPUTER NUMERICAL CONTROL Milling Machines?
Simply how much does a COMPUTER NUMERICAL CONTROL Milling Machine cost?
Where can you buy CNC Milling Machines?
Just what COMPUTER NUMERICAL CONTROL Milling Machine/ Engineering Center?
First, let us look at exactly what a CNC milling machine is.
COMPUTER NUMERICAL CONTROL Milling Machines are machine operated slicing tools that are programmed and maintained by Computer Statistical Control (CNC) systems to accurately remove materials from a workpiece. The conclusion result of the machining process is a specific part or product that is established by using a Computer Assisted Design (CAD) software.
These machine tools are normally outfitted with a main spindle and three-linear-axes to position or move the part to be precision machined. More complex versions could have a fourth or 5th rotating axis making possible more precise gradation of varying dimensions and sizes to be machined.
CNC milling machines / engineering centers normally use a process of material cutting called milling or engineering – the milling process involves protecting a piece of pre-shaped material (also referred to as workpiece) to a fixture attached to a platform in the milling machine. A rapidly revolving tool (or a series of compatible tools) is then placed on the substance to remove small chips of the fabric until the desired condition for the part is achieved.
Depending on the materials for the part, as well as the complexity of the machined part, various axes, cutting mind speeds, and nourish rates may be applied.
Milling is normally used to machine parts which are not shaped from an central perspective. These elements could have unique curvatures or surface contours, which may require a blend of drilling & tapping, grooves, slot machine games, recesses, pockets and holes to work in it. They may also form elements of the pedaling for other producing processes – for example in the fabrication of 3 DIMENSIONAL moulds.
Features of Advanced CNC Milling Machines / COMPUTER NUMERICAL CONTROL Machining Centers
Inside the past, milling machines were managed by hand. Workers had to use a blend of machines with different tools to machine an even more complex part or product. Or even they'd to use various settings on one machine in order to complete the job.
With the improvement of technology such a CNC settings and Automatic Application Changers (ATCs), better efficiency, overall versatility and speed can be achieved : even for more convoluted parts. The particular provision of digital readouts and computing systems has also improved the reliability of CNC engineering processes.
To serve to manufacturers that need the overall versatility of “High Combine, Low Volume” (HMLV) or “small batch” production, CNC engineering centers can be when you have Pallet Changers or other automation strategies to form part of any Flexible Manufacturing Cellular (FMC) or Versatile Manufacturing System (FMS). This allows such machines to serve to numerous engineering demands and wishes.
Need to learn read more about CNC Milling Machines for your company?
E mail us
Just how does a COMPUTER NUMERICAL CONTROL Milling Machine work?
The general basic principle for a COMPUTER NUMERICAL CONTROL milling machine or CNC machining middle would be that the part to be machined is clamped on top of the machine table. It could be clamped on the table itself, or held in place by a vice or fitting.
The spindle (moving section) like the slicing tool can now be either vertically or flat positioned. For the reason that settings, the tool can reach various X-Y-Z positions on the work piece and initiate cutting and shaping actions. Since it does so, the work item or part may either be set, mounted, or moved/positioned by the desk in a geradlinig direction to the spindle with the cutting tool. This enables material to be removed in range with the desired condition needed for the machined part.
A CNC milling machine may either be horizontal or vertical.
You can see how shows up in the made easier diagram below.
COMPUTER NUMERICAL CONTROL Milling Machine Compared to CNC Lathe (Turning Center)
While COMPUTER NUMERICAL CONTROL Milling Machines are machine tools similar to a CNC Lathe, both tools operate quite differently.
For a CNC milling machine (aka CNC engineering center), the work piece is set or mounted in position by using a vice or fixture as the slicing tool is manoeuvred on top of or just around the piece. Substance is then slowly removed using slicing tools or exercises which rotate at high-speed with various feed rates together several axes.
Inside the case of a CNC Lathe (aka CNC Transforming Center), however, the work piece (usually cylindrical) is installed on a revolving chuck or on the key spindle. It truly is then “turned” (hence the name turning Center) or rotated along a main axis as the cutting tool positioned in a rotational or positioning turret would move in a parallel direction to the piece. Substance can now be removed using stationery cutting tools.
Thus, a COMPUTER NUMERICAL CONTROL milling machine use a spinning tool with a letter head work piece, whilst a CNC Lathe would involve re-writing the fabric to be labored on by a stationery slicing tool.
Want to upgrade or buy CNC Milling Devices for your company?
Click Here For more information
What are the Main Aspects of a CNC Milling Device?
So what are the several parts of a CNC Milling Machine or Engineering Center? The plan below provides a breakdown from the main components.
#1 Frame
The body is the key structure that facilitates the milling machine and helps to provide stability and rigidity. It usually includes a base and detachable column/s.
