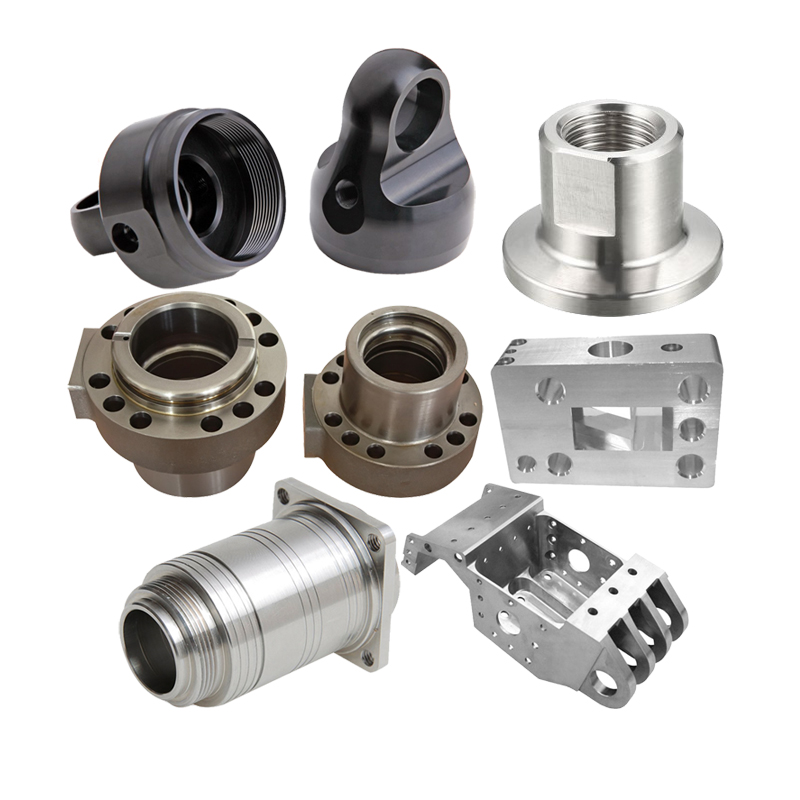
Computer system Numerical Control (CNC) machining has become increasingly common in manufacturing. CNC technology supplies a versatile, computerized means to produce large-volume runs of high-quality parts. Profit levels of accuracy and reliability and repeatability proposed by CNC machining operations ensure it is a great tool for some manufacturers.
Computer numerical control Machining - Anything You Need to be aware of
WHAT IS COMPUTER NUMERICAL CONTROL MACHINING?
In basic, CNC machining pertains to one of many reductive operations that take stuff away from a workpiece to accomplish a design. COMPUTER NUMERICAL CONTROL processes use electronic controls to take care of the complete machining process from learn to surface finish, in the end producing constantly precise parts. COMPUTER NUMERICAL CONTROL machining equipment can follow the same sets of instructions over and over again to aid small or large production runs of identical pieces.
COMPUTER NUMERICAL CONTROL machines come in multiple varieties and levels of intricacy. Some machines can hold multiple tools at the time or work alongside X, Y, and Z axes to remove excess stuff from any area or any kind of time perspective.
CNC machining can be used to create elements and components for nearly every industry and application. This specific includes the jetstream industry and other highly complex companies that need engineering work on large parts. Manufacturers can use this procedure on substrates such as:
Composite materials
Froth
Glass
Metals
Plastic-type material
Wood
CNC engineering is particularly useful due to the automated efficiency. Automation allows the machines to operate self-sufficiently, requiring less human labor to produce accurate elements. A growing industry deficit of skilled machinists and employees has been a primary contributor to the advancement of CNC technology in recent years.
A FEW MANUFACTURING PROCESSES
Most of the time, there are a few types of developing processes:
Reductive. Reductive or subtractive operations like machining take material away from a workpiece to create a design.
