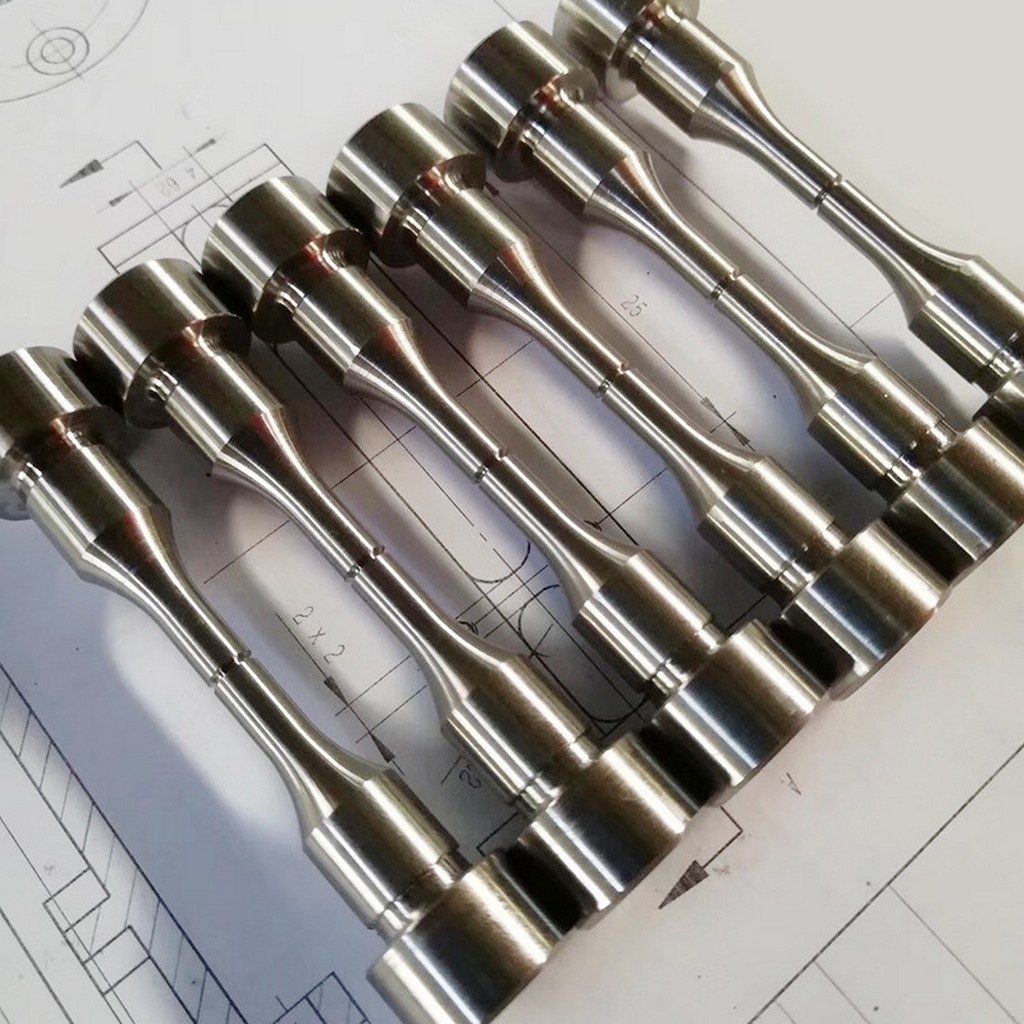
What is Investment Casting?
Expense casting is truly a manufacturing process where a wax pattern is generally coated using a refractory hard material. When the ceramic covering material is dry and solidified, the wax is melted away and leaves an interior tooth cavity the shape from the last product 's geometry. Molten metal is put to the cavity where the polish pattern was. The metal confirms in the ceramic cavity, lowers, plus the ceramic is eliminated from your metal casting. The consequence of this method is really a net to near- web precision metal component which might be used as a wide choice of applications in a variety of sectors.
Just why is it Called Expense Casting?
The ancient art and science of investment casting is normally also referred to as the shed wax process. Investment casting was made over 5500 years back and may trace its roots back to both ancient Egypt and China. Parts stated in industry by just this method include dental fittings, gears, cams, ratchets, jewelry, generator blades, machinery parts and other parts of complex geometry.
What is generally the Investment Casting Process?
Expense casting is really a manufacturing procedure where a liquid materials is poured into a difficult mold, which includes a useless cavity of the specified form, then in order to solidify. The proceduresolidified part may be the audition, that is broken away via ceramic mold to accomplish the method. Things in the expenditure casting process are as uses:
1: Engineering Review
First thing with this production process depends on a complete Layout For Manufacturing( DFM) review with the consumer.
