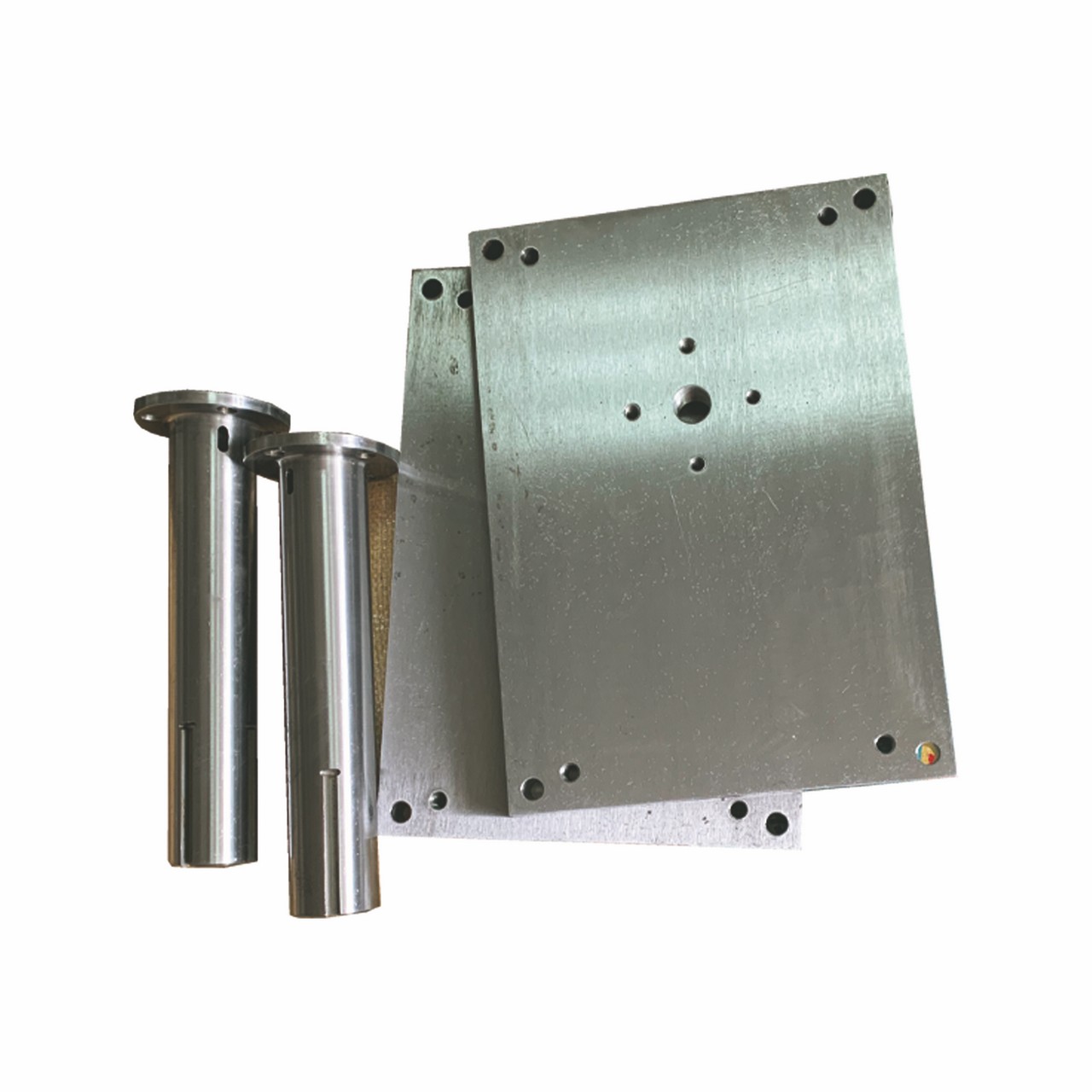
Precision machined Parts
Machining generally describes a producing process in which a worker utilizes sharp cutting tools to remove excessive material from a part in order to create a desirable new form.
Castings, forgings, extrusions, bar stock and even raw materials can all provide substrates for the process of engineering.
Typically, machining comprises a secondary procedure. It usually requires cutting away and discarding a part of the material.
The particular machining rarely shows economical when it involves removing more than 40% of the of the part. If so, the manufacturer should depend on other producing techniques, such as forging or spreading.
