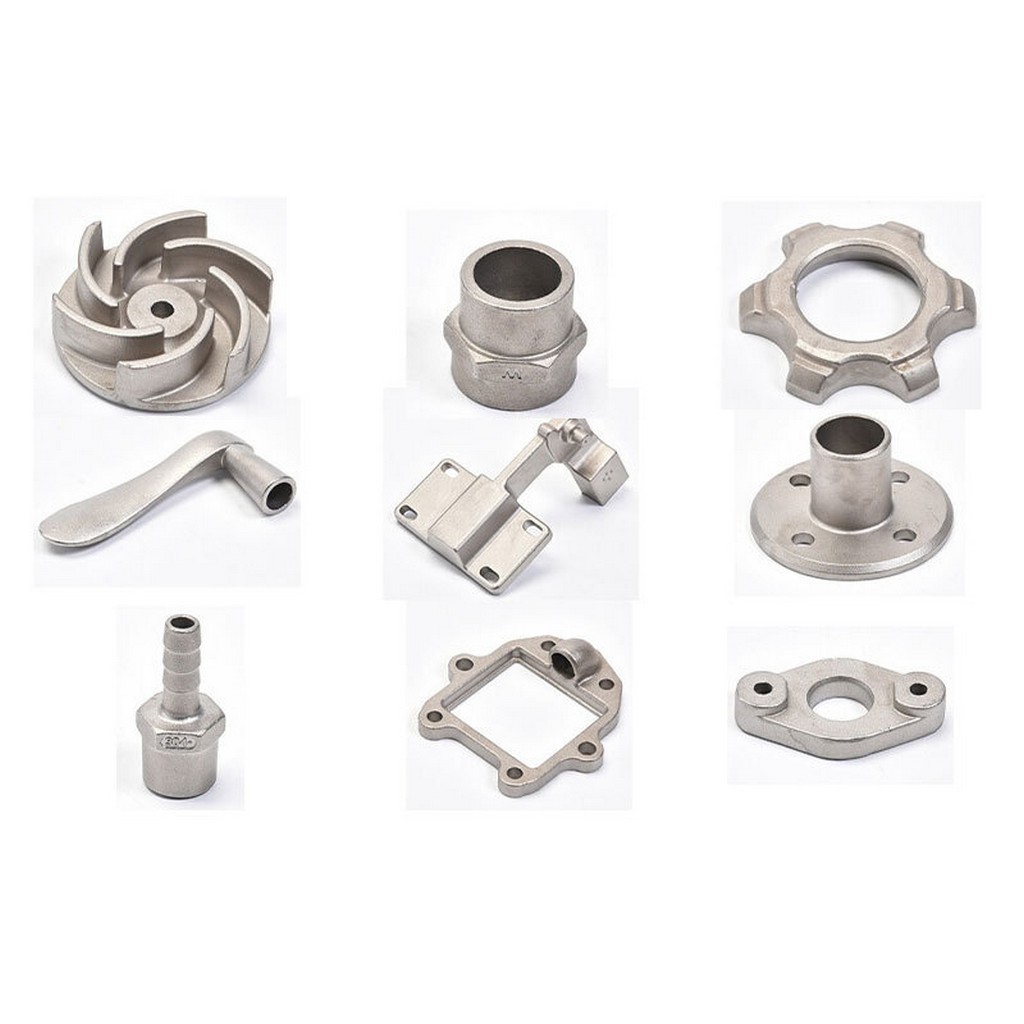
In terms of producing, every component must meet its exact specifications to produce a final product. Right now there are numerous processes offered to make necessary parts unique to a products or services , but investment casting is one method that stands above others in a number of ways.
Investment casting is a vintage way to make metal using minimal machinery and energy. It is best for producing intricate parts, which is still beneficial in today 's commercial environment.
This website will clarify why this old- world metal forming technique stages hard use and how various industries apply it today.
What's Investment Casting?
The metal forming process referred to as investment casting goes almost 5, 000 years. Others just for this system include lost- wax casting and precision sending your line. Manufacturers use this method to accurately cast metals with a high temperature tolerance by using a plastsorter, plastic, or ceramic mold along with a wax pattern that touches away.
Investment casting is good for creating precise components with original shapes that want tighter tolerances more enhanced surface finishing.