Additive. Additive developing processes blend or assemble different elements together to create a finished product. 3D printing is the most frequent form of additive manufacturing.
Conformative. Formative manufacturing bends or otherwise changes are the base to suit the design requirements. Formative developing includes processes like injection molding, in which the base is melted and then pressed in an impression to hold a certain shape. It also includes many steel forming processes, such as bending or rolling.
CNC ENGINEERING PROCESS OVERVIEW
Typically the predecessor to COMPUTER NUMERICAL CONTROL machining—numerical control (NC) machining—used punched strapping cards and basic commands. CNC engineering follows more intricate commands and makes use of a greater variety of controls. These kinds of systems both teach the cutting and forming tools that remove, but COMPUTER NUMERICAL CONTROL machining equipment can follow complex, custom-made sets of instructions that come from complex CAD or CAM designs.
Distinct CNC machining equipment will manage different tools, capabilities, and businesses. The CNC engineering process typically includes these general steps:
1 ) DESIGNING TYPICALLY THE CAD MODEL
Just before the CNC engineering process starts, manufacturers need to make the product design. Computer-aided design (CAD) software can be used to create thorough two-dimensional (2D) or three-dimensional (3D) models. These design data files include details including the geometries, dimensions, and other technical technical specs of the elements. CAD software makes up the limitations of machining processes and the properties of the chosen materials.
For example, if the design contains slots formed by cylindrical tools, CAD software can inform design engineers when designs are too intricate for a given substrate or identify potential problems thanks to limitations in the selected process. These automated investigations help CAD/CAM design services and designers avoid many prospective errors during the rendering process so the prototyping period is more useful.
2. CONVERTING CAD FILES TO WORKABLE CNC INSTRUCTIONS
After the design is complete, the design technical specs should be translated into directions that COMPUTER NUMERICAL CONTROL machines can follow. The CAD data files are run through computer-aided manufacturing (CAM) software. These programs create the encoding code that COMPUTER NUMERICAL CONTROL machines use for primary the tools through the manufacturing process. This specific software also brings out information about the part angles that operators can use to ensure the initial workpiece has the right dimensions and positioning.
These CNC-compatible pieces of instructions are often in one of two file types: STEP or IGES. They include encoding languages such as G-code and M-code, which each take care of specific areas of the machine tool’s functionality. G-code functions give attention to the genuine functioning of the equipment, such as their speed, the course of motion, and how far they move. M-code functions give attention to miscellaneous businesses, such as energizing on and off and other additional functions.
3. SETTING UP THE CNC EQUIPMENT
Human operators play a much smaller role in computerized manufacturing than in manual manufacturing, nevertheless they still handle important functions that the machinery can’t deal with. This can include:
Loading the CNC program record to the machine
Putting the workpiece to the machinery spindles or vices so the machine can manipulate the workpiece
Attaching the required machining tools
Examining the work area, machine, and workpiece
4. EXECUTING BUSINESSES
After the equipment is prepared and the program starts, the CNC machining equipment executes the steps and conducts engineering functions on the workpiece. The program can complete the necessary reductive operations from learn to surface finish without further user input. Once the instructions have recently been completed, the part can continue through finishing and the labels processes.
SORTS OF COMPUTER NUMERICAL CONTROL MACHINING BUSINESSES
COMPUTER NUMERICAL CONTROL machining is definitely a extensive category of possible functions and operations. Among CNC engineering operations, drilling, milling, and turning will be the most common.
GOING
Drilling processes use bits with a diameter the same size as the diameter of the desired hole. Typically the machining equipment inserts the spinning exercise bit perpendicularly to the workpiece until it drills a pit of your predetermined span. More advanced equipment can produce angular slots, and drilling tools provides features such as:
Counterboring
Countersinking
Reaming
Going
MILLING
The milling process removes cuts of material from the workpiece by moving the material against a spinning reducing edge. The equipment have multiple cutting items, and each tool spins to provide a sharp reducing surface with a different length and shape. When the workpiece is hard pressed against milling tools, thin strips or cuts of stuff are taken out of the existing edge. This may create shallow reductions, wide cuts, or flat-bottom cavities to condition the part. Peripheral milling operations may cut more deeply to make slots or threads into the piece’s general condition.
