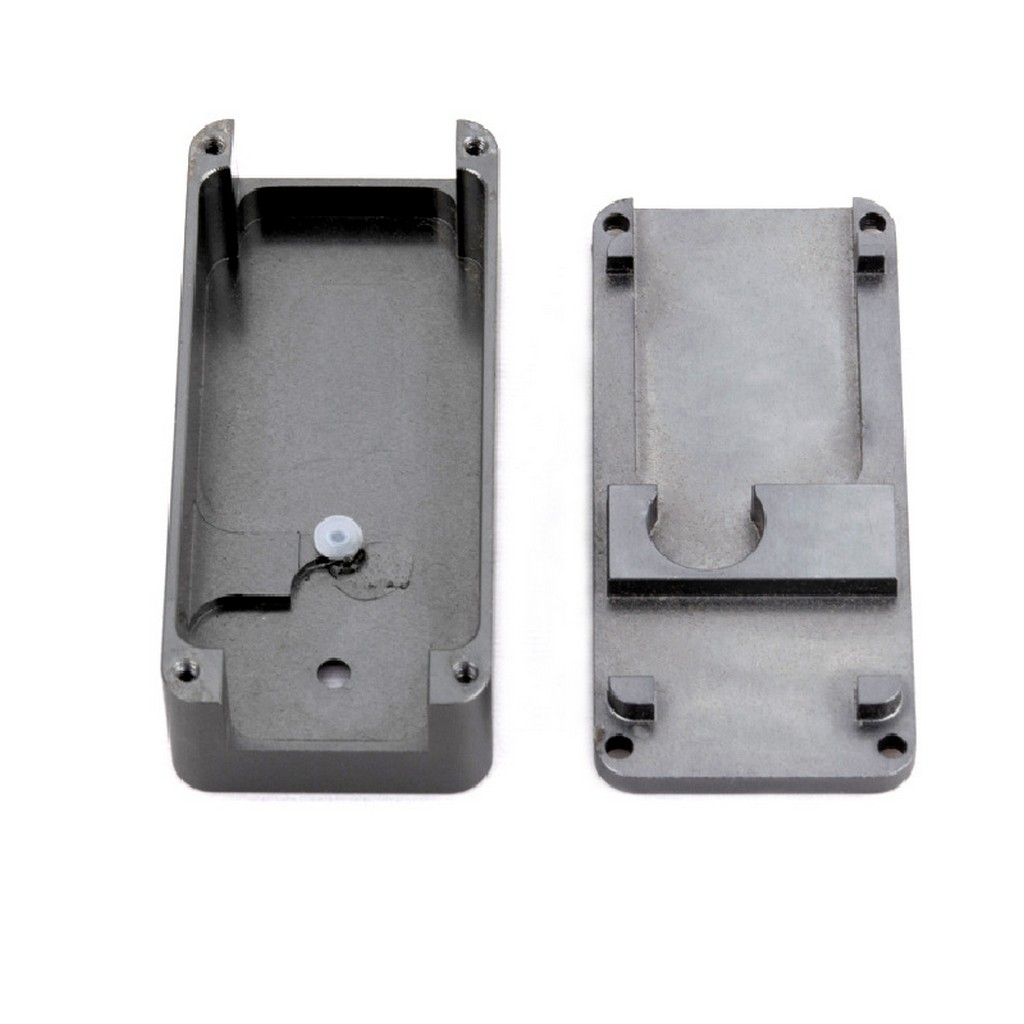
Your momentary initial pattern is made of wax. The mould, or possibly investment, is made by dipping the wax pattern into a price- added tax of refractory slurry, which confirms around the outside the wax pattern. This technique is certainly repeated until the mandatory wall membrane thickness is achieved. The first wax pattern then can be melted apart, leaving a hollow mould when to cast the smelted metal.
A newdiagram which remarks the investment sending your line
Manufacture:
An alternative choice to cover moulding, die casting and forging.
Rubber, or epoxy, resin adjusts used to make patterns to have small, delicate components, although dimensional accuracy and mildew life will undoubtedly be much lower than for the higher priced steel dies applied in longer production runs.