Your ownGlance within the Investment Casting Method
The pattern and mold building process sets investment casting from one another from the other metal fabrication methods like die and sand spreading.
Here is a break down of the procedure:
A design engine motor first the wax routine by using a metal injection die. The pattern could have everything for a piece or percentage of the finished part good results . slightly larger proportions to take into account thermal shrinkage.
Next, the engineer creates the runner and gating system by connecting multiple patterns to form the last component. Molten sheet metal will flow from the athlete system because it fills major inside the mold, developing a well- balanced casting. Gates would be the openings involving the athlete plus the cavity that bottles molten metal in the area.
When the complete pattern is complete, it's dipped into a tough slurry and covered with crushed stone stucco. The style engineer repeats the dipping process before cover achieves the right thickness. Now, the dried shell 's sturdiness is sufficiently strong to resist heat from your molten steel. Also, it's going to retain their form over the last step.
The wax dissolves under great heat, and trace sums soak in to the plaster or ceramic mold. The void remaining from the melted wax style will soon be filled up with an alloy to make a specific metal casting.
How s Purchase Casting Used Today?
This spreading process is great for creating services prototypes. It offers wide- spread applications across various industries, mainly the automotive and commercial industrial sectors.
So, what is the better metal for casting? Well, how different industries utilize the diffusion today be determined by the alloys they require, but refractory materials with good melting points might be best.
AluminiumAlloy
Design designers use such material probably the most in investment castings. A combined mix of aluminum, silicon, and magnesium is sufficiently strong to produce premium automotive components, but casters likewise use the alloy for electronics and commercial equipment.
Stainlesss steel
Steel is recognized for their durability, this is the reason this number of metal is an ideal choice for various components. Casters utilize this materials to craft many methods from parts to club heads. To obtain a total revision of the benefits of stainless investment casting, read another article we published here.
VosBlend
Metalworkers consider ti alloy when discovering castings that must be sufficiently strong to not fracture when very low crack. By exampling , golf clubs and marine components are a typical choice for titanium diffusion.
Benefits of Investment Casting
That method is good for crafting small, complex geometric shapes that have elaborate features with one mold.
Purchase casting is versatile. Mainly since you can combine multiple feel patterns to produce one unique mold, you can configure parts may very well not make having a machine or tools, that makes it an advisable choice to weldments.
Dimensional accurate and smooth finishes is also benefits of this casting method. The casters make up the ceramic cover around even patterns, leaving no parting line since one mold the actual casting, not two. In this way an easy finish averaging of a hundred and twenty- five micro finish, but post- process smoothing can perform a much more refined finish, if possible.
Several other great things about investment casting include:
Recylable Materials: Design engineers can recycling the melted wax the other point is pattern. They will recycling the mold, because of its durability.
Tight Tolerances: Investment casting may have a tolerance of. 003″, which can be tighter than most casting processes such as for instance perish casting.
Design Capabilities: With investment casting, design engineers can integrate identifying markers towards the sending your line, such as for instance numbers, logos, and product IDs.
Drawbacksof Purchase Casting
Regardless of the beneficial characteristics of lost- wax sending your line, it'll have its drawbacks. The most important disadvantage is the type limitation. Because so few design engineers can deliver large parts using this system, it is probably not to choose for complaintant who must fabricate a bulky part.
This technique ideal casting small intricate components. Parts exceeding 75 pounds are better suited to other casting methods.
Investment casting shells have constraints on the size and range. They cannot be less space-consuming than 1. 6 mm or deeper than 1. 5 times the dimension. In case your casting design requires cores and can unfit these requirements, you may want to seek another process.
This plan is more difficult than every other casting processes, and it takes a lot of preparation and specialised equipment. Due to this , the upfront expense of investment casting can cost more than sand spreading or die casting, but the availability cost per unit diminishes with larger orders.
Start A fantastic Investment Casting Project Today With TFG United states of america
Investment spreading might have roots dating again 5, 000 years, however it continues to have beneficial applications in females. Around the world , industries depend on precision spreading to make intricate components with smooth finishing, unique geometric styles, and tight tolerances, including the economic,, automotive, firearm, food control equipment, and agricultural equipment developing industries.
The XIEJIN Usa offers superb investment casting services.
We use specialized shell making and wax processing equipment to fabricate patterns and cast quality components quickly. If you desire to learn more about our investment casting services and get a free quote on your own approaching project, contact we today.
