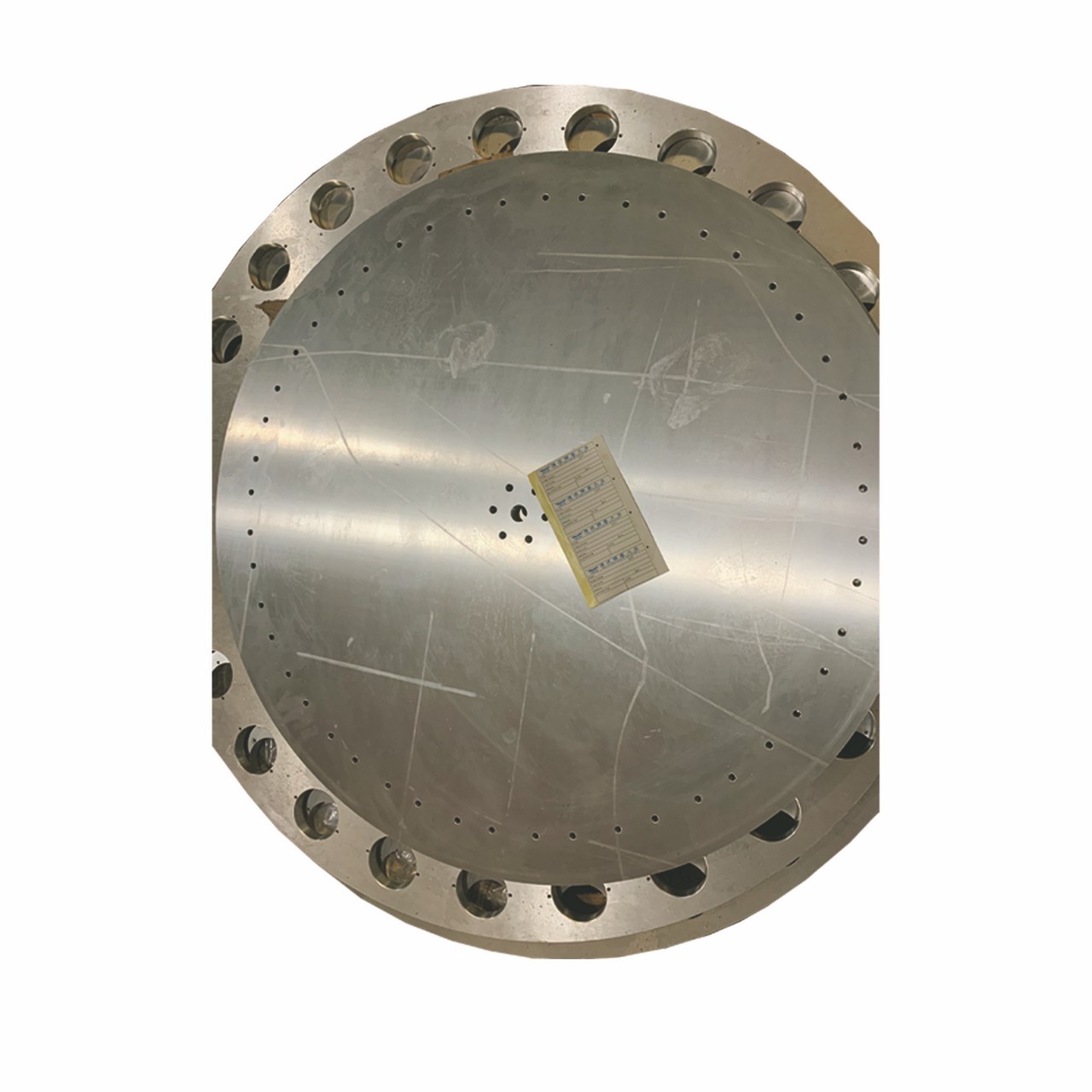
Tips on how to design parts for CNC machining
In this particular complete guide to designing for COMPUTER NUMERICAL CONTROL machining, we've created basic & innovative design practices and here are some hints you achieve the best results for your custom parts.
There are a few easy steps you can earn to optimize your designs for computer statistical control (CNC) engineering. By following design-for-manufacturing (DFM) rules, you can get more out of COMPUTER NUMERICAL CONTROL machining's broad functions. This is challenging though, as industry-wide specific standards do not exist.