This could incorporate an assessment of print proportions mainly because it pertains to the expenditure cast process, wax injection method build considerations such as for instance entrance placement, post- case information requirements and expected tolerances regarding fit, form and satisfaction from the business, and final inspection requirements to find out a mutually acceptable part.
ExpenseCasting Strategy Infographic step one
Step only two: Mold Design& Build
The method depends on a finely- detailed- engineered wax injection mould to create wax patterns which represents your final part.
These design facts to consider are discussed using the mould builder and an impression layout is done.
Our wax treatment molds are made here by Aero Metals at our for- house mold shop.
The molds are made and created to replicate lots of wax parts over its lifetime.
ExpenseAudition Process Infographic 2
3 or maybe more: Wax Pattern
The wax treatment mold is quantified so that you can formation and delivered to the Wax tart Room for injection and construction.
From one to 90 patterns are injected and located or glued onto a pre- fabricated wax runner program known as the "tree" present in our process.
The populated forest of wax parts is even known a cluster( of parts).
At that timetree cluster is at that time delivered to the Dip Place for part from the procedure.
ExpenseCasting Strategy Infographic 3
Step four: Porcelain Mold Construction
The initialwax forest is dipped and completely surrounded into ceramic slurry, removed, then completely coated in yellow sand to generate the very first element of shell, and dry.
This enveloping procedure for plunge and sand is repeated several or 8 times with a drying period between each a definite.
By repeating this action, it leads to a lamination effect creating some strong ceramic shell across the wax pattern as known while "investment". The shell now functions through our drying system related to 24 to 36 hours in front of removing the wax from your shell.
ExpenseCasting Process Infographic Step four
Step five: Via- waxing
The shell, composed of the wax pattern which is coating of ceramic and yellow sand, lies into an autoclave to quickly take away the wax based on extremely questionable and steam temperature.
This vessel helps to really have the shell set up along with steam heat quickly melts the wax out creating an the ceramic mold, hence the definition of "lost wax" casting.
The porcelain shell can then be relocated for the foundry ovens to begin with the casting process.
Investment decisionSending your line Process Infographic Step five
Stage 6: Foundry& Pouring
The mold can now be positioned in to a warm oven, about 1000° C( 1832° F), to heal( cristobalite) the ceramic mold and prepare it for accepting molten alloy.
The cured ceramic mold is easy to remove from the oven and molten metal is immediately placed into in to the mold cup and its own subsequent gating system, entirely completing the mold tooth cavity with metal.
ExpenseCasting Plan of action Infographic Step six
Step sete: Shell& Casting Removal
Soon after the metal has cooled to the effect , the ceramic mould shell may be broken far away from the business( s), as well as the casting( s) removed via, the now metal, tree.
The ceramic shell is brittle and typically broken free by dealing with water jets, vibration, and differing methods.
When the tree is unquestionably clean from the ceramic, the parts are taken from the gating system by either reducing off using a saw with vibration or liquid nitrogen.
ExpensesCasting Process Infographic Step eight
Step 8: Finishing
Often, the business 's gate is removed having a grinding or machining post-- cast operation.
Further finishing including heat application treatment to anneal ahead of machining, plating, or harden is normally done before final inspection and shipping to the client .
CostCasting Process Infographic Step eight
Furthermore, within the information- casting stage Aero Alloys is fully equipped to handle any finishing, if required.
Speak to us to start the casual engineering discussion with regards to your task, or request a quote inside your precision metal component and we'll get back using a proposal.
What Materials could be Investment Cast?
Aero Alloys can make precision metal parts through investment casting using just about any metal. However, the advanced excellent materials we most often utilize , include:
Stainless
Metal
Ductile Iron
Be (symbol)Copper
Pennie-- Based
Aluminium lightweight
Co (symbol)- Centered
Water piping- Based
What is normally Investment Casting Useful for?
The cost casting process is fairly beneficial designed for casting metals with good burning temperatures that can't be cast, pressure casted, or molded on plaster or sand. Typical expense castings include parts with organic geometries, such as for example turbine cutting blades, firearm components, marine parts, as well as other commercial components.
What will be the benefits of Investment Spreading?
There are numerous benefits associated with investment casting inside the manufacturing of precision metal parts, some of such as:
Molddesign versatility
Elevatedcomplex style features
Offers up a softer surface( 125 RMS)
Highly correct, repeatable- designs
Moment& cost benefits versus fabrication and machining
Produces numerous of00 products
A multitude of00 metallic alloys may be used