A great important part of the frame is the machine headstock the location where the key spindle is mounted on. The headstock, while important, is often overlooked. In the event the headstock is not inflexible and does not provide stability and support to the spindle, you could get vibrations and chattering through the engineering operation. This might bring about machining errors and a shorter life-span to your slicing tool.
#2 Spindle
The spindle can be considered as the “heart” of a CNC milling machine. It normally comprises a revolving assembly, and a tapered section where tool holders may be positioned. The particular shaft of the spindle is normally the location where the tool is mounted on, usually via a tool owner.
A motor with different levels of transmission can be used to rotate the spindle.
In order to keep spindle in good condition within the long-term, various kinds of lubrication are used. They might include Oil Lubrications (not suited to long durations of high speed operations), Air-Oil Lubrications (sufficient for longer routine runs at higher speeds) or the Hwacheon Oil-Jet-Lubrication (ideal for those conditions : even extreme, long and high rate applications).
According to the machine type, the spindle can be top to bottom or horizontally placed.
#3 Responsable
Inside general, CNC milling machines have Times / Y and Z as well as additional rotating axis or D / A or B (subject to configuration). These can be programmed using g-code in the CNC controller.
#4 Column/s
The content of the COMPUTER NUMERICAL CONTROL machining center can be single (eg travelling column HiRex 4000 or also C-Frame like Strike 400 / fish hunter 360; VESTA line including “B”; SIRIUS-650 and 850 / 1050) or double (SIRIUS 1250 / 2300 / L1 and L2). This will depend on the amount of complexity needed in the engineering task.
#5 COMPUTER NUMERICAL CONTROL The control -panel
This is the key “nervous system” of the device tool. It contains the electronics that helps to manage the several slicing actions through encoding functions. The control panel has a CNC monitor and programming buttons where data and unique codes can be smacked in. It usually also supplies a guide function. For simplicity of machine procedure, the control -panel should be easily accessible and within easy reach.
#6 Tool / Application Changers (Automatic Application Changer or ATC)
These are either mounted at the column or individually mounted to the machine. These is preferred if greater tool changers are needed with 45 up to 3 hundred different tools. Accomplishing this not only helps you to save time and effort – it also helps your operators to avoid unnecessary vibrations during operation.
#7 Application Holders
These come in many different sizes, systems and for various apps. The standard dimensions for tool slots are BT 35 to BT 45 and BT 55 (BT refers to the taper viewpoint of the cone on the holder).
(In Europe, the term used is SK 30, SK 40 or SK 50, which has the same viewpoint as BT owner using an additional orientation groove at the flange. Collectively with a key-stone mounted at spindle nose, SK slots can be directed in a specific position. Eg.: uninteresting bridges, boring night clubs, angular milling minds and so on )---
For higher rigidity and well balanced fast rotations, BBT versions are suggested or the HSK System.
The particular BBT version is definitely an up-graded version of the standard BT system providing dual contacts between the tool holder and spindle. As a result, it connects and a genuine more strongly, provides significantly less vibration as the tool holders are well balanced to class Queen 2 . not 5. This specific boosts not only the machining features and outcomes of your machine tool, but provides better surfaces to bank account / mould, expands your tool life and finally helps you to save spindle replacements in the long term as bearings can last longer.
What about the HSK Method? It truly is lighter (good for HSC machining), shorter (good for faster tool change), and better than the BT system (a HSK-A63 owner is 2 . not 5 times better when compared to a BT 50 holder). The HSK Method also offers excellent balancing (Class Queen 2 . not 5). Credited to the strong and powerful clamping from inside to outside, the binding involving the tool owner and the spindle is well suited for heavy duty operations, heavy cuts or extremely high-speed functions at the same time.
Both the BBT and HSK types offer far firmer and more inflexible bonding between the tool holder and spindle mainly because these systems come with dual contact clamping (i. e. between the caper / cone and front spindle nose surface).
#8 Desk
The desk supplies a solid bottom to lock the work piece on, and can be used to install fixtures or bassesse to hold the piece in place. Almost all of the tables use T-slots for easy clamping of bassesse, fixture or part.
On Horizontal COMPUTER NUMERICAL CONTROL milling machines, pallets are available too with Tap-holes. These types of allow greater versatility in moving different work pieces to be machined. Significantly, magnets are also being used for easy, fast and secured clamping. These types of should preferably be built into the machines table to avoid the reduction of Z-axis elevation.
(See Hwacheon’s SIRIUS UM+ for instance. )
#9 Coolant Reservoir
Most CNC engineering centers have a coolant tank to help supply coolant to the slicing surface and also the spindle with tool during machining action. This specific helps to extend the life-span of the machine and its parts. Over and above this, the coolant will also remove heat created by the machining action, and hence keep temperatures under control.