In this article, we give a comprehensive guide to the best design practices for COMPUTER NUMERICAL CONTROL machining. To make this intensive up to date information, we inquired for feedback from industry experts and CNC machining companies. If you are optimizing for costs, check out their guide to building cost-effective parts for CNC. CNC engineering is a subtractive manufacturing technology. Throughout CNC, material is taken from a sturdy block by using a variety of cutting tools that rotate at high speed—thousands of RPM—to develop a part based on a CAD model. Equally metals and materials can be Cnc machined.
CNC-machined parts have high dimensional accuracy and reliability and tight tolerances. CNC is well suited for both high amount production and one-off jobs. In simple fact, CNC machining is currently the most cost-effective way of producing metal representative models, even compared to 3D printing.
Precisely what are the key constraints of CNC design?
CNC offers great design flexibility, but there are a few restrictions. These kinds of limitations correspond with the basic mechanics of the cutting process and mainly worry tool geometry and tool access.
Instrument geometry
Most common CNC cutting tools (end mill tools and drills) have a cylindrical condition and a constrained cutting length.
While material is removed from the workpiece, the geometry of the tool is transferred to a machined part. This kind of means, for illustration, that the inside corners of a CNC part always have a radius, no matter how small a reducing tool was used.
Tool access
To be able to remove material, the cutting tool strategies the workpiece immediately from above. Capabilities that cannot be accessed in this way cannot be Cnc-machined.
There is an exception to the rule: undercuts. There are a section on undercuts towards the ending of the article.
A good design practice is to align your model’s features (holes, cavities, vertical wall surfaces, etc. ) to a single of the half a dozen principal directions. Yet , see this concept as a advice and not a restriction, as 5-axis CNC systems offer advanced workpiece-holding functions.
Tool access is also a concern when machining features with a sizable depth-to-width rate. To reach the base of a serious cavity, for example, you need tools with extended get to. This means a wider range of motion for the ending effector, which increases the machine chatter and lessens the achievable accuracy and reliability.
It can simplify generation if you design parts that can be CNC made with the tool that has the most significant possible size and the least possible length.
COMPUTER NUMERICAL CONTROL design guidelines
An issue that frequently arises while designing an element for CNC engineering is that no industry-wide specific criteria exist. CNC machine and tool manufacturers consistently increase the technology’s capabilities, expanding the limits of what is possible. Typically the table below summarizes recommended and possible values for the most frequent features encountered in CNC machined pieces.
Recommended cavity degree: 4x cavity breadth
End mill tools have a constrained cutting length (typically 3–4 times their diameter). Tool deviation, chip evacuation and vibrations are more well known when cavities have smaller depth-to-width rate.
Limiting the degree of the tooth cavity to four times its width ensures good results.
In the event that larger depths will be required, consider designing pieces with a changing cavity depth.
Serious cavity milling: Space with depths higher than six times the tool diameter are thought deep. A tool diameter-to-cavity depth rate up to 30: a single may be possible using particular tooling (maximum degree: 35 cm with a 1-inch size ending mill tool).
Vertical corner radius
Recommended: times tooth cavity depth (or larger)
While using recommended value for internal spot radii ensures that a suitable size tool can provide and aligns with guidelines for the recommended cavity degree.
Increasing the spot radii slightly above the recommended value (e. g. by 1 mm), allows the tool to cut following a circular path as opposed to a 90 perspective. It is preferred as it results in a higher quality surface finish. In the event that sharp 90 education internal corners are required, consider adding a T-bone undercut as opposed to reducing the corner radius.
Floors radius
Recommended: zero. 5 mm, a single mm or no radius
Feasible: any radius
End generator tools have a flat or a little bit rounded lower reducing edge. Other floor radii can be machined using soccer ball ending tools. Its good design practice to use the recommended values, as it is preferred by the machinists.
Minimum wall fullness
Recommended: 0. 6 mm (metals), 1 ) 5 mm (plastics)
Feasible: 0. 5 mm (metals), 1 ) 0 mm (plastics)
Decreasing the wall membrane thickness reduces the stiffness of the fabric, which improves vibrations during engineering and lowers the achievable accuracy. Materials are susceptible to warping (due to residual stresses) and softening (due to temperature increase), so a larger bare minimum wall thickness is recommended. The possible values explained above should be reviewed on a case-by-case basis.
