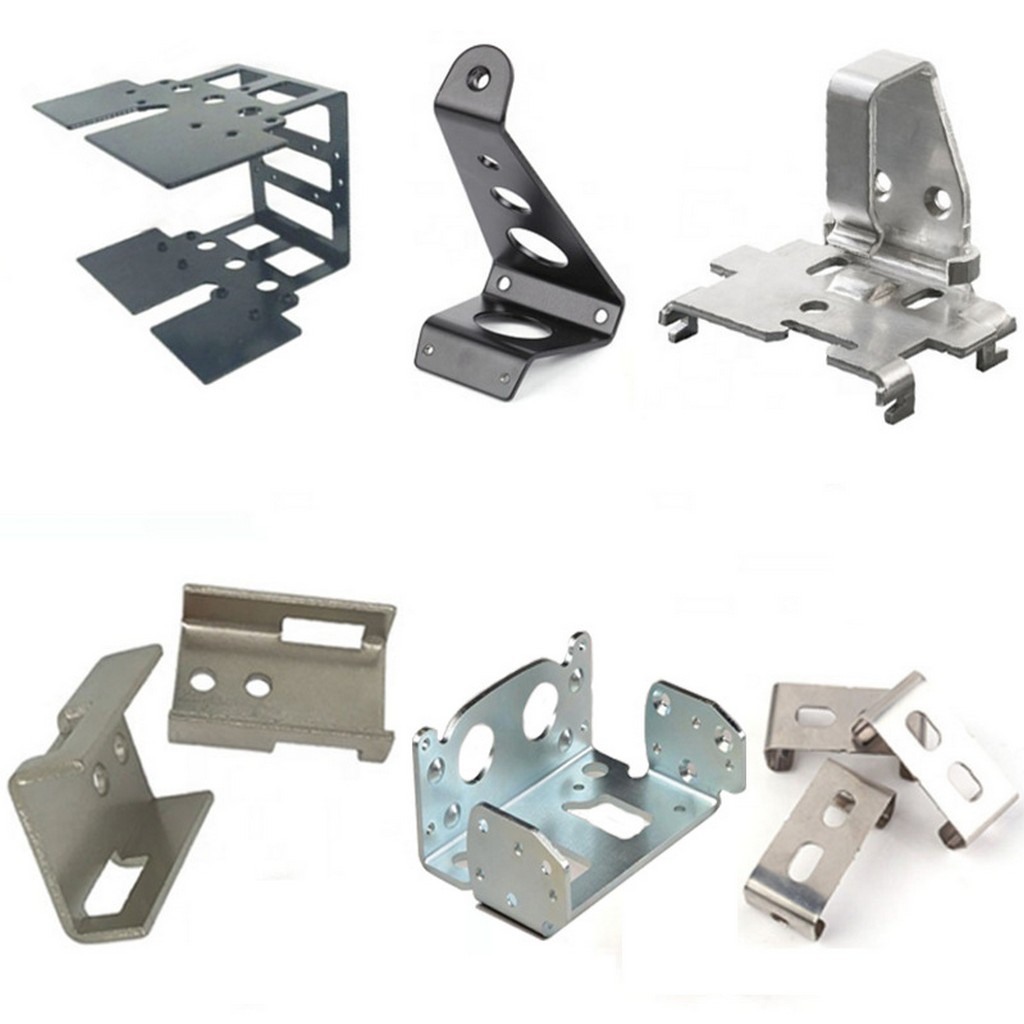
When comparing to conventional stamping at room temperatures, hot stamping has a variety of advantages. First, hot rubber stamping parts can homogeneously distribute toughness and decrease springback, as proven in Figure 8 conducted by means of the authors 'team working with Baosteel B1500HS. Therefore, the dimensional accuracy from the parts may be greatly improved and extra size procedures may be eliminated. Furthermore, the forming load is even reduced at elevated temperatures, plus the investment for any press with larger tonnage will get considerably reduced. An additional from hot stamping is based on the opportunity of reducing the amount of forming stages which have been required in cold stamping, equally well as decreasing the great number of presses and forming equipment. For instance, just one stage can have to form a N- pillar by direct popular stamping, whereas conventional stamping is made up of tools for a number of stages.
The essential characteristics from IHPF would be the integrated building of assorted cross- portions 'hollow parts which includes two- or three a significant dimensional axis from the principal circle section of the tube to kind of square, trapezoid, ellipsoid, or other varied closed portions( 5). The common manufacturing for this sort from part is stamping of a couple of half parts after which welding together for many whole part. In order to reduce the deformation of welded, the sections weren't entirely closed by virtue of from spot weld used usually( Figure 6). Moreover, it is extremely tough to meet the requirement from structure the style of the reason of simple section geometries from stamping parts. From the angle of process techniques, the characteristics of IHPF in contrast to rubber stamping and welding process are while follows( 5–8):
Second, hot rubber stamping offers the opportunity for synchronous charge of complex microstructrures during thermomechanical processing. This technique can form parts with widely varying technical properties and combinations by implementing an individual blank, which lessens blanking costs and allows regarding a simple transition of technical properties. These hot- rubber stamped parts with tailored properties can simply avoid particular problems under drive conditions whenever using material with native soft areas( 13). Additionally, sophisticated geometries predicated on a thicknesses and strength levels may be created by tailored blanks in popular stamping. Several conventionally formed parts may be integrated in a definite hot- stamped element of achieve financial savings in body- in- white creation. Therefore, the- rubber stamped part spectrum could be optimized by new applications.