The Investment Casting
Method
Joseph Electronic. Fritz
ProfessionalDirector
Expense
GrowingInstitute
Back ground
Actuallydeveloped by just ancient Chinese and Egyptian
customto create artwork
Mainlyused meant for art until progress the jet turbine
motorat the conclusion of World War 2
Ever since that time it is now a great enabling technology on
these days's best industries
Aeronauticaland Defense
Electrical power Generation
Automobile
Fueland oil
AreaSearch
Health care/ Orthopedics
Culture
Creating
Industrialand
Buyerproducts
A number of some great benefits of Expense Throwing
Excellentsurface finish
Lot of different metals
Complex, near to net geometries
Info
The cost Casting Process
Building a Wax Design
In today 's manufacturing world, polish patterns are usually developed by
managingwax in to a metal device or "die"
With the emergences of Additive Manufacturing, patterns might be imprinted
Within the artwork community, unique pieces are carved with the artist
throughwax blocks
Meant for multiple castings, a silicon device is usually created from the artist 's sculpture
in addition towax is shot or poured in to the cake you produced tooth cavity
PolishTree Create
It will always be typically uneconomical to create chunks individually ,
as a resultwax patterns usually are mounted on a wax "sprue"
The particularsprue serves two purposes
1. Gives an installation surface to build multiple patterns into 1
mold, that will be afterwards full of alloy
2. Provides flow path for your molten alloy to the gap produced by the polish
design and style( s)
They'rewax between design( s) plus the sprue they're called "Gates",
simply because they throttle the direction and flow in the alloy in to the void
made by the look
CoveringEstablishing
The next phase in the act should be to build a hard shell
round the wax woods
This specificshell will eventually become the mold that metal is generally
addedinto
To create the shell, the tree is dropped in to a ceramic bath or "slurry"
After dipping, sand or maybe "stucco" is placed on the wet surface
The mold is normally in order to dry, plus the strategy is repeated several in
times until a layered( or laminated) ceramic mold, capable to endure
the stresses from the casting process, remains built
Dewax/ Burnout
Before pouring metallic to the mold, the polish is removed
This is usually done by using a steam-- dewax autoclave,
which can be like a large, commercial pressure oven
Another technique conditions good flash fire oven, which will
detailsand burns the polish
Severalfoundries use both strategies in agreement
Autoclave removes a lot of the wax, which will might be reconditioned and
utilizedagain
Flash fire burns up recurring wax and cures the covering, readying it for casting
Stainlesss steelFlowing
Prior to the metal is generally poured in the ceramic mold or simply
"shell", the mold is preheated to a certain temperature
to avoid the molten alloy via solidifying or "freezing off"
before the whole mold is packed
Blendis melted in a great ceramic cup( known as crucible) utilizing a
procedureknown because induction melting
A higher level of recurrence household current makes a magnet field about
the alloy, generating electric fields inside the metallic( eddy currents)
The particulareddy power heat the alloy due to the fabric 's electrical resistance
When the alloy reaches its specified heat, it really is poured in to the
mold, plus the mold is permitted to cool
CoveringKnock Away
Once cool, the shell materials is taken from the steel
This is normally done through mechanical means
Sort
HigherForce Water Blast
Vibratory Table
Covering removal may also be performed chemically, by using a warmed
caustic solution of either potassium hydroxide or sodium hydroxide,
neverthelessthis type of approach has been phased away because of environmental and
health and fitnessconcerns
Stop
When the shell material have been eliminated, the parts are
reduceaway the sprue along with the gates are in fact ground off
Componentcut away can be achieved manually
Slicenoticed
Flashlight
Laserlight( limited applications)
Parts are often slice off using automation, that could be , the mold may be
anchoredhaving a fixture over a programmable slice off noticed
PersonCastings
If the parts are removed from the sprue, as well as the entrance removed,
the outer lining may become finished using numerous means
Vibratory/ Media finishing
Belting or hands grinding
Perfecting
Finishing can become done manually, but on many it is actually automated
Parts are then inspected, marked( if required), packaged and shipped
With regards to the application, the parts can be utilized in his or her "net
condition "or undergo engineering for precision mating surfaces
Review
From Egypt and China to present day manufacturing, expense
tossinghas started out an artwork into a top technology enabler
On our daily lives, investment is found everywhere