Diameter
Advised: standard drill tad
Feasible: any size larger than a single logistik
Holes are machined using either a drill tad or an ending mill tool. Typically the size of the drill bits is standardized (in metric and imperial units). Reamers and monotonous tools are widely-used to finish holes that require tight tolerances. For high- accuracy and reliability holes with a diameter smaller than 20 mm, by using a standard diameter is recommended.
Maximum degree
Recommended: 4x moderate diameter
Typical: twelve times nominal size
Feasible: 40 times nominal diameter
Gaps with a weird diameter must be machined with an ending mill tool. In this circumstance, the maximum tooth cavity depth restrictions apply and the advised maximum depth value should be used. Holes deeper than the conventional value are machined using particular drill bits (with a baseline diameter of 3mm). Blind gaps machined with a drill have a conical floor (135 angle), while gaps machined with an ending mill tool are flat.
Generally there is no particular preference between through holes or impaired holes in COMPUTER NUMERICAL CONTROL machining.
Thread size
Minimum: M2
Advised: M6 or much larger
Threads are minimize with taps and external threads with dies. Taps and dies can be used to minimize threads down to M2. CNC threading tools are common and are preferred by machinists, as they limit the risk of engage breakage. CNC threading tools can be used to minimize threads down to M6.
Thread span
Minimum: 1 ) 5 times nominal size
Recommended: 3 times nominal diameter
Typically the majority of the load applied to a thread is taken by the few first pearly whites (up to a single. five times the nominal diameter). Posts longer than 3 times the moderate diameter are thus unnecessary.
For posts in blind gaps cut with shoes (i. e. all threads smaller than M6), add an unthreaded length similar to 1 ) 5 times the moderate diameter at the bottom of the hole. When a CNC threading tool can be used (i. e. posts larger than M6), the hole can be threaded during its length.
Bare minimum hole diameter
Advised: installment payments on your 5 logistik (0. 1 inches wide. '')
Feasible: zero. 05 mm (0. 005 inches. '')
Most machine retailers can accurately machine cavities and gaps using tools down to 2. 5 mm (0. a single inches) in size. Anything below this limit is considered micro-machining. Speciality tools (micro-drills) and expert knowledge are required to machine such features because the physics of the cutting process difference in this scale. Until absolutely necessary, the recommendation is therefore to avoid them.
Typical: +-0. a single mm
Feasible: +-0. 02 logistik
Each of our tolerances are either 2768 medium or fine. If tolerances are not particular, manufacturing partners makes use of the selected 2768 grade.
Tolerances specify the boundaries for an acceptable aspect. The achievable tolerances vary in line with the basic dimension and the geometry of the part. The principles above are fair guidelines.
Text and lettering
Recommended: typeface size 20 (or larger), 5 logistik engraved
Engraved text message is preferred over embossed text, as less material is removed. Using a the least size -20 sans -serif font (e. grams. Arial or Verdana) is recommended. A lot of CNC machines have pre-programed routines for anyone fonts.
CNC machine setups and components orientation
Tool entry is one of the primary design restrictions in CNC engineering. To achieve all areas of the model, the workpiece needs to be rotated multiple times.
Whenever the workpiece is rotated, the machine needs to be recalibrated and a new coordinate system needs to be defined.
While developing, it is very important consider machine setups for two reasons:
The entire quantity of machine setups impacts the cost. Rotating and realigning the business requires manual work and increases total engineering time. This could be suitable if the business needs to be rotated up to three or four times, but something above this restrict is excessive.
In order to achieve maximum family member positional accuracy, two features must be machined in the same setup. It is because the new adjusted step introduces a little (but non-negligible) mistake.
What is 5-axis CNC machining?
The 5-axis CNC machine moves cutting tools or parts together five axes at the same time. Multi-axis CNC machines can manufacture components with complex geometries, as they provide two additional rotational responsable. These machines eliminate the requirement for multiple machine setups.
Exactly what are the advantages and limitations of 5-axis CNC engineering?
Five-axis CNC engineering allows the tool to stay constantly tangential to the trimming surface