Economical production numbers vary widely, since outlined by component material, style and design and kind of die. Production works inside the variety of 50–10 million dollars are certainly not unusual.
Due to substantial tooling, material and process costs, production is usually only feasible if you find no ideal alternative( e. g. turbine rotor blades in unforgeable alloys), or wherever an appreciable decrease in engineering may be accomplished ( e. g. hip prostheses).
Production rates rely on material and component style , but are often slow scheduled to the various stages engaged. Automatic investment, drying and dewaxing stages can increase production costs.
Water- soluble ceramics which is frequently stripped in a matter of 62 s can increase production costs, but are best suited with alloys whose melting point is unquestionably <1200? C.
For reactive alloys such as for instance titanium, shedding and casting could be completed under vacuum.
Machinable waxes as well available for one- away prototypes, before expensive tooling is certainly made.
The "Mercast" process uses mercury, which may be eventually frozen, wax to make the pattern. Unlike the wax, the mercury isn't lost about melting, and the method is certainly with the capacity of giving better area finishes and accuracy of details. However, you can find negative effects associated with the procedure.
The "block mould process" is frequently your less expensive process for light castings. Moulds include series small components, and so are centrifugally cast.
Materials:
Virtually all materials and alloys may be purchase cast, but the method is certainly suitable to those supplies which can be challenging to die ensemble, forge or machine.
Reactive supplies may need to be vacuum pressure melted and cast, and substantial melting point materials, such since titanium, take advantage of your carbon investment the standard refractory.
Refractory investments vary in line with the material being cast, nevertheless are graded and chosen during so that it will minimise metal/ mould tendencies, to reduce cracking during firing aswell to provide enough mechanical strength.
Poor melting point materials( <1200? Significantly more), that are used during conjunction using a water supports soluble investment, have now been produced to obtain mechanical properties comparable with those through the significantly more conventional ferrous alloys. These low melting point materials are significantly more expensive, but give better area finish and dimensional tolerance.
Most materials bring about the characteristic defects connected to an since- cast structure, such since porosity, segregation, heterogeneous grain framework, etc.
Porosity may be eradicated by HIPing where necessary, in the. g. to boost fatigue property of turbine blades and prostheses. Structural defects can be applied for by heat application treatment where important.
Design:
Ideal to tiny, complex, 3D elements beginning your few grams to five kg, although elements around 100 kilogram might be produced.
Re- competitor angles are possible, but intricate internal undercuts are merely likely using a soluble hard investment, with low melting level materials.
The minimum hole dimension is around 1. 5 logistik, with tolerances from the buy of ±0. 13 mm as much as 25 mm. The truth thatdepth/ diameter ratio of blind holes should be <2, and the fact for through holes <5.
One of the leading top features of the procedure certainly is the since- cast surface finish, which depends on the materials employed for the investment as well as the component. Typical values will be given just below.
Minimum wall density depends on flow miles and materials. Although wall thicknesses of 0. 25 mm have been achieved, the accepted inexpensive minimum is in the gathering 0. 75–1. 5 mm.
Most affordable production costs are achieved with tolerances of ±0. 25 logistik, and inside the gated location tolerances can never be under this.
Linear tolerances depend on material, and component proportions and geometry. Typical values will soon be the following( for 100 logistik diameter):
Ferrous materials ±0. looking for millimeter
Non- ferrous supplies ±0. 4 mm
Straightness will depend on component dimensions, nevertheless is from the order in ±1% of component length.
Patience on external and internal radii with all the order of ±0. 40 mm per 25 logistik of radius.
Accuracy of moulded angles depends largely on part design, but is usually present in the number ±0. 5–1. zero?.
MetallicRa( μm)
Investment decisionensemble Machined
Aluminium lightweightalloys
0. almost eight- 2. 6
1. zero- 2. 6
Copper mineralgold and silver coins
1. 5- 2. 6th
1. 0- 2. 6th
Metalsteels
2. 3 supports 3. 2
1. 5 supports 3. 2
Co (symbol)- stainless- alloys
2. 1- a few . 6
1. 3- several . 6
Co2steels
2. three or maybe more- 3. 2
1. several- 3. 2
Lowerblend steels
2. 5- three or even more. 8
1. 5- three or even more. 2