The final form of the part conforms to measurements specified by the manufacturer. Companies use machining to add features to or refine an existing metal component. Machinists may also clean the surface of a part to achieve a better finish. Nowadays, engineering allows for the production of steel parts within high tolerance levels.
Producing facilities frequently apply machining to add desired features to metal components. The particular features might include slots, slots, flattened areas, pockets, or even complex exterior marks.
Applications
In nowadays modern world, many industries utilize specifically machined parts. Firms furnishing semiconductor, tail wind, automotive and dietary fiber optics products all depend on engineering for the design of certain components.
Machining as a process is generally cost-effective, however the duration of the method varies significantly. Engineering by well-equipped manufacturers usually offers the benefit of low installation and tooling costs.
Nevertheless , when the process of engineering requires a long time period to complete per part, it can add considerable costs to overall production expenses.
That is why, many manufacturers restrict the use of machining involving an substantial time dedication to the design of any limited amount of detailed representative models.
Products with brief machining times frequently permit cost-effective high volume production operates. In the situation of some smaller parts easily and rapidly fabricated from bar stock, engineering provides a highly cost-effective solution.
Engineering Operations
Our company employs three main types of traditional machining functions in order to eliminate excessive material from steel parts.
The functions include turning, going, and milling. Throughout these processes, machinists utilize sharp slicing tools to by mechanical means cut away small chips of substance from the first segment.
Each procedure differs slightly from the others:
Transforming
Turning refers to the procedure in which a machinist moves metal against the cutting tool by carefully revolving the workpiece on a lathe machine. A lathe helps you to form metal using a rotating drive which turns the metal component at desired angles.
Transforming will generate cylindrical-shaped parts that show various specified interior or external features. Typically, turning functions encompass boring, going through, grooving, thread slicing and the cut-off process, also known as parting.
Proceeding
Drilling can be used to generate holes on a workpiece, or improve how big existing slots. A machinist usually performs this step by utilizing a cylindrical, rotating tool exercise bit.
The small amount penetrates the stationary metal part so as to create a hole. The particular machinist relies on a drill press to perform fast precision drilling.
Milling
A 3rd extensively performed machinist procedure, milling involves transferring a metal part facing a cylindrical rotating tool with multiple cutting ends known as milling cutter. A machinist uses a milling machine to effectively get free of any excess elements of the cloth.
In addition to these three main machining operations, our company also provides secondary functions so as to produce elements meeting manufacturer specs. The secondary functions might include shaping, planing, boring, broaching, or sawing.
Categorization of machining processes
Inside general, all engineering processes can be divided into two distinct machining categories: conventional and non-conventional. The processes fluctuate according to the tools used for removing excessive material.
Conventional Engineering
Conventional machining symbolizes a mechanical process. Machinists use a sharp tool to cut away excessive material from a part. The process can be further divided into about three sub-categories:
1) Individual point cutting: This method refers to utilizing a cutting tool with just one sharp advantage that turns, airplanes and shapes the part.
2) Multi-point cutting: Multi-point slicing involves a slicing tool with two or more slicing edges to work, drill, broach or saw the part.
3) Abrasive engineering: During the process of abrasive engineering, a machinist utilizes small abrasive allergens to hone, work, lap or gloss the business. The particular process may also include ultrasonic and abrasive jet engineering.
Non-Conventional Machining
Non-conventional machining processes cover two sub-categories: chemical substance machining and energy machining.
Chemical engineering: This method involves using baths of temperature-regulated etching chemicals. The particular chemicals remove substance from the business, thus creating a metal component of a specified form. Chemical machining can be a regular or an electrochemical process.
Thermal engineering: This method employs a source of energy energy, for instance a laserlight or an business torch, to immediate intensive heat towards a metal part in order to eliminate excess material. Varieties of thermal machining include torch cutting, power discharge machining and high energy ray machining.
Why Consumers Choose Our Engineering Providers
At XIEJIN, you can easliy provide a variety of engineering services and techniques in order to manufacture an array of custom metal parts game particular customer requirements.
Our company uses highly experienced and knowledgeable machinists who have got the resources required to supply various machining services. Our experts have the ability to manage complex engineering tasks.
The company maintains versatile equipment able to performing well under manufacturing conditions and tailored to zero defects.
The machinery allows us all to complete projects for customers successfully and accurately. As a result, the in-house engineering features of XIEJIN conserve our customers both time and money.
We provide just-in-time delivery so which our customers may avoid unnecessary supply storage costs. We all offer inexpensive price points and exceptional customer care for all our clients.