TURNING
Turning operations turn the workpiece as opposed to the reducing tool. They include cutting processes such as boring, grooving, and facing. They will cut excess stuff off of a workpiece by using single-point cutting tools precisely applied to the rotating workpiece. Turning creates cylindrical parts which may have a specified diameter. Transforming can create thready features both inside and on the exterior edge of the parts. These kinds of features include:
Video poker machines
Threads
Battres
POSITIVE ASPECTS OF CNC ANATOMIST
Many manufacturers favor machining processes because they create elements or components coming from a single workpiece. COMPUTER NUMERICAL CONTROL machining has several additional advantages. Like for example ,:
Increased productivity. Establishments with CNC engineering can produce pieces 24/7. The machines may run consistently with little-to-no man intervention. The machines also require less space than work stations or manual engineering setups, so a facility with a set total area can have more machines running together.
An increased degree of accuracy. CNC engineering uses highly thorough programming operations. Typically the machines follow these instructions without allowing any unwanted deviation or human problem. The parts will be high-quality, specific, and identical. COMPUTER NUMERICAL CONTROL machining can also produce parts with intricate, complex designs.
Faster project achievement. Every CNC engineering process depends on a CAD design, so the prototyping process will be faster. The software catches or inhibits many possible design flaws or prospective risks based on a materials. When the prototyping and testing operations are shortened, numerous go from design into production faster. CNC machining instructions can even be modified or replaced quickly, so there is little delay between changes in production works.
Cost-effectiveness. CAD data file designs and reduced risks of producing errors reduce the per-unit cost of production. CNC engineering also requires less human labor, which further reduces the price of developing these products.
CNC ENGINEERING FROM PRO-TYPE DEVELOPING
Can be seeking a complete developing solution, Pro-Type Companies, Incorporated gives a standard of value and process overall flexibility that is unmatched in the industry. We operate a state-of-the-art center that comes with some of the most advanced COMPUTER NUMERICAL CONTROL machining systems available.
These are high-torque, high-RPM systems that deliver precision and productivity all in one package. One of these is our 550 mm Toyoda COMPUTER NUMERICAL CONTROL 4-axis horizontal generator. This state of the art system features spindle boosts to 15, 1000 RPM delivered through a 30 HEWLETT PACKARD motor. Which has a 30” work cube and 2400” each min positioning, it can power through materials such as lightweight aluminum, steel, and materials at high rates with maximum accuracy and reliability. It also allows us to assist hard-to-machine materials such as Inconel, Invar, Monel, and various superalloys.
Yet , this is merely one of our many precision machining systems. We also operate four CNC usable mills that can accommodate workpieces way up to 64” by 32” by 25”, two horizontal generators equipped with multiple pallets, and a high-output CNC lathe with auto rod feed, sub-spindle, and live tooling. Throughout the hands of our team of seasoned machinists, these high-precision machining can deliver tolerances within ±0. 0005”. These functions and resources are augmented by in-house fabrication coming from all tooling and fixturing, giving us increased control over production.
Through our practically 5 decades as a manufacturer, we have learned that few project requirements comprise of machining only. To incorporate even more value to the service offerings, we also provide value added software program as:
Welding
Decoration
Chromating
Passivation
Complete assemblage
Comprehensive dimensional records
Material traceability
All of of our work is backed way up by a sturdy ISO 9001 quality management system and culture that runs to all of our organization.
Coming from a single prototype to high volume umbrella orders that amount many months or longer, the key to the success is our potential to supply same level of value and quality in spite of run size or design complexity. To be able to find out about all of our manufacturing functionality, or to ask a quote, email us directly.