1.
Minimized weight and savings in elements. For that structure parts through the chassis and frame from your car body, system.Drawing.Bitmap of IHPF parts is minimized 20–40% in comparison to stamping parts, and the will get reduced 40–50% for hollow essentiel parts.
2.
Reduced part and die amounts and costs. A definite pair of die is wanted usually for IHPF parts, contrary to a multiset of dies could be required for stamping parts. While demonstrated in Figure 7, the quantity of areas of a subframe is reduced from six parts related to stampings to at least one part through IHPF.
Sign-upto download whole- size image
Figure sete. Structure a a comparison of some subframe( a) stamping part, and( b) IHPF part.
3.
Minimized amount of machining and welded subsequently. As an example, the rad support structure is by way of using IHPF, the location of warm dissipation is increased by 43%, and the total amount of location welds is reduced from 174 to twenty. The amount from procedures is reduced from 13- 14 to six, then the organization rate was increased by 66%.
4.
Increased strength and firmness, particularly for fatigue strength. Under the same exemplory case of rad support is required: the power could be increased 39% for your vertical course and 50% for that horizontal course.
5.
Higher ratio details utilization. The items utilization rate of IHPF is 90–95%, though exactely stamping is 60–70%.
6.
Lower production charge. Depending on your characters of an organization in Indonesia, the cost of IHPF parts is 15% under regarding stamping parts, plus the expenses of dead of IHPF parts are 20–30% lower than those patients of rubber stamping parts.
6. 6. 1 Popular stamping of boron steels regarding automobile parts requiring improved drive reluctance
Martensite steels are excellent but challenging to form therefore two steps of creating and heat therapy are generally needed. Hot stamping combines both stages in one technique and supplies an answer to00 several system.Drawing.Bitmap forming super a substantial high- strength steels round the direction these days 's R&D trend of fabric processing. The stamping offers various advantages including greatly improving formability for hi- strength and light-weight materials( which typically show an unhealthy formability in accordance with traditional forming conditions), reduces along with eliminates springback and reduces building load for overcoming press insert limitation. Additionally it allows the enhancement of complex stamping part geometries or integrated parts, to guaranteeing that the final number from stamped parts and tools can typically be reduced( as a way of reducing tooling cost). Present in this technique blanks are pre- heated to 900–1000° C in a austenite temperatures range, and quenched inside water- cooled stamping expire set to make martensite a significant based microstructures. To stop oxidation process at elevated temperatures an lightweight aluminum- boron coating is usually put on the blanks.
Based mostly on two reports by Munera et al. 35 and Image et al., 36 in get to generally meet safety requirements for your crash from front, side, along with rear directions, and under some rollover condition without compromising car weight, monolithic and TWB boron steels are under development present in the steel industry. For model, at ArcelorMittal a two a significant step development program is underneath way. The initial step is ty trying monolithic boron steels for inspecting vehicle crashworthiness performance of three stamping parts: side member, N- pillar reinforcement and prominent- finish bumper. Enough time step is to take into account some TWB solution. An assessment amongst monolithic solutions and TWB answers was presented to look for the extra advantages( e. g. weight saving, energy absorption) that popular stamping TWB will offer. New steel grade for demanding crash zones was in reality under development that made the concept possible to considerably expand the applying type of press- toughened TWBs, but no detailed data can be acquired. Probably the favorite stamping TWBs need to utilize boron steel blanks of several thicknesses instead of using several materials apart from boron steel, until both parent materials can endure elevated temperatures without serious oxidation process.
For fabricating boron steel TWBs, the feasibility of utilizing some hybrid welding process with a laser in the key situation plus the arc welding walking was studied by Koganti ain al., 31 for welding aluminum coated coated boron steel. In these process the laser welding can easily offer broadband, deep puncture and low heat input in just the concentrated weld zone, but it surely requires good edge preparation without large gap variation. MIG welded uses filler material to passage the gap and allows an important edge fit- up ceiling, but has reduced welded speed and higher heat type, which tends to build up negative microstructures. Taking advantages from either processes, this hybrid welding strategy runs on the focused laser identify to make a vapor capillary 'keyhole' that improves the arc stability and welding acceleration. Aluminized coated boron steels( generally known as USIBOR) happen to be used as oxidation protection present in hot stamping and corrosion safeguard operating. Although this analyze used exactly the same material/ thickness for welding, the comes from the hybrid welding process plus the boron steel welding are best suited and therefore are briefly described below.
Within this study the booty welding( 'bead on menu') of boron steels by 1. 0 mm, 1. several mm and 2. 0 milimetre were studied as well as for run welding, the boron steel bedsheets at 1. 6 mm and 2. 0 mm thicknesses became studied. Good weldability was obtained for a number of studied cases. However, established on tensile coupon tests and microhardness measurements, substantial strength deals of HAZs in accordance with the beds base metal were observed regarding all welding cases studied. The outcome indicate that the answer strength is managed by the very last step welding process– the arc welding with filler that gave a lesser trying to cool off rate, even the procedure are able to increase welding speed significantly. The welded components, having a weakened HAZ out of this hybrid welded process, may raise serious toughness concerns if employed for last products, however, if used related to generating boron steel TWBs regarding hot stamping, some may well not turned out to be an issue. That is since preheating and hot- deformation in the austenite temperature line may just eliminate the inhomogeneity of weld zone microstructure and chemical composition. Truth continually be told there is absolutely no literary works included in forming tailored boron steel blanks. The formability from TWB boron steels in popular stamping deserves further investigation.