To carry a sufficient amount of coolant for cutting functions, the rule here is “the more, the better. ” More coolant helps machine operators to avoid the increased temperatures up of coolant.
Generally, the CTS system or Coolant Through Spindle is recommended for further drilling functions (deeper than 4 times diameter) or when one is engineering deeper cavities in mould & perish applications. The standard should be 30bar with choice of upwards to 70bar in coolant pressure. Just very specific apps would require even higher coolant challenges.
Attention has to be given if tools with larger coolant hole diameters are employed. Such machining needs may require a High Pressure : High Flow Charge Pump to be used.
Have a replicate of our COMPUTER NUMERICAL CONTROL Milling Machines brochure here
Request At this point
What are the Milling Tools that CNC Milling Equipment use?
On the whole, COMPUTER NUMERICAL CONTROL milling machines can deploy a variety of reducing and shaping tools. These tools aid to remove material thanks to how they move within the machine or direct from the cutter’s shape.
These may include the subsequent:
Ending Mills, Flat or Ballnose, Straight or Form Tools.
Confront Mills
Drills, U-Drills, Spiral Borer.
Shoes
Reamers
Tool Owners and Hydraulic Instrument Holders, Shrink-Fit or Press-Fit holders.
Precisely what are the Distinct Types of COMPUTER NUMERICAL CONTROL Milling Machines?
There are many variations and types of CNC Milling Machines – from simple two to three axes machines to multi-axis COMPUTER NUMERICAL CONTROL machining centers. Normally speaking, the key different versions are either Top to bottom or Horizontal engineering centers.
Here are some of the types that you could find in the market:
Horizontal Milling Equipment
Vertical Milling Equipment
Bed Mill
Turret gun Mill (for handbook machines only)
Exploring Steering column
Double Steering column
C-Frame
Drill & Engage
Five Axis Machining Centers
Twice Spindle (VESTA-500T & VESTA-650T)
When you look at the right COMPUTER NUMERICAL CONTROL milling machine for your machining needs, it pays to to consider your specific requirements in words of your made part dimensions, complexness from the condition and design, need for accuracy, as well as the machine longevity and stability.
C-Frame Top to bottom Machining Centers
Top to bottom Machining Centers (VMCs) can normally take the condition of a C-Frame, the traditional design for a VMC. These kinds of are restricted to a certain machine size – further than this, the hang over of the spindle and overall machine floor space required could become too big.
(Examples here include Hwacheon’s VESTA series or SIRIUS-650 as well as 850 / 1050 and also 7040 / 7050. )
Double Column Engineering Centers
Double Steering column machining centers are normally used for larger parts and machine sizes. Yet , smaller sized high precision milling machines may also be fashioned with a twice column to improve their rigidity and accuracy. (Examples here include Hwacheon’s SIRIUS UM+ / UL+ / UX as well as 1250 / 1350 / 1750 as well as 2500 and L1 / L2)
Equipment that are made for milling simple parts with lower accuracy standards are normally lower in price (and features) compared to those used for mould & die software which require the highest accuracy and production standards.
Exploring Column Machining Centres
Travelling Column Engineering Centers (like Hwacheon’s Hi-Rex 4000 as well as 5000 / 6000) are CNC milling machines where stand and work part are stationary and do not move. Every one of the three thready axes movements made by the exploring column consisting of the spindle as well as the reducing tool. These machines are specially suitable for a very long but slimmer (Y-axis direction) parts or to enable multiple-clamping applications of the workpiece.
Double/ Multi-Spindle Machining Centers with Pallet Changers
Generally equipped with Pallet Changers, vertical or horizontal double or multi-spindle machining centres are top-end COMPUTER NUMERICAL CONTROL milling machines. These are generally made to achieve optimal yields in productivity and are suitable for the size production of sophisticated parts.
The use of computerized pallet changers helps to reduce down times while increasing production and efficiency. That they can even be deployed as part of your factory automation process (read this article for more. )
Multi-Axis CNC Engineering Centers
Most COMPUTER NUMERICAL CONTROL milling machines come in the standard 3-axis up to 5-axis for engineering very complex forms (ie mold & die) or sophisticated parts which need to be found in various angles. Using multiple axis, the machining on way up to five looks are provided in a single placing.
High Speed and High Capacity Engineering Centres
Also known as HSC machines, high speed engineering centers can be used to achieve not only the highest surface completes for the made part, but for handle tools with extremely small diameters – as little as 0. 030 mm in size or smaller.
In the same way, high capacity engineering centers are created and built to look after extreme tough materials. Such materials include Heat Resistant Stainless steel Steel, Inconel or Titanium – just to name a few. (Hwacheon Lateral Machining Centers such as H6 & H8 as well as our Top to bottom Machining Centers such as VESTA B-series and the much larger SIRIUS line of machine are created to take care